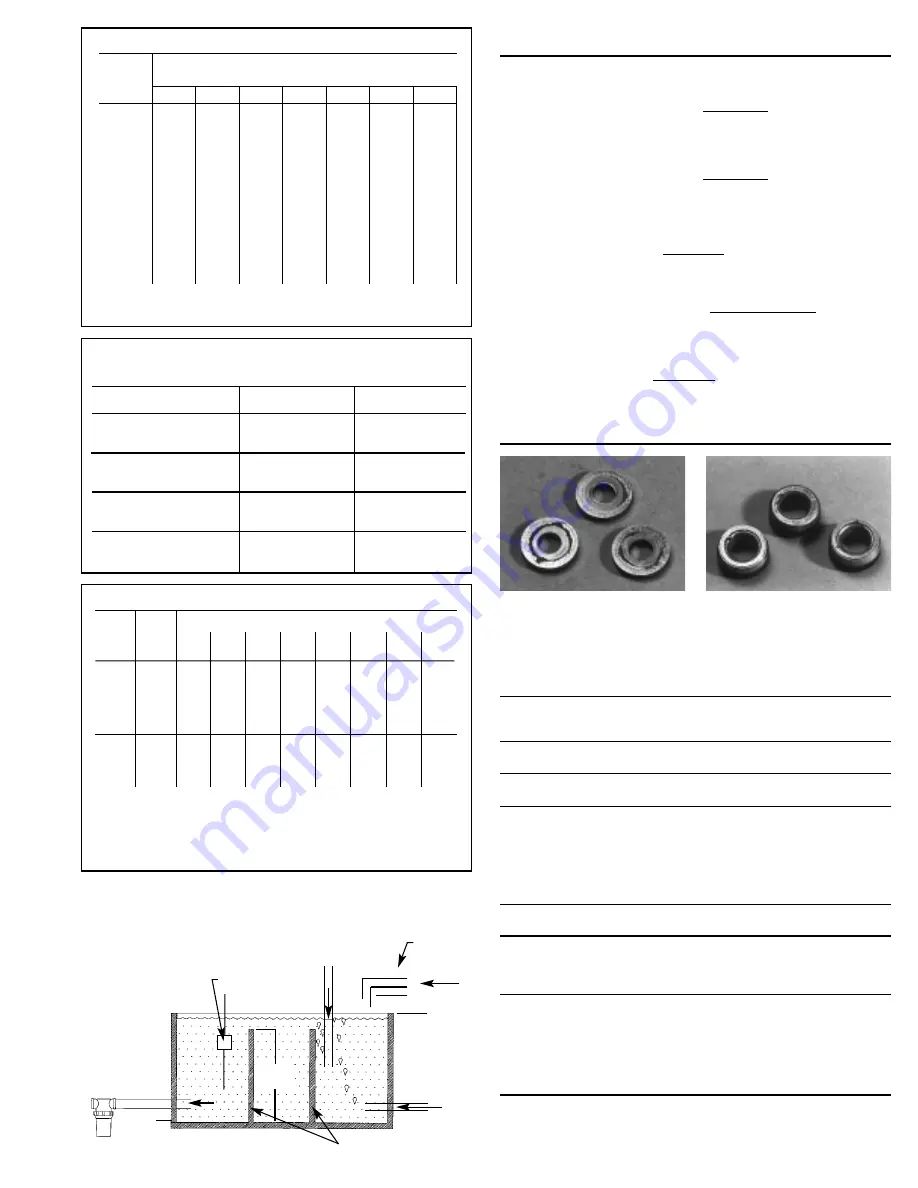
TYPICAL RESERVOIR TANK
RECOMMENDED 6 TO 10 TIMES SYSTEM CAPACITY
1/4
5/16
3/8
1/2
5/8
3/4
1"
0.5
16
5
2
1
54
20
7
2
2
180
60
25
6
2
3
380
120
50
13
4
2
4
220
90
24
7
3
5
320
130
34
10
4
6
220
52
16
7
1
8
300
80
25
10
2
10
450
120
38
14
3
15
900
250
80
30
7
20
1600
400
121
50
12
25
650
200
76
19
30
250
96
24
40
410
162
42
50
600
235
62
60
370
93
*At a fixed flow rate with a given size hose, the pressure drop across a given hose length
will be directly proportional. A 50 ft. hose will exhibit one-half the pressure drop of a 100
ft. hose. Above values shown are valid at all pressure levels.
PRESSURE DROP IN PSI PER 100 FT OF HOSE
WITH TYPICAL WATER FLOW RATES
Hose Inside Diameters, Inches
Water*
Flow
Gal/Min
HOSE FRICTION LOSS
Water
GPM
1
2
3
5
8
10
15
25
40
60
80
100
Steel Pipe—Nominal Dia.
1/4 3/8 1/2 3/4
1 1
1
/
4
1
1
/
2
8.5 1.9
30 7.0 2.1
60 14 4.5 1.1
150 36
12 2.8
330 86
28 6.7 1.9
520 130
43 10 3.0
270
90 21 6.2 1.6
670 240 56
16 4.2 2.0
66
17 8.0
37
17
52
29
210 107
48
Brass Pipe—Nominal Dia.
1/4 3/8 1/2 3/4
1
1
1
/
4
1
1
/
2
6.0 1.6
20 5.6 1.8
40 11 3.6
100 28 9.0 2.2
220 62
21 5.2 1.6
320 90
30 7.8 2.4
190
62 16 5.0 1.5
470 150 40
12 3.8 1.7
39
11 5.0
23
11
40
19
61
28
Copper Tubing O.D. Type L
1/4 3/8 1/2 5/8 3/4 7/8
120 13 2.9 1.0
400 45
10 3.4 1.3
94
20 6.7 2.6
230
50 17 6.1 3.0
500 120 40
15 6.5
180 56
22
10
120
44
20
330 110
50
550 200
88
WATER LINE PRESSURE LOSS
PRESSURE DROP IN PSI PER 100 FEET
1/2
0.622
0.41
18.5
9.3
0.78
1.67
3.71
0.93
3.33
3/4
0.824
0.54
24.5
12.3
1.03
2.21
4.90
1.23
4.41
1
1.049
0.69
31.2
15.6
1.31
2.81
6.25
1.56
5.62
1
1
/
4
1.380
0.90
41.0
20.5
1.73
3.70
8.22
2.06
7.40
1
1
/
2
1.610
1.05
48.0
24.0
2.15
4.31
9.59
2.40
8.63
2
2.067
1.35
61.5
30.8
2.59
5.55
12.30
3.08
11.60
2
1
/
2
2.469
1.62
73.5
36.8
3.09
6.61
14.70
3.68
13.20
3
3.068
2.01
91.5
45.8
3.84
8.23
18.20
4.57
16.40
4
4.026
2.64
120.0
60.0
5.03
10.80
23.90
6.00
21.60
Nominal
Pipe
Size
Inches
Inside
Diameter
Inches
RESISTANCE OF VALVES AND FITTINGS
Gate
Valve
Globe
Valve
Angle
Valve
45˚
Elbow
90˚
Elbow
180˚
Close
Ret
Tee
Thru
Run
Arriving at a total line pressure loss, consideration should then be given to
pressure loss created by valves, fittings and elevation of lines.
If a sufficient number of valves and fittings are incorporated in the system to
materially affect the total line loss, add to the total line length, the equivalent
length of line of each valve or fitting.
Tee
Thru
Branch
Equivalent Length of Standard Pipe in Feet
Bypass Line
(from regulator or unloader)
Level Sensing
Device
Bypass Line
(from regulator or
unloader)
MIN. 4"
1.5 x D (Min.)
Minimum Two Baffles
Sealed at Bottom
Minimum
Liquid
Level
FILTER
MIN. 4"
Flexible Hose
to Pump
Supply Line
(Dia of pipe)
T
X
D
→
→
→
→
→
→
→
→
→
Q. How can I find the RPM needed to get specific GPM
(Gallons Per Minute) I want?
Rated RPM
A. Desired RPM = Desired GPM x
Rated GPM
Q. I have to run my pump at a certain RPM. How do I figure
the GPM I’ll get?
Rated GPM
A. Desired GPM = Desired RPM x
Rated RPM
Q. Is there a simple way to find the approximate horsepower
I’ll need to run the pump?
A. Electric Brake
GPM x PSI
(Standard 85%
Horsepower Required
=
1460
Mech. Efficiency)
Q. What size motor pulley should I use?
Pump RPM
A. Pump Pulley (Outer Diameter) x
Motor/Engine RPM
Q. How do I calculate the torque for my hydraulic drive
system?
GPM x PSI
A. Torque (ft. lbs.) = 3.6
RPM
( )
One or several of the conditions shown in the chart below may
contribute to cavitation in a system resulting in premature wear,
system downtime and unnecessary operating costs.
CONDITION
SOLUTION
Inadequate inlet
●
Increase line size to the inlet port or one size
line size
larger
Water hammering
●
Install C.A.T. Tube
liquid acceleration/
●
Move pump closer to liquid supply
deacceleration
Rigid Inlet Plumbing
●
Use flexible wire reinforced hose to absorb
pulsation and pressure spikes
Excessive Elbows in
●
Keep elbows to a minimum and less than 90°
Inlet Plumbing
Excessive Liquid
●
Use Thermo Valve in bypass line
Temperature
●
Do not exceed pump temperature specifications
●
Substitute closed loop with baffled holding tank
●
Adequately size tank for frequent or high
volume bypass
●
Pressure feed high temperature liquids
●
Properly ventilate cabinets and rooms
Air Leaks in Plumbing
●
Check all connections
●
Use PTFE thread tape or pipe thread sealant
Agitation in Supply
●
Size tank according to pump output —
Tank
Minimum 6-10 times system GPM
●
Baffle tank to purge air from liquid and
separate inlet from discharge
High Viscosity Liquids
●
Verify viscosity against pump specifications
before operation
●
Elevate liquid temperature enough to reduce
viscosity
●
Lower RPM of pump
●
Pressure feed pump
●
Increase inlet line size
Clogged Filters
●
Perform regular maintenance or use clean
filters to monitor build up
●
Use adequate mesh size for liquid and pump
specifications
Handy Formulas to Help You
(Consult
Engine Mfr.)
Avoid Cavitation Damage