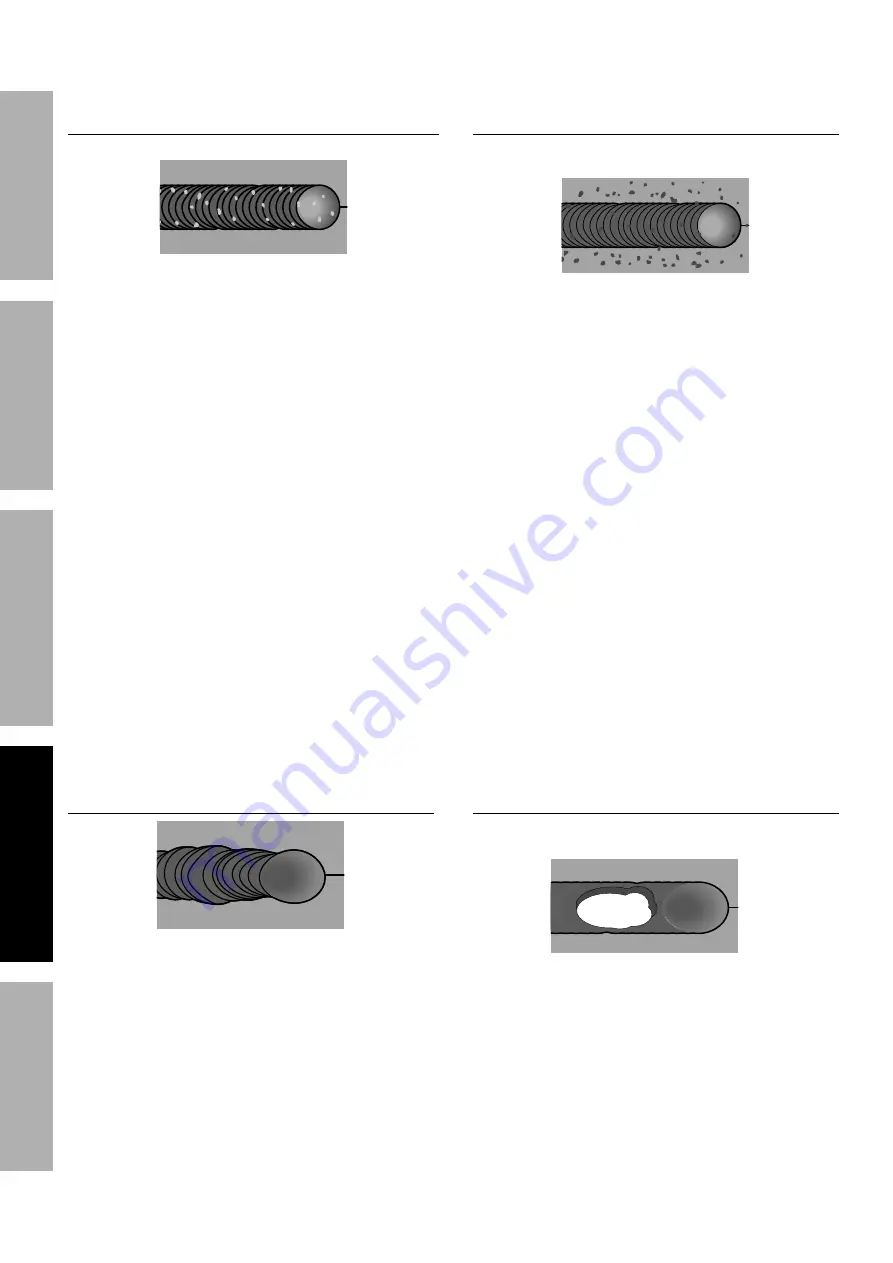
Page 26
For technical questions, please call 1-888-866-5797.
Item 62181
SAFETY
MAINTENANCE
BASIC WELDING
WELDING TIPS
SETUP
Burn-Through
Base material melts away,
leaving a hole in the weld.
POSSIBLE CAUSES AND SOLUTIONS
1.
Workpiece overheating:
Reduce current and/or wire feed speed.
2.
Welding speed too slow:
Increase welding speed and ensure
that welding speed is kept steady.
3.
Excessive material at weld:
Reduce wire feed speed.
TOP
VIEW
Crooked/Wavy Bead
POSSIBLE CAUSES AND SOLUTIONS
1.
Inaccurate welding:
Use two hands or rest hand on steady surface.
2.
Inconsistent welding speed:
Maintain steady weld speed.
3.
Stickout too long:
Reduce stickout.
TOP
VIEW
Porosity
Small cavities or holes in the bead.
POSSIBLE CAUSES AND SOLUTIONS
1.
Incorrect polarity:
Check that polarity is set correctly
for type of welding.
2.
Insufficient shielding gas (MIG only):
Increase flow of gas.
Clean nozzle.
Maintain proper stickout.
3.
Incorrect shielding gas (MIG only):
Use shielding gas recommended by wire supplier.
4.
Dirty workpiece or welding wire:
Clean workpiece down to bare metal.
Make certain that wire is clean and free
from oil, coatings, and other residues.
5.
Inconsistent welding speed:
Maintain steady weld speed.
6.
Stickout too long:
Reduce stickout.
TOP
VIEW
Excessive Spatter
Fine spatter is normal.
Spatter that is grainy and large is a problem.
POSSIBLE CAUSES AND SOLUTIONS
1.
Dirty workpiece or welding wire:
Clean workpiece down to bare metal.
Make certain that wire is clean and free
from oil, coatings, and other residues.
2.
Incorrect polarity:
Check that polarity is set correctly
for type of welding.
3.
Insufficient shielding gas (MIG only):
Increase flow of gas.
Clean nozzle.
Maintain proper stickout.
4.
Wire feeding too fast:
Reduce wire feed speed.
5.
Stickout too long:
Reduce stickout.
TOP
VIEW