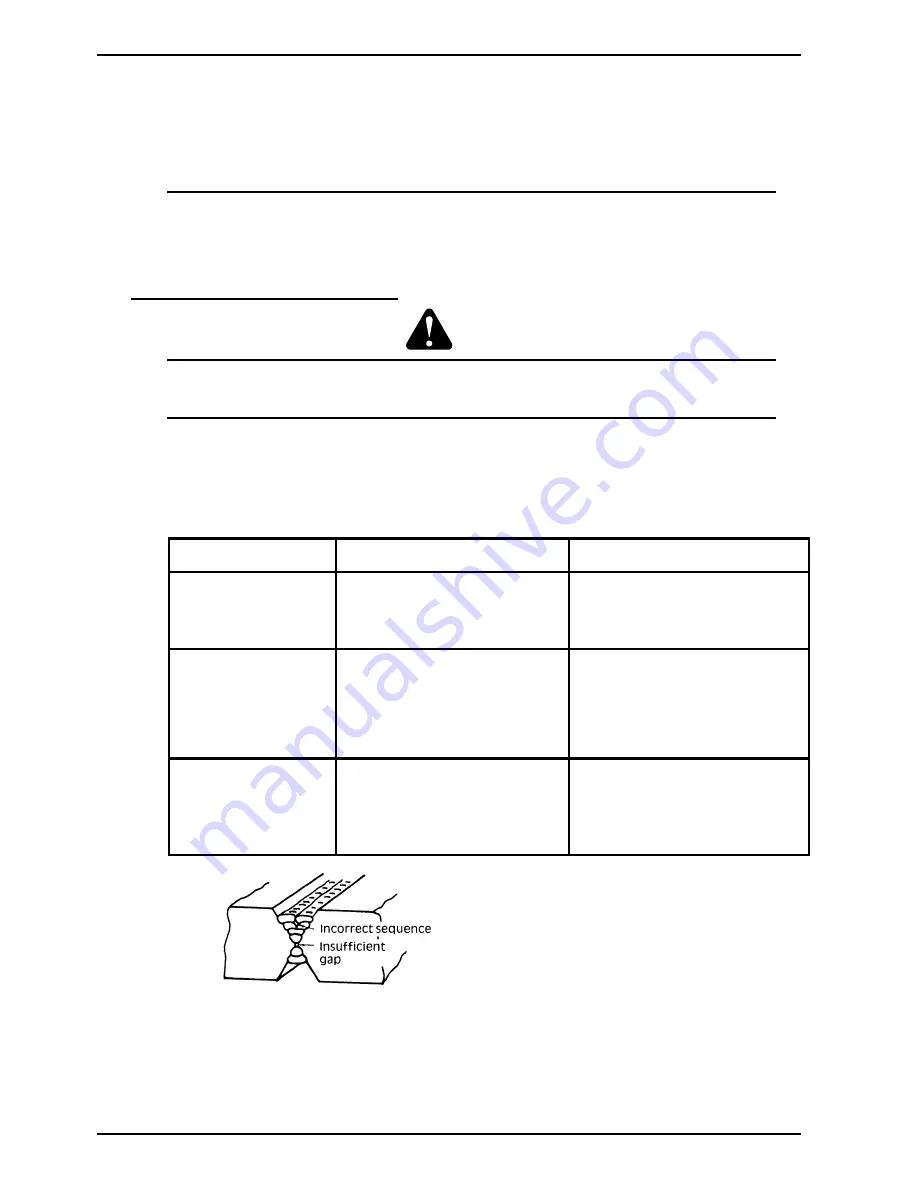
HD Manual Arc Welders
©2000 CIGWELD All rights reserved
28
13.1 Cleaning the Welding Power Source
Refer to
WARNING 5
. To clean the Welding Power Source, open the enclosure and use a
vacuum cleaner to remove any accumulated dirt, metal filings, slag and loose material. Keep
the shunt and lead screw surfaces clean as accumulated foreign material may reduce the
welders output welding current.
CAUTION 3
Do not use compressed air to clean the Welding Power Source. Compressed air can force metal particles
to lodge between live electrical parts and earthed metal parts within the Welding Power Source. This may
result in arcing between this parts and their eventual failure.
14. BASIC TROUBLESHOOTING
WARNING 6
There are extremely dangerous voltage and power levels present inside this product. Do not attempt to
open or repair unless you are a qualified electrical tradesperson and you have had training in power
measurements and troubleshooting techniques.
If major complex subassemblies are faulty, then the Welding Power Source must be returned to an
Accredited CIGWELD Service Agent for repair. The basic level of troubleshooting is that which can
be performed without special equipment or knowledge.
14.1 Welding Problems
FAULT
CAUSE
REMEDY
1 Gas pockets or voids in
weld metal (Porosity).
A
B
C
Electrodes are damp.
Welding current is too high.
Surface impurities such as oil,
grease, paint, etc.
A
B
C
Dry electrodes before use.
Reduce welding current.
Clean joint before welding.
2 Crack
occurring
in
weld metal soon after
solidification
commences
A
B
C
Rigidity of joint.
Insufficient throat thickness.
Cooling rate is too high.
A
B
C
Redesign to relieve weld joint of
severe stresses or use crack
resistance electrodes.
Travel slightly slower to allow
greater build up in throat.
Preheat plate and cool slowly.
3 A gap is left by failure
of the weld metal to fill
the root of the weld.
A
B
C
Welding current is too low.
Electrode too large for joint.
Insufficient gap.
A
B
C
Increase welding current
Use smaller diameter
electrode.
Allow wider gap.
D Incorrect sequence.
D Use correct build-up sequence.
Figure 28 - Example of insufficient gap or incorrect sequence