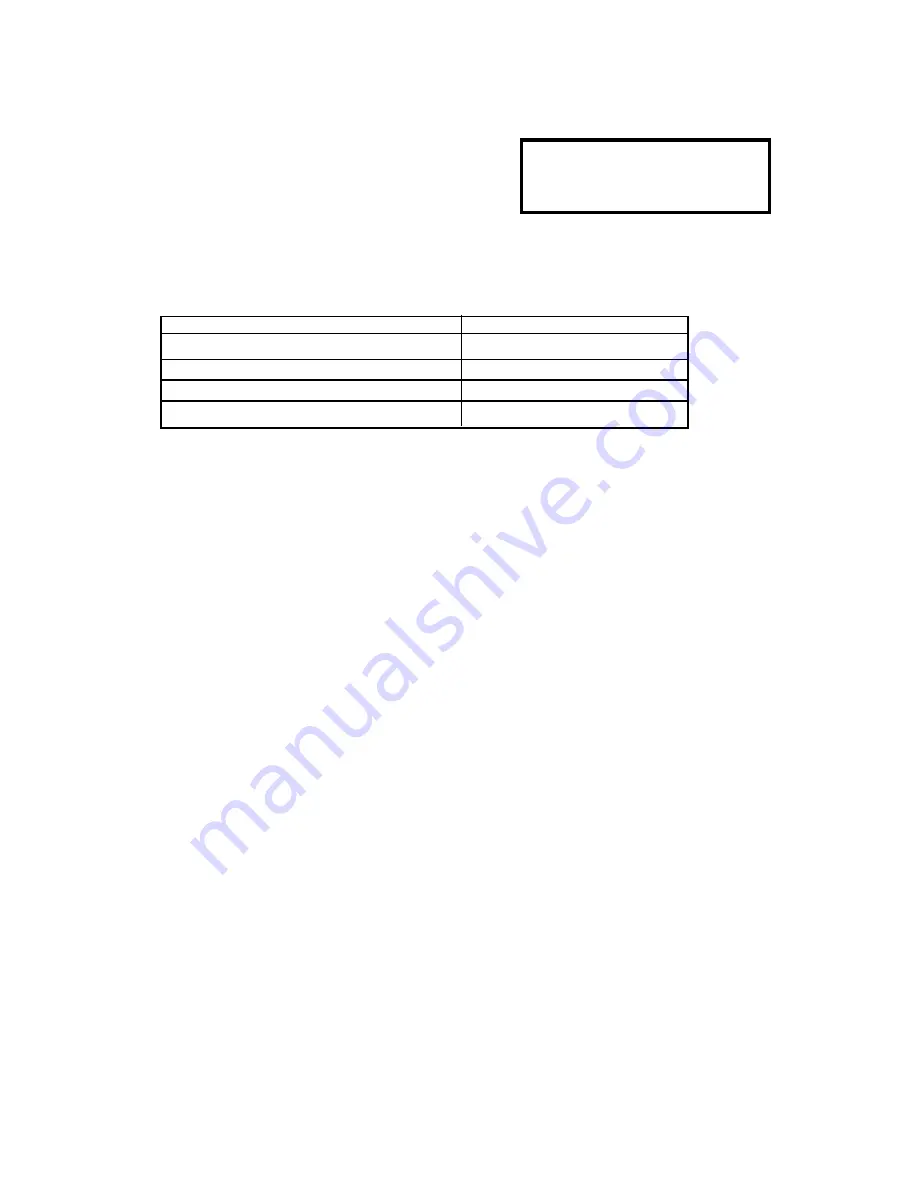
SAVE THIS MANUAL
You will need this manual for the safety instructions,
assembly and operating instructions and parts list.
Put it in a safe, dry place for future reference.
Keep
your invoice with this manual. Write the invoice
number on the inside front cover.
SPECIFICATIONS
Characteristic
Value
Measurements
40” x 14 1/2” x 23 1/2”
Weight
297 lb.
Maximum Work Piece Width
30”
Maximum Work Piece Thickness
20 Gauge
SAFETY WARNINGS & CAUTIONS
1.
KEEP WORK AREA CLEAN.
Cluttered areas invite injuries.
2.
KEEP CHILDREN AWAY.
All children should be kept away from the work area. Don’t
let them handle the tool.
3.
DO NOT OPERATE THE TOOL IF UNDER THE INFLUENCE OF ALCOHOL OR
DRUGS.
Read warning labels on prescriptions to determine if your judgment or reflexes
are impaired while taking drugs. If there is any doubt, do not attempt to operate.
4.
AVOID MOVING PARTS DURING OPERATION.
Keep fingers and hands away from all
moving parts.
5.
USE EYE PROTECTION.
Wear ANSI approved impact safety goggles. Goggles are
available from Harbor Freight Tools.
6.
DRESS SAFELY.
Protective, gloves and non-skid footwear or safety shoes are recom-
mended when working with and operating the tool. Don’t wear loose clothing or jewelry.
They can get caught in moving parts. Also, wear a protective hair covering to prevent
long hair from getting caught in the tool.
7.
DON’T OVERREACH.
Keep proper footing and balance at all times.
8.
STAY ALERT.
Watch what you are doing. Use common sense. Do not operate any
tool when you are tired.
9.
REPLACEMENT PARTS AND ACCESSORIES.
When servicing, use only identical
replacement parts. Only use accessories intended for use with this tool. Approved
accessories are available from Harbor Freight Tools.
10.
STORE IDLE EQUIPMENT.
When not in use, the tool should be stored in “closed”
position and in a dry location to reduce rust. For safety, keep out of reach of children.
READ ALL INSTRUCTIONS
BEFORE OPERATING THE
30” SHEAR BRAKE ROLL.
Page 2 -- SKU: 05907