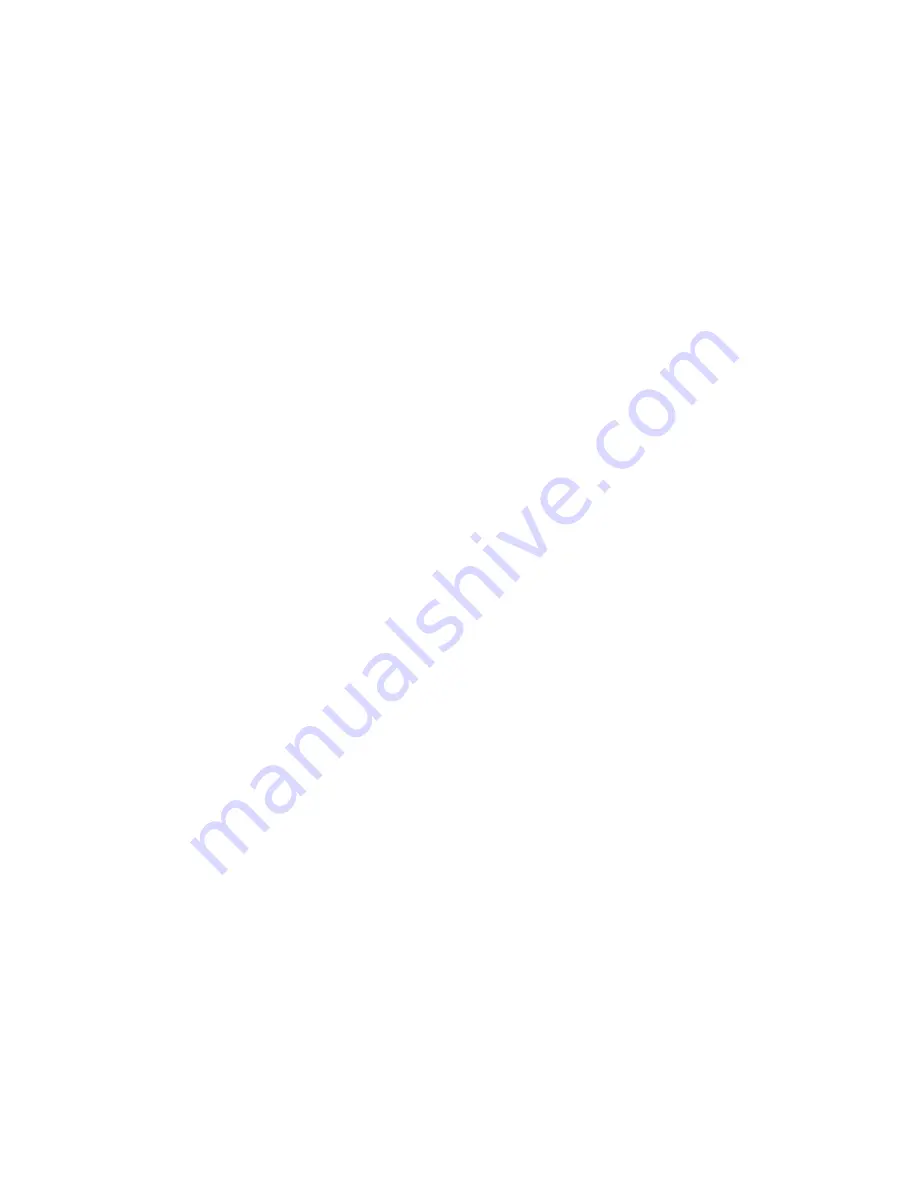
PACKING INSTALLATION
These instructions apply to the conventional woven, braided, folded,
and wrapped packings. Packings of multifilament Teflon, braided
carbon filament, compressed carbon sheet, and other special types
or materials may require special installation tech niques.
The way in which the packing is installed in the stuffing box is impor-
tant to the good service life of the packing and the shaft sleeve.
Incorrect installation will lead to excessive leakage and may cause
higher power requirements.
The use of a packing tamper (split bushing) is recommended to prop-
erly seat the packing rings. Such a tool is easily made from wood or
metal in the form of a hollow cylinder. The inside diameter must be
slightly larger than the shaft sleeve and the outside slightly smaller
than the stuffing box bore. Split the piece lengthwise to allow inser-
tion in the stuffing box. More than one length of packing tamper
may be necessary. Suit the lengths to the particular pump.
Packing rings furnished by Dean Pump Division are die molded to fit
the stuffing box. To place a ring on the shaft sleeve, open the ring at
the split at a right angle to the plane of the ring. This will best retain
the molded form and avoid distortion.Successive rings should be
installed with the joints at 90° intervals.
Foil wrapped packings must be installed with the foil laps running in
the direction of shaft sleeve rotation on the inside of the ring. Metallic
packing should be lubricated, on the wearing face only, with a dry
graphite lubricant before insertion.
Foil wrapped packing sets are furnished with soft rings of packing
which are placed between the hard metallic rings in the locations
shown in the diagrams. These rings help to furnish lubrication during
the run-in period. Being soft, they are more sensitive to compression
loads and care must be taken during the adjustment period.
Follow these steps:
1) With the packing gland slid back towards the bearing housing,
or removed if it is a two piece gland, place a ring of packing
on the shaft sleeve and enter it carefully into the stuffing box.
Insert the halves of the packing tamper and push the packing
ring to the bottom of the stuffing box. Slide the packing gland
up against the end of the packing tamper with the gland studs
indexed in the gland holes, put on the gland stud nuts and tight-
en them firmly and evenly to seat the packing ring.
2) Back off the gland, remove the packing tamper, and insert a
second ring of packing, staggering the ring joint 90° from that
in the first ring. Repeat the seating procedure above.
3) If a lantern ring is to be used, check the pump specifica tions to
determine its position in relation to the number of rings between
the bottom of the seal chamber and the lantern ring. Insert pack-
ing rings as above until the lantern ring position is reached and
then install the lantern ring.
4) If no lantern ring is to be used, or after the lantern ring is put in
place, continue to add packing rings, one at a time, staggering
joints at 90° intervals, until the stuffing box is nearly full.
5) Put the packing gland in place and pull up the gland stud nuts
firmly. Back the gland stud nuts off to finger tightness.
6) Rotate the pump shaft by hand to be sure it is not locked.
7) Final adjustment of the packing compression must be made
with the pump running.
Start and stop the pump several times
to begin the running-in period. Allow sufficient leakage to
assume good lubrication during the adjustment. Pull up the
gland stud nuts 1/8 turn at a time. Allow a running in period
between adjustments. Continue adjustment until the desired
leakage control is reached. The minimum leakage rate depends
on a number of things: liquid pumped, packing used, tempera-
ture, stuffing box pressure, and the condition of the pump. In
any case, some leakage is necessary to both lubricate and cool
the packing. Minimum rates may vary from a few drops per
minute to as much as 1/2 pint per minute.
8) As the packing wears in service, the gland should be readjust-
ed to maintain the minimum leakage.
9) After the gland has been taken up to full travel, an additional
ring of packing may be placed in the stuffing box. When the
gland has again been taken up to full travel the stuffing box
should be repacked completely.
USUAL CAUSES OF PACKING FAILURE AND EXCESSIVE STUFF-
ING BOX LEAKAGE
1) Packing has not been installed properly.
2) Packing used is not suitable for the temperature and pressure
involved or may be subject to attack by liquid handled.
3) Inner rings are not thoroughly seated in the stuffing box so
that outer rings are carrying all the load.
4) Dirt and foreign particles in stuffing box are causing rapid
scoring of shaft sleeve.
5) Stuffing box cooling water not turned on.
6) Packing gland pulled up too tight.
When ordering additional packing sets, always refer to pack-
ing set number and to pump serial number.
INSTALLATION OF STANDARD MECHANICAL SEALS
22
Clean, careful, and correct installation of the mechanical seal is
essential to successful mechanical seal operation. Cleanliness and
accuracy of setting cannot be overemphasized.
For instructions on the pump disassembly and assembly, see above.
A correct mechanical seal drawing is furnished with each pump and
the mechanical seal setting dimension is given on this drawing.
Use the setting for the specific pump type in which the installation is
being made.
The pump is first assembled according to the applicable assem bly
instructions through the step of casing back cover installation.
The mechanical seal rotary unit must be properly located in relation
to the face of the pump seal chamber in order to establish the proper
seal spring tension and resultant proper force on the seal faces. An
error in setting of more than several thousandths may well cause seal
failure by excessive or insuffi cient seal face pressure.
INSTALLATION OF SINGLE INSIDE SEALS
To make the seal installation, with the pump partially assembled as
noted above, scribe a mark on the shaft sleeve (10) exactly in line
with the face of the pump seal chamber (Note 1). The impeller (3),
and casing back cover (22) are now removed from the pump. If the
mark causes roughness on the shaft sleeve remove the burr carefully