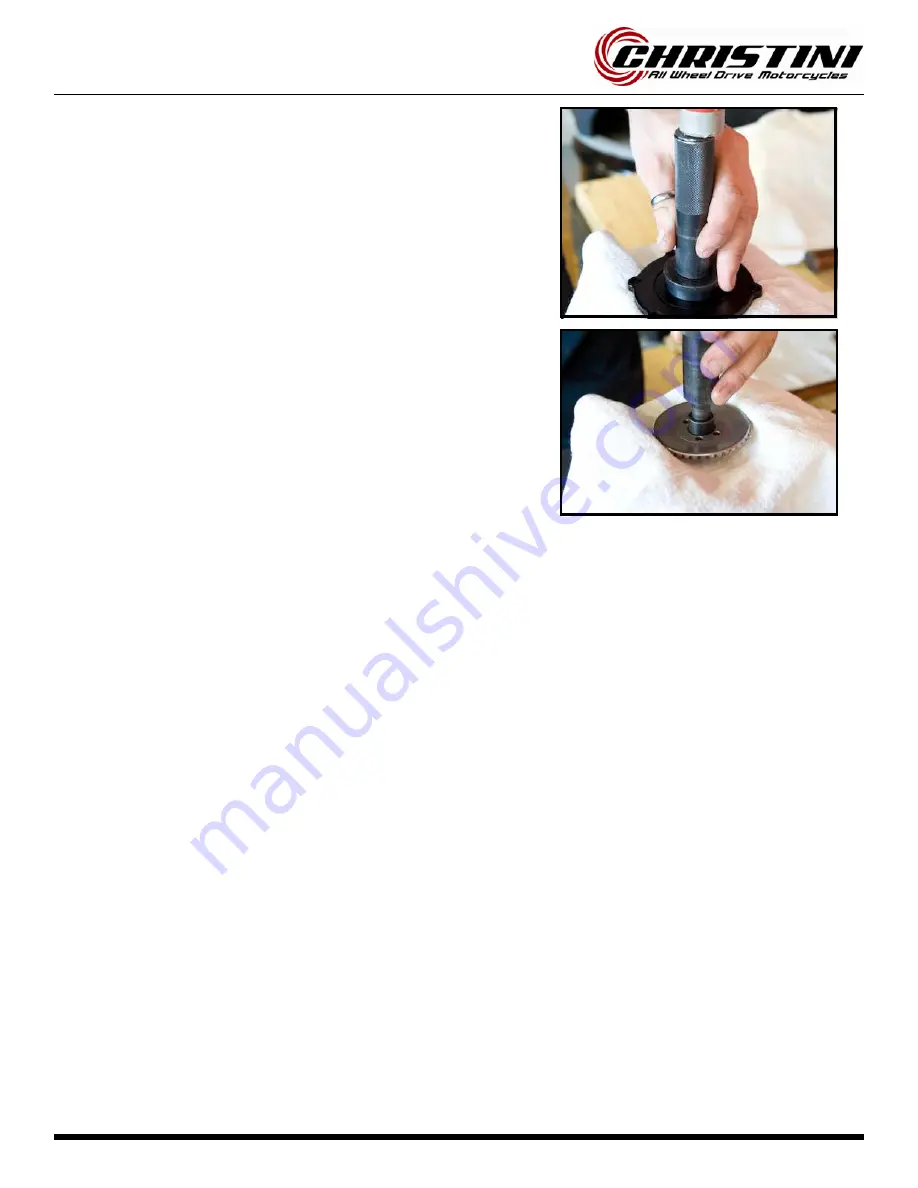
Page 65
•
Remove cover bearing with bearing removal punch. Note o-ring lip
near inner race of bearing is easily damaged. Only apply pressure
to inner race of bearing.
•
Remove drive insert from gear with hammer and bearing removal
tool.
•
Before reassembly of dropouts, all parts must be cleaned and
inspected individually for damage or wear. Parts can be cleaned
with solution no different then OEM fork. Be sure to blow dry
dropouts and parts prior to reassembly if cleaning solution is used.
•
Pinion and bevel gear must be replaced as a set.
•
If bearings are seized or hard to turn by hand they must be
replaced or cleaned and repacked with grease.
•
Be sure to grease all o-rings and gears during reassembly.
Dropout Service
Содержание AWD 450E
Страница 1: ...Service Manual CHRISTINI AWD 450E Christini Technologies Inc tech christini com Version 2015 1 ...
Страница 2: ......
Страница 34: ...Page 33 Maintenance ...
Страница 35: ...Page 34 AWD Service Section AWD Service ...
Страница 37: ...Page 36 AWD Detail Illustration ...
Страница 42: ...Page 41 Cover and Chain Removal ...
Страница 43: ...Page 42 Cover and Chain Removal ...
Страница 46: ...Page 45 AWD Engagement Disengaged AWD System Pull and Push with one finger to Engage Engaged AWD System ...
Страница 53: ...Page 52 Front Wheel Service ...
Страница 62: ...Page 61 Dropout Service ...
Страница 71: ...Page 70 Fork Spline Bearing Service ...
Страница 80: ...Page 79 Triple Clamp Service ...
Страница 81: ...Page 80 Triple Clamp Service ...
Страница 96: ...Page 95 Head Tube Bearing Service Picture above shows a head tube not welded to the frame for reference ...
Страница 104: ...Page 103 Gear Box Service ...
Страница 105: ...Page 104 Slide clutch basket off output gear Remove output seals from gear box Remove output snap ring Gear Box Service ...
Страница 110: ...Page 109 Clutch Service Clutch Service ...
Страница 117: ...Page 116 Warranty ...
Страница 118: ......