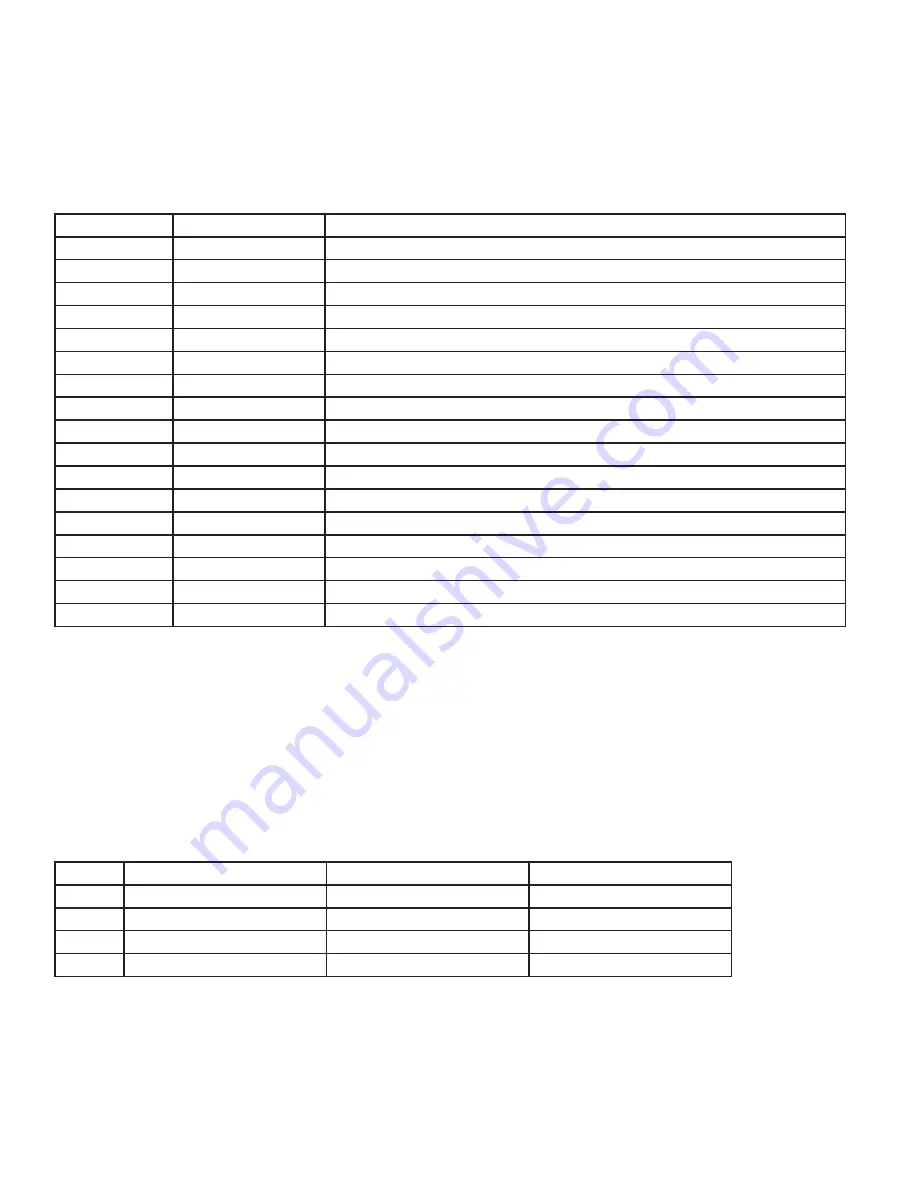
Page 24
CNC12 KP-3 configuration for Oak and Allin1DC
CNC12 V4.16+ requires a Pro or Ultimate License for Probe functionality.
Oak/Allin1DC control system parameters below are the recommended basic settings SAE Inch and Millimeters in (mm)
These are the suggested starting values. Some of these parameters are typically adjusted by the integrator/user to suit
the probing/digitizing application. F1 setup, F3 config, type in password (137), F3 parameters.
Parameter
Setting
Description
11
50769
The PLC input for the Probe signal
12
10
Tool Library number of the Probe
13
0.020 (.508)
Clearance amount nominal
14
30 (762)
Fast Probing Rate
15
3 (76.2)
Slow Probing Rate
16
5 (127)
Maximum Search Distance
18
50771
PLC input, Spindle Inhibit/probe connected
120
0.020 (0.508)
Probe stuck clearance amount
121
0.020 (0.508)
Grid digitizing minimum Z pullback
122
0.0002 (0.005)
Grid digitizing dead band distance
123
0
Radial clearance move
151
0
Repeatability tolerance
153
1
Probe protection enable
155
0
Probe type enable
186
1
Probe stuck retry disable
366
1
Probe deceleration Multiplier
Probe Jog Parameters
control operator machine jogging speeds when the probe is connected. Probe must decelerate to
stop when contacting a surface without exceeding overtravel limits. See probe specifications and set fast probing rates so
that over travel specification is not exceeded. Probe will be damaged if over travel limit is exceeded by any amount.
F1 Setup, F3 Config, F3 Machine, F1 Jog, F8 Probe Jog
Axis
Probe Slow Jog
Probe Fast Jog -
Probe Fast Job +
1
25
150
150
2
25
150
150
3
25
75
150
4
25
100
100
Note: In this example axis 3 is the Z axis which only has 0.150 inches of overtravel limit in the (-)
direction. Axis 4 is a rotary axis overtravel will depend on distance from center of rotation.