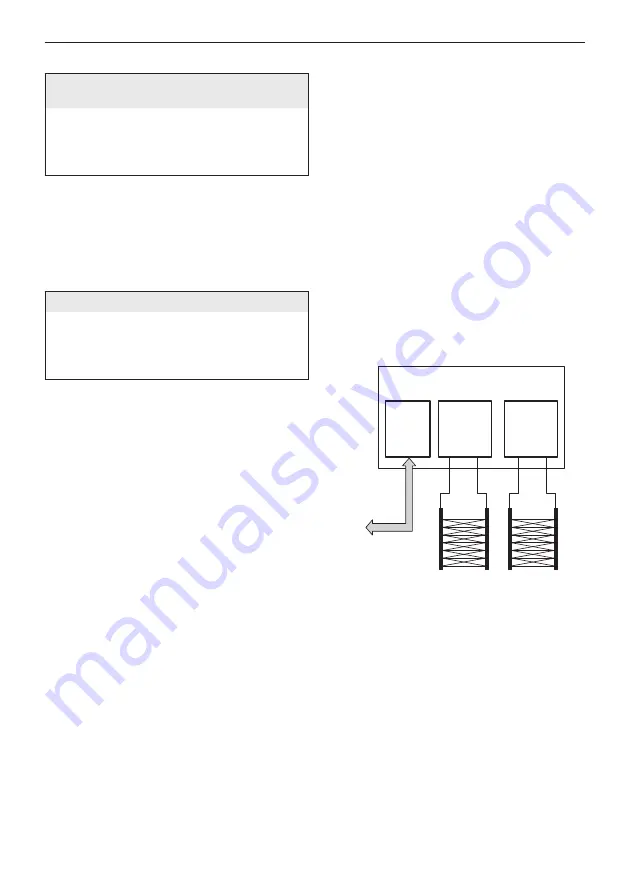
cegard/Lift LX/LY
English
4
© CEDES | V 2.10
Notice of damage risk
NOTICE
Risk of damage
Disregarding these notices can lead to damage
to the sensor, the door controller and/or other
devices.
Follow the measures highlighted by the
triangle-shaped arrows
4. Indroduction
The cegard/Lift light curtain serves to protect people
in cargo and passenger elevators without elevator cage
closure doors. The speed at which the elevator cage travels
should not exceed 0.85 m/s (max. 0.63 m/s in Switzerland
and Austria). All valid national regulations should be
observed.
IMPORTANT NOTICE
cegard/Lift is constructed exclusively for elevators,
and should not be used in areas where there is a
risk of explosion (ATEX-areas). However, a product
specifically designed for use in such ATEX-areas
(Zone 2 and 22) is also available.
The cegard/Lift carries out a self-test:
• Before each journey
• Every time a person or object interrupts the light
curtain
Every malfunction involving the opto edges, system control
rack or incorrect wiring leads to a shutdown of the elevator
system.
If an object causes an emergency stop by penetrating the
protective field during the journey, it can be signalled either
audibly or visually.
A journey interrupted by the safety equipment can only be
continued after the protective zone is reenabled by a new
drive / journey command from the interior of the elevator
cage.
Where an elevator has entrances on either side, both
are simultaneously bypassed. This occurs regardless of
whether there are one or two entrances to the elevator
cabin on a floor.
The cegard/Lift offers the following advantages:
• Also ideal for controlling automatic doors thanks to an
additional output
• Cost effective
• Simple integration into almost all existing elevator
control systems without additional travelling cables
• Simple, space-saving installation
• No setting or optical adjustment of the light curtain
necessary
• Short installation time, can be easily carried out by just
one single person
• Monitoring of up to two elevator cabin entrances
• Large range and dense protective field
• Automatic start after power-up
• 8 isolated inputs for cabin call signals,
12 … 265 VAC/DC
• Safety logics for the prevention of dangerous steps
into the elevator
• System control rack IP54
• Opto-edge IP65; IP67 optional (fully potted)
• Actuation for load control display available as
accessory
Assembly sets can be supplied as accessories which
enable integration, installation and commissioning by a
single installation fitter. The assembly kits also offer optimal
protection from daily industrial use.
5. Description of function
5.1 Structure
The cegard/Lift control unit is mounted on the elevator
car’s roof using the enclosed mounting rails.
The block circuit diagram (Figure 1) shows the setup.
Interface to the
elevator controller
Plug-in
system
controller
Control unit
Plug-in 1
Control unit
Plug-in 2
Light curtain
Entrance 1
Light curtain
Entrance 2
System control rack
Figure 1:
Interface to elevator controller
5.2 Interface to elevator controller
The following signals from the elevator controller are
required for actuation:
• At least one
internal call
and/or reset signal from
inside the elevator cabin (Chapter 5.2.1)
• Latch power supply:
Latch_In (Riegel_In)
(Chapter
5.2.2)
• Supply voltage of 230 VAC must be permanently
supplied (Chapter 7.1)
Additional signals increase the elevator’s level of
comfort:
• Elevator shaft information (e.g. slower travel speed,
zone signal) for early bypassing of the system (Chapter
5.2.3)
• Signal for testing of the safety components of
cegard/Lift (Chapter 5.2.4)