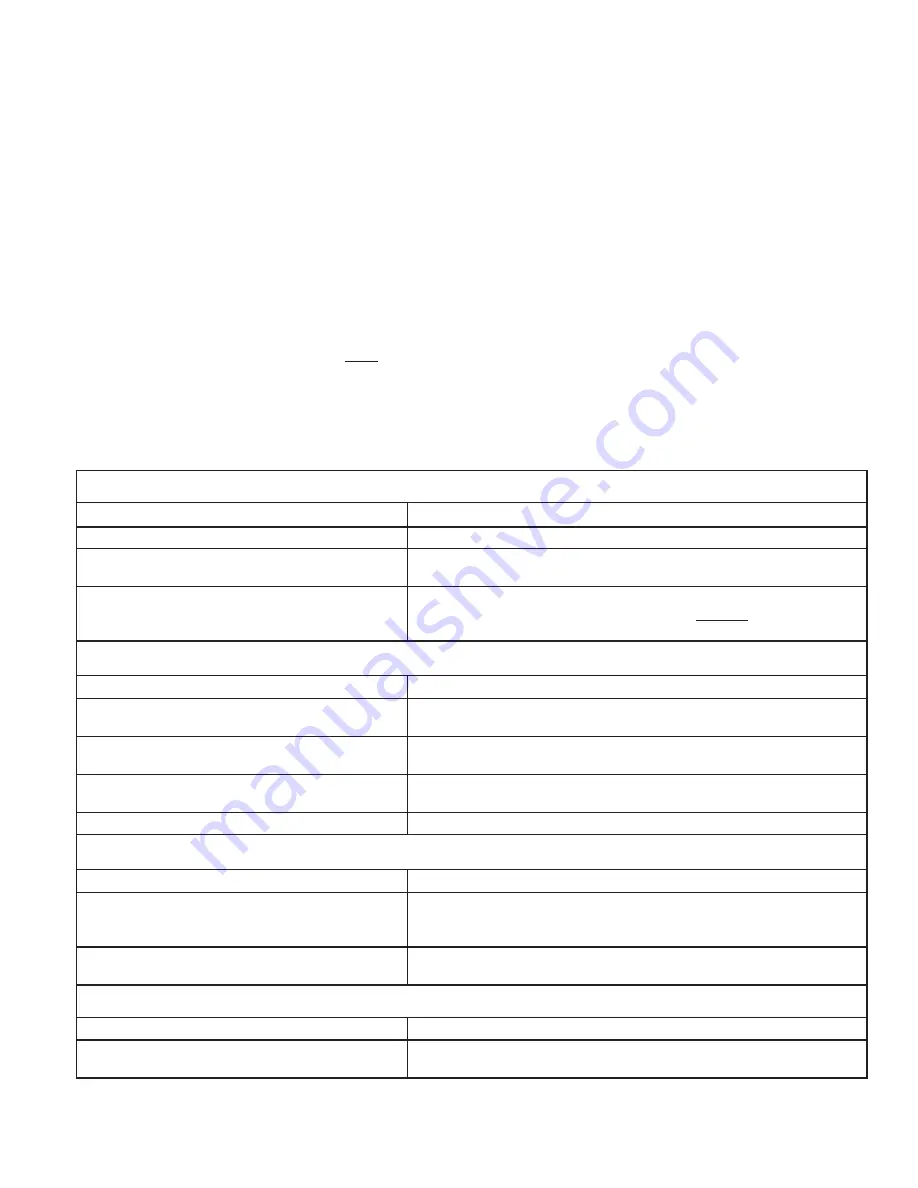
IOM-PGR-2
9
SECTION VIII
VIII. TROUBLE SHOOTING GUIDE
When trouble shooting this regulator there are many possibilities as to what may be causing problems. Many times, the regu-
lator itself is not defective, but one or more of the accessories may be. Sometimes the pro cess may be causing difficulties.
The key to efficient trouble shooting is information and communication. The customer should try to be as precise as possible
in their explanation of the problem, as well as their understanding of the application and operating con di tions.
It is imperative the following information be provided by the customer:
• Type of Service (with fluid properties)
• Range of outlet pressure
• Range of flow rate
• Range of temperature
• Range of inlet pressure
• Range of ambient temperature
Pressure readings should be taken at every location where pressure plays a role - i.e., regulator inlet (as close as possible to
inlet port), regulator outlet (as close as possible to outlet port), etc.
Following are some of the more common complaints along with possible causes and remedies.
1. Erratic regulation, instability or hunting.
Possible Causes
Remedies
A.
Sticking of internal parts.
A.
Remove internals, clean, and if necessary, replace.
B. Oversized
regulator.
B.
Check actual flow conditions; resize regulator for min i mum and maxi-
mum flow; if necessary, replace with smaller regulator.
C. Metering Valve may not be adjusted correctly.
C. Rotate knob on metering valve in 1/4 turn increments to be more or
less sensitive to changes in P2 pressure.
DO NOT
fully close the
metering valve.
2. Downstream pressure will not reach desired setting.
Possible Causes
Remedies
A.
Supply pressure is down (confirm on pressure
gauge.)
A.
Increase supply pressure.
B.
Undersized regulator.
B.
Check actual flow conditions; resize regulator for min i mum and maxi-
mum flow; if necessary, replace with larger regulator.
C.
Pressure loading system pressure restricted.
C1. Clean filter.
C2. Clean pilot valve.
D.
Faulty loading pressure control device.
D.
Replace/repair loading pressure control device.
3. Diaphragm continually breaks.
Possible Causes
Remedies
A.
Stem seals (13) which protect fluorocarbon
elastomer in diaphragm assembly may have
deteriorated.
A.
Replace with new stem seals (13).
B.
Diaphragm nut (11) may not be torqued to
correct value.
B.
Confirm torque value in accordance with Section VII, F-13.
4. Diaphragm continually breaks (all regulators).
Possible Causes
Remedies
A.
Differential pressure across diaphragm may
have exceeded limits.
A1. Be aware of limits as well as where the various pressures are acting.
Install pressure safety equipment as necessary.