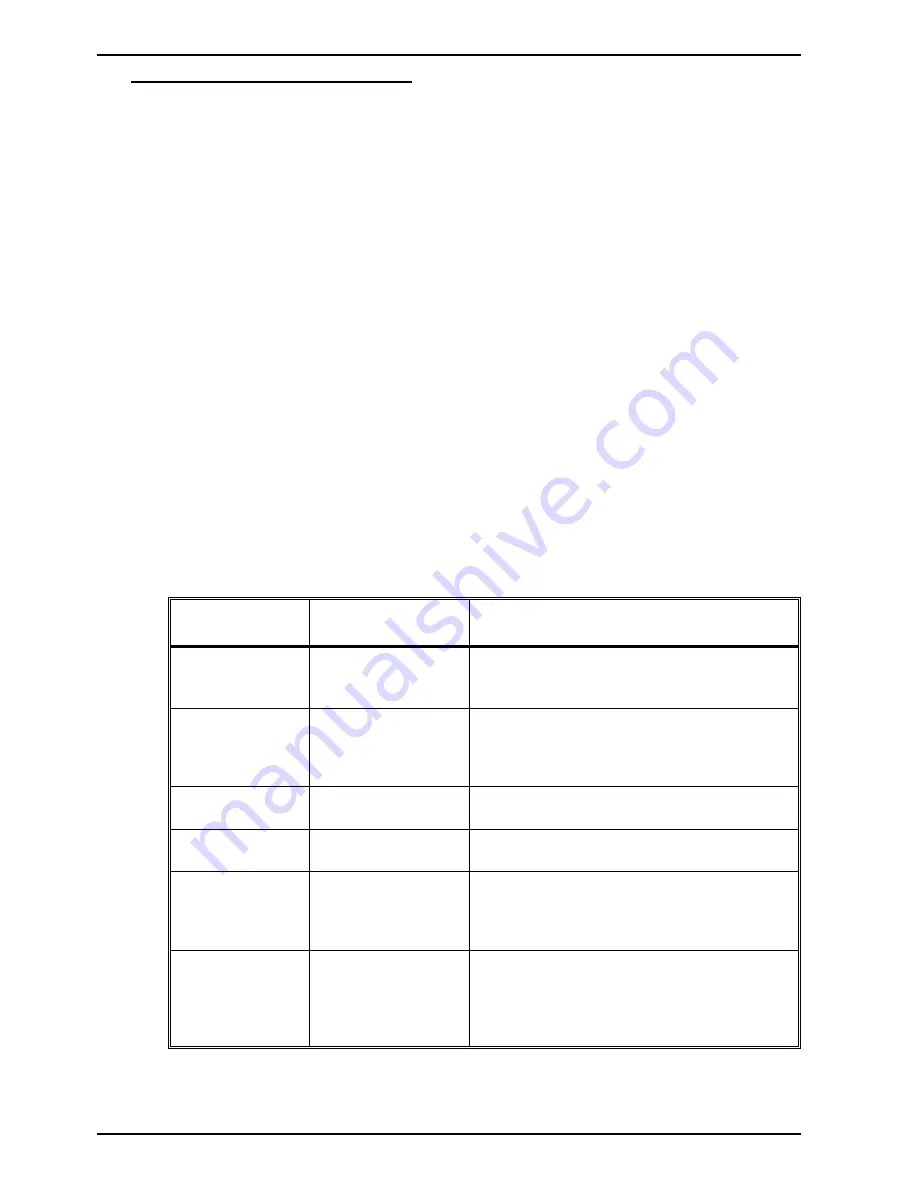
HD Manual Arc Welders
©2000 CIGWELD All rights reserved
18
9. ARC WELDING ELECTRODES
Metal arc welding electrodes consist of a core wire surrounded by a flux coating. The flux coating is
applied to the core wire by an extrusion process.
The coating on arc welding electrodes serves a number of purposes:
a) To provide a gaseous shield for the weld metal, and preserve it from contamination by
the atmosphere whilst in a molten state.
b) To give a steady arc by having ‘arc stabilisers’ present, which provide a bridge for
current to flow across.
c) To remove oxygen from the weld metal with ‘deoxidisers’.
d) To provide a cleansing action on the work piece and a protective slag cover over the
weld metal to prevent the formation of oxides while the metal is solidifying. The slag
also helps to produce a bead of the desired contour.
e) To introduce alloys into the weld deposits in special type electrodes.
9.2 Types
of
Electrodes
Arc Welding electrodes are classified into a number of groups depending on their applications.
There are a great number of electrodes used for specialised industrial purposes which are not of
particular interest for everyday general work. These include some low hydrogen types for high
tensile steel, cellulose types for welding large diameter pipes, etc.
The range of electrodes dealt with in this publication will cover the vast majority of
applications likely to be encountered; are all easy to use and all will work on even the most
basic of welding machines.
Metals being
joined
CIGWELD
Electrode
Comments
Mild steel
Satincraft 13
(AS/NZS E4113-0)
Ideal electrodes for all general purpose work.
Features include out standing operator appeal,
easy arc starting and low spatter.
Mild steel
Ferrocraft 21
(AS/NZS E4818-2)
All positional electrode for use on mild and
galvanised steel furniture, plates, fences, gates,
pipes and tanks etc. Especially suitable for
vertical-down welding.
Cast iron
Castcraft100
Suitable for joining all cast irons except white cast
iron.
Stainless steel
Satincrome 318-16
(AS/NZS E316L-17)
High corrosion resistance. Ideal for dairy work,
etc. On stainless steels.
Copper, Bronze,
Brass, etc.
Bronzecraft
(AS/NZS E6200-A2)
Easy to use electrode for marine fittings, water
taps and valves, water trough float arms, etc. Also
for joining copper to steel and for bronze overlays
on steel shafts.
High alloy steels,
Dissimilar metals,
Crack resistance,
All hard-to-weld
jobs.
Weldall
(AS/NZS E312-17)
Weldall does truly what its name states. It will
weld even the most problematical jobs such as
springs, shafts, broken joins mild steel to stainless
and alloy steels.
Not suitable for Aluminium.
Table 2 - Types of Electrodes