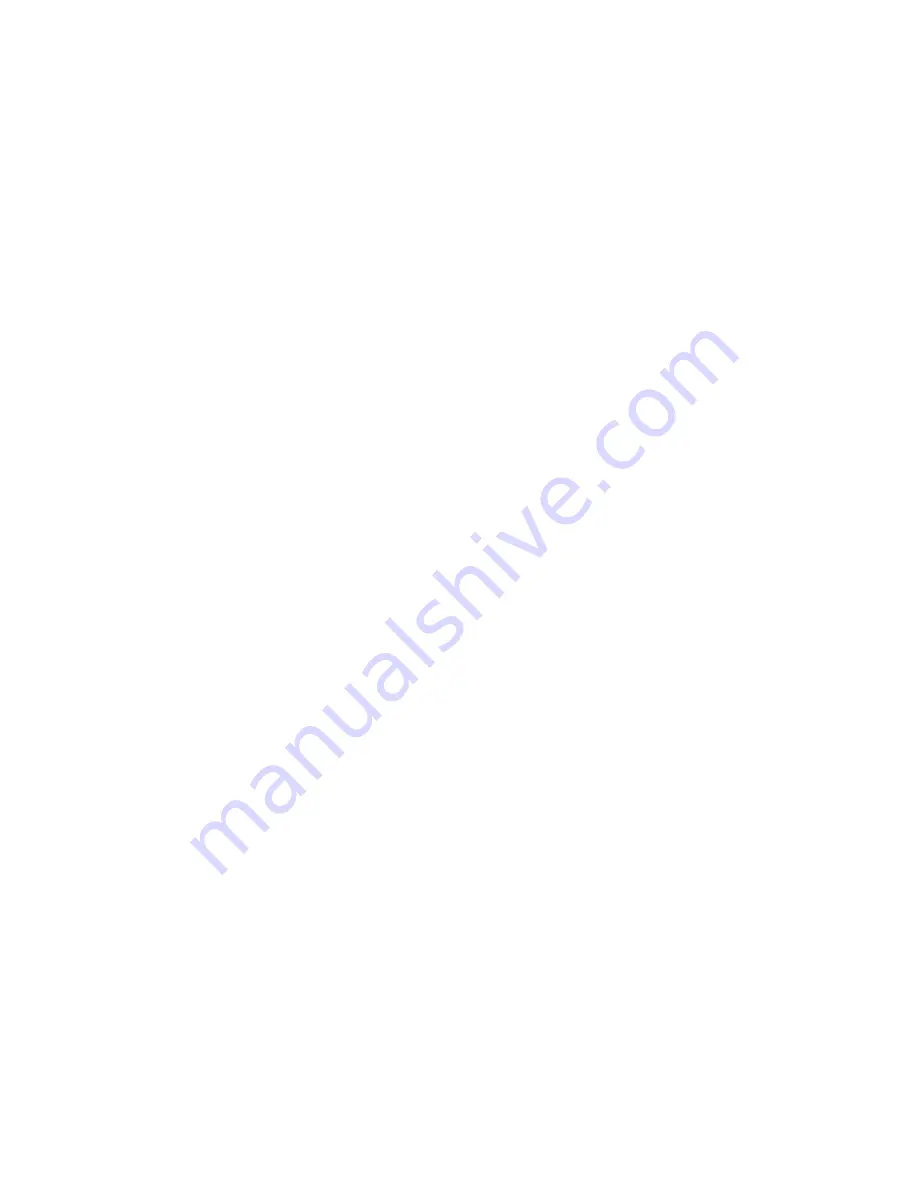
allowing liquid to flow from the system into the pump. Personal
injury, death and/or equipment damage may occur if great caution
is not exercised.
n) Because of the above possibility, when you loosen the gasketed
joint at the back of the casing (5), loosen the casing nuts (5C)
only one full turn, and then use the jack screws in the flange of
the cradle spacer (7) to break the gasket seal. If fluid and/or
pressure remains in the pump it will spray out now. Use
extreme caution, wearing protective gear, to avoid injury. Do
not proceed with disassembly until leakage ceases completely.
If leakage does not cease, the isolation valves may not be seal-
ing. Note that if the pump was purchased without a drain, the
pump will contain fluid which will flow out at the time the nuts
are loosened and the gasket seal is broken.
WARNING:
When you open the pump, the fluid will be exposed to the atmos-
phere and personnel in the area. For the safety of all involved, the
risk of exposure can be reduced by flushing the cavity that was just
drained with a compatible, non-toxic, non-hazardous, stable liquid,
before disassembling the pump.
o) Remove the casing nuts (5C) and using a mechanical lifting
apparatus to support the weight, pull the rotating unit from the
casing (5).
p) Flush the wetted parts, now exposed, with a compatible, non-
toxic, non-hazardous, stable liquid.
q) Remove the gasket from the face of the casing (5) or the casing
back cover (22) dependent on which one the gasket may have
adhered to. The type of gasket and material of construction will
vary with service requirements. Attack by prying and then, if
necessary, layering off the old gasket with a sharp scraper,
attempting to remove it in the largest possible pieces. Wear
heavy leather, long sleeve work gloves when using the scraper.
Be careful to not scar the gasket contact surfaces of the casing
or the casing back cover. Wet the gasket before and during the
scraping operation to reduce the possibility of fibers becoming
airborne. Wear a respirator during this operation and until all
debris has been disposed of in a plastic bag. Remove all of the
gasket material down to clean metal surfaces on both parts that
contacted the gasket. Place all of the gasket residue in a plastic
bag, seal the bag and dispose.
r) The rotating assembly of the pump can now be moved to a
more convenient location for further disassembly. Use mechani-
cal lifting equipment to move assemblies and components.
DISASSEMBLY PROCEDURE
To further dismantle the pump, perform the following steps in the
sequence shown:
WARNING:
Use only high quality tools.
Flush parts as disassembled to remove hazardous residue from the
pumpage and/or sub-system fluids.
Wear protective equipment as advised at the beginning of this
section.
Use mechanical lifting equipment to lift assemblies and components.
Do not apply heat to parts to assist in disassembly. Explosion could
occur causing personal injury, death, and/or damage to equipment.
Do not attempt to drill, saw or otherwise cut parts to remove them.
Explosion and/or fuming could occur causing personal injury, death,
and/or equipment damage.
Do not hammer on any parts. Personal injury and/or damage to
equipment may occur.
a) Remove gland stud nuts (15) and slide gland (13) away from
seal chamber.
b) Remove packing from stuffing box if pump is packed. Use pack-
ing extractor.
c) Turn down the lip of the lockwasher (12B) which is turned up
against one flat of the impeller bolt (12). Remove impeller bolt
(12) (right hand thread). Remove impeller bolt lockwasher
(12B) and impeller retaining washer (12A). Discard the lock-
washer (12B). The impeller may now be removed from the
shaft (29). Remove impeller key (4) from the shaft.
d) Remove the two capscrews securing the casing back cover (22)
to the cradle spacer (7) and lift out the casing back cover. Do
not remove the gland studs (14) from the casing back cover
(22). If the gland studs (14) are damaged, or it is deemed nec-
essary for any other reason to remove the gland studs (14),
contact Dean Pump.
e) If the pump is equipped with a mechanical seal, loosen the set
screws that retain the seal and remove the mechanical seal
rotary (95B). Remove the mechanical seal stationary (95A) and
gland(13). Remove the mechanical seal stationary (95A) from
the gland (13).
f) Remove the four capscrews securing the cradle spacer (7) to
the bearing housing (26) and remove the cradle spacer.
g) Remove the shaft sleeve (10) and shaft sleeve key (10K) from
the shaft.
h) Remove pump half of coupling from shaft (29).
i) Remove the bearing housing oil cooler (109) before attempting
to remove the pump shaft (29). Remove the 1/2” tube x 1/2”
male pipe thread fitting from one end of the oiler cooler (109).
Remove the tubing nut and tubing ferrule from the 1/2” tube x
1” male pipe thread fitting that is in the bearing housing (26)
on the same side that you removed the first fitting. Unscrew the
1/2” tube x 1” male pipe thread fitting that is on the opposite
side of the bearing housing (26) from the bearing housing and
pull the oil cooler (109) out through the 1” NPT opening.
j) Remove the bearing end cover (28) and end cover gasket
(77B) from the bearing housing (26). Remove the gasket (77B)
from the end cover (28).
k) Push the pump shaft (29) towards the rear of bearing housing
(26) until the thrust bearings (25A) are out of the back end of
the bearing housing. Lift the shaft and reach in, with snap-ring
pliers, to remove the snap ring (75B) from the bearing housing
(26). Remove pump shaft and bearing assembly from the rear
of the bearing housing.
l) Bend the tab of the lock nut washer (31A) out of the slot in the
bearing lock nut (31). Remove bearing lock nut (31) and lock
nut washer (31A) from the pump shaft (29). Use a hydraulic
press to remove the bearings (25 and 25A) from the shaft.
Ham mering bearings in any way, may result in serious dam-
age to the pump shaft.
Remove snap ring (75B) from the pump
shaft.
m) Press seal ring (27), labyrinth seal (76) assembly from bearing
housing (26).
n) Press the front labyrinth seal (76) from seal ring (27).
o) Press rear labyrinth seal (76A) from bearing end cover (28).
p) If necessary, remove the casing ring (6A) by prying it out of the
casing (5). If the ring is tack-welded into the casing, grind the
13