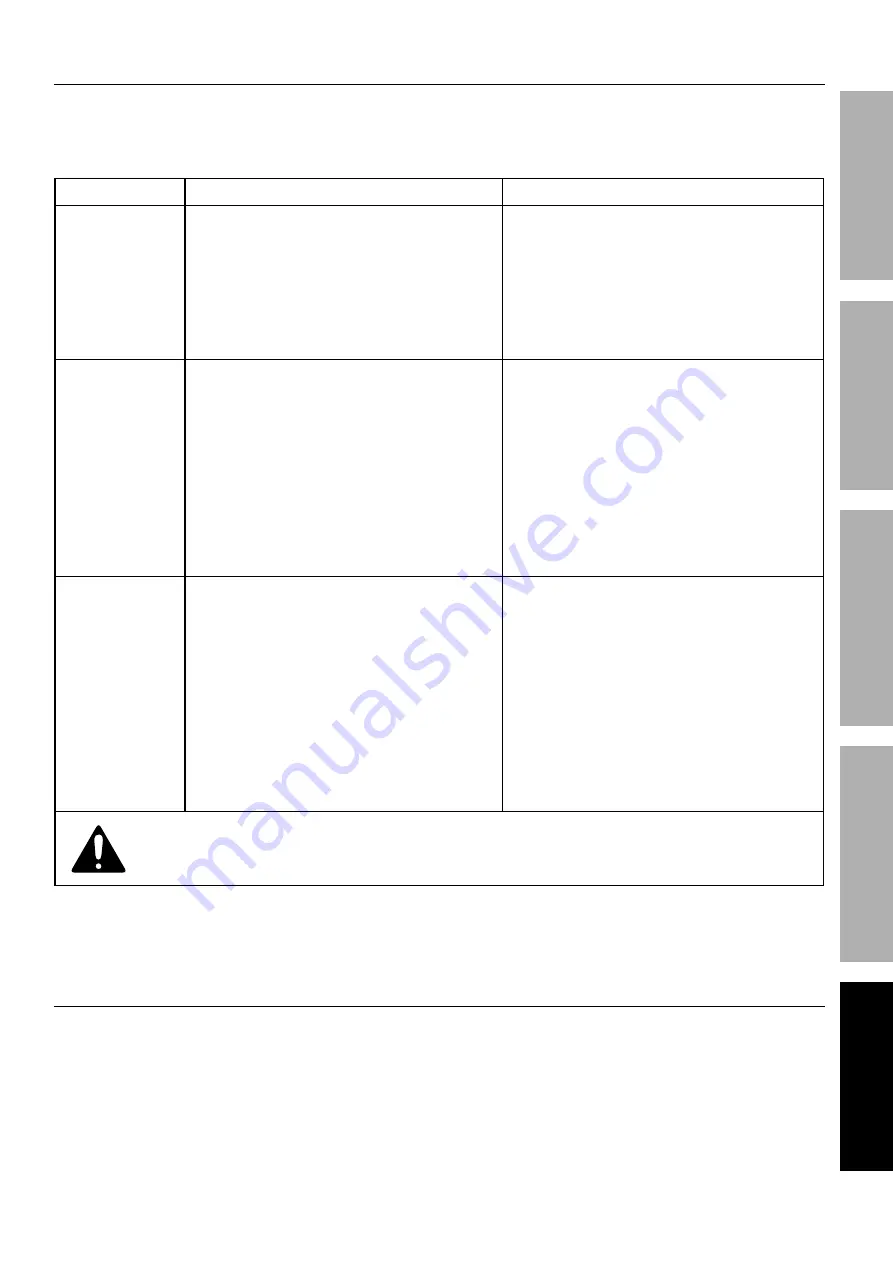
Page 29
For technical questions, please call 1-888-866-5797.
Item 62181
SAFETY
MAINTENANCE
BASIC WELDING
WELDING TIPS
SETUP
PLEASE READ THE FOLLOWING CAREFULLY
THE MANUFACTURER AND/OR DISTRIBUTOR HAS PROVIDED THE PARTS LIST AND ASSEMBLY DIAGRAM
IN THIS MANUAL AS A REFERENCE TOOL ONLY. NEITHER THE MANUFACTURER OR DISTRIBUTOR
MAKES ANY REPRESENTATION OR WARRANTY OF ANY KIND TO THE BUYER THAT HE OR SHE IS
QUALIFIED TO MAKE ANY REPAIRS TO THE PRODUCT, OR THAT HE OR SHE IS QUALIFIED TO REPLACE
ANY PARTS OF THE PRODUCT. IN FACT, THE MANUFACTURER AND/OR DISTRIBUTOR EXPRESSLY
STATES THAT ALL REPAIRS AND PARTS REPLACEMENTS SHOULD BE UNDERTAKEN BY CERTIFIED AND
LICENSED TECHNICIANS, AND NOT BY THE BUYER. THE BUYER ASSUMES ALL RISK AND LIABILITY
ARISING OUT OF HIS OR HER REPAIRS TO THE ORIGINAL PRODUCT OR REPLACEMENT PARTS
THERETO, OR ARISING OUT OF HIS OR HER INSTALLATION OF REPLACEMENT PARTS THERETO.
Problem
Possible Causes
Likely Solutions
Power switch
lights, but welder
does not function
when switched on
1. Tripped thermal protection device.
2. Faulty or improperly connected Trigger.
1. Stop welding and wait about 8-10 minutes
with the Power Switch ON for the welder
to cool. Reduce duration or frequency
of welding periods to help reduce wear
on the welder. Refer to Duty Cycle
(Duration of Use) on page 17.
2. Qualified technician must check
and secure/replace Trigger.
Power switch
does not light
when switched on
1. Unit is not connected to outlet properly.
2. Outlet is unpowered.
3. Circuit supplies insufficient input voltage or
amperage.
4. Plug does not have correct rating.
1. Verify the voltage at the outlet and
the connection to the outlet.
2. Check circuit breaker/GFCI devices;
if any are tripped, determine and
remedy cause before resetting.
3. Verify that the circuit is designed to supply
the required input voltage and amperage
as detailed on the Specifications table.
4. Make sure installed plug is correct
rating (250 VAC, 50A recommended)
- see Specifications on page 7.
Wire feeds, but
arc does not ignite
1. Improper ground connection.
2. Improperly sized Contact Tip.
3. Excessively worn Contact Tip.
4. Dirty Contact Tip.
1. Make certain that the workpiece is
contacted properly by the Ground
Clamp and that the workpiece is
properly cleaned near the ground
clamp and the welding location.
2. Verify that Contact Tip is the proper
size for welding wire. If needed, replace
Contact Tip with proper size and type.
3. Check that the hole in the tip is not
deformed or enlarged. If needed, replace
Contact Tip with proper size and type.
4. Properly clean Contact Tip.
Follow all safety precautions whenever diagnosing or servicing the equipment or engine.
Troubleshooting (cont’d)
IMPORTANT!
Be CERTAIN to shut off the Welder, disconnect it from power, and discharge the Torch to ground
before adjusting, cleaning, or repairing the unit.