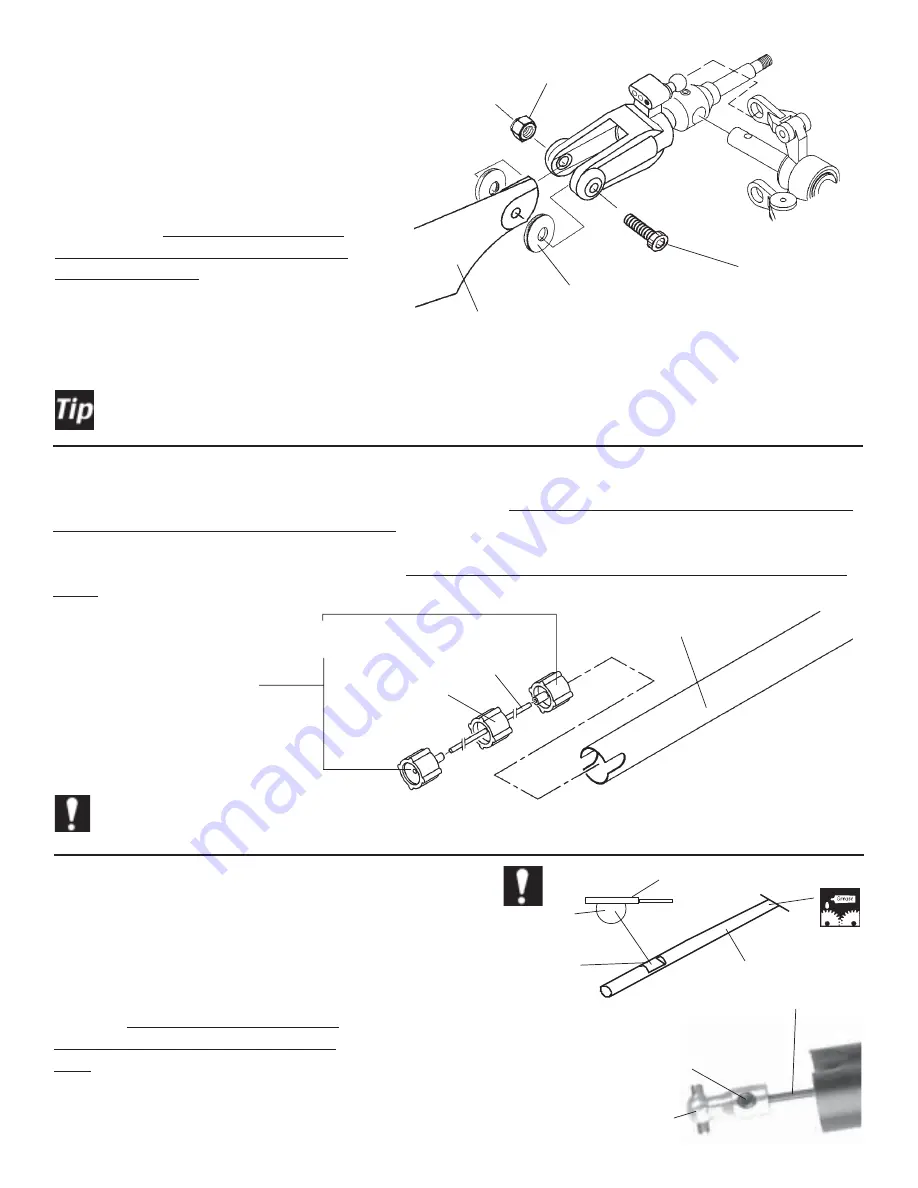
18
#HI6099
Tail Rotor
Blades x 2
M3x20 Socket
Cap Screw x 2
M3 Locknut x 2
After flying the model, if a vibration is noticed on the horizontal fin, you can remove the complete tail rotor
assembly with the hub and further balance it using a High Point balancer. Careful sanding of the rotor
blades is all that is needed.
Leading Edge
Snap the ball on the tail rotor grip into the
adjoining pitch slider link on both sides.
Install the tail rotor blades shimmed with
M3x10 plastic washers on both sides using
two M3x20 socket cap screws and M3
locknuts. Note the direction of the blades
on the diagram, the leading straight edge of
the blade should be on the same side as the
ball on the blade grip. To tension the blade
bolt, start loose and tighten until the blade
holds horizontal but pivots freely when
moved.
Step 29 Tail Blade Assembly
#HI3096A
M3x10 Plastic
Washer x 4
Insert three tail drive shaft guides on to the brass tail drive housing (note that one guide has a larger center hole than the
others, slide this one to the center of the brass tube), add the remaining two onto the ends. Glue the guides into posi-
tion using Zap Ca on the brass tube. Insert the tail shaft guide assembly into the tailboom from the end with the 2 holes
and position the assembly centered in the tailboom ( gentle tapping with a wooden dowel will easy the insertion of the
guides ).
#HW3063A
Tail Drive Shaft Set
#HW3062A
Tail Boom
Drive
Housing
( brass )
Drive Housing
Ends x 2
Make sure the brass tubing is glued to the plastic guides inside the tail boom.
Step 30 Tail Drive Shaft & Pushrod Guides
Drive Shaft
Support
Center x 1
Step 31 Tail Drive Shaft
#HW3063A
Tail Drive Shaft Set
Deepen the flat spot on
the the round end of the
Tail Drive Shaft.
File
Tail Drive Shaft
Apply Grease
For extra security, continue filing until the flat
spot is 1/3
rd
the thickness of the shaft. Thor-
oughly grease the tail drive shaft (Tip 1) and
insert the newly filed end into the tailboom end
with the slots into the drive shaft housing
assembly (ensure the end with the new flat
spot exits the tailboom end with the round
holes) and degrease both ends of the shaft.
Attach the universal tail drive coupler using
two M4x4 set screws using locktight.
#CN1076-12
Tail Drive Coupler - Male
M4x4 Set
Screw x 2