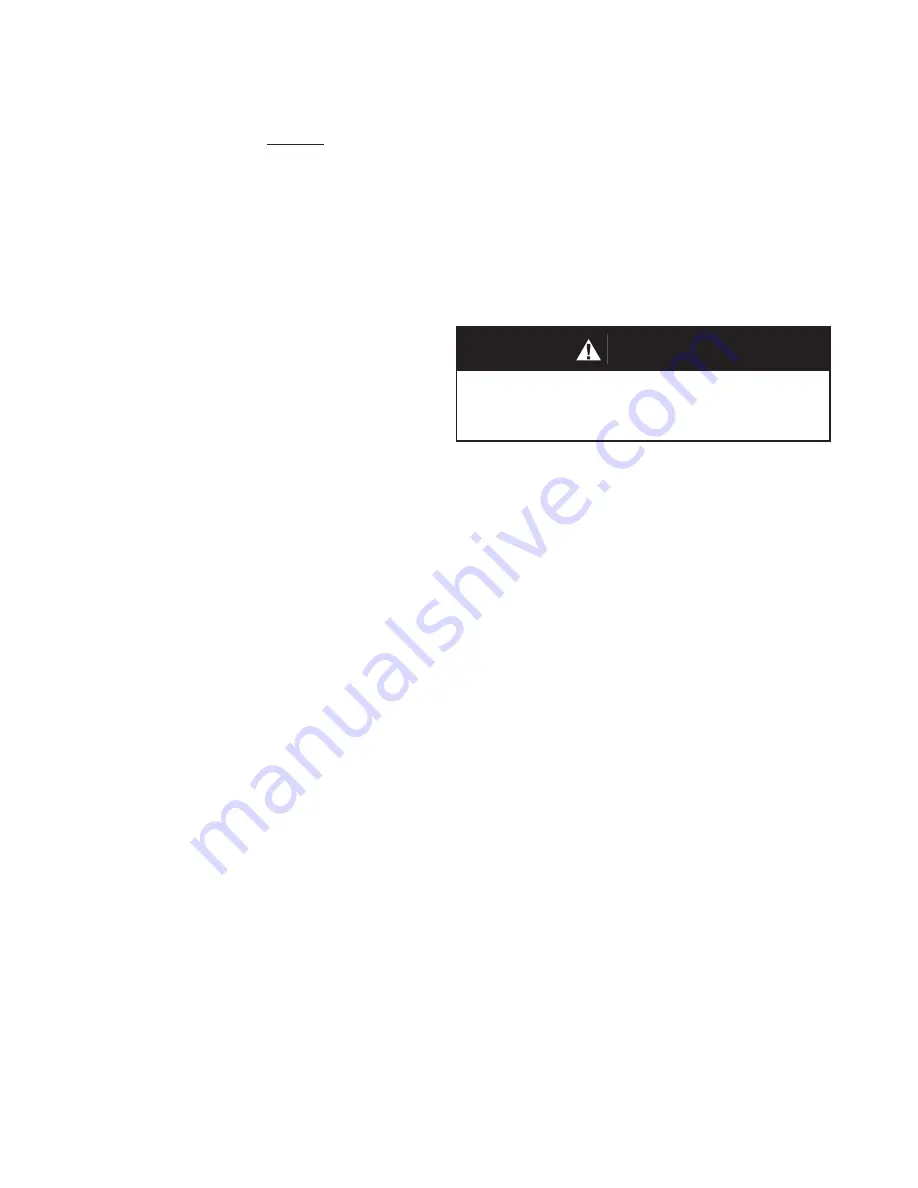
IOM-PGR-2
4
15. Spray liquid leak detector around body cap (5)
and body (1) for test for leakage. Test pres sure
should be a min i mum of 100 psig (6.9 Barg) at
the inlet. Outlet should be tested to upper value
of range spring (14) with a 100 psig (6.9 Barg)
minimum.
NOTE:
When piston (15) assemblies are
used with comp seats, Cashco, Inc. does not
rec om mend attempting to remove the comp
seat. If composition seat is dam aged, re place
entire pis ton assembly.
G. Pilot Valve Disassembly:
outlet pressure is main tained during this leak
test of at least mid-range spring level; i.e. 10-40
psig (.69 - 2.8 Barg) range spring, 25 psig (1.7
Barg) test pressure mini mum.
C. Trim
Replacement:
1. Install body (1) in a vise with the body cap (5)
on top and the body (1) flange down wards.
2. Loosen and remove body cap (5).
3. Remove piston spring (17), piston (15), and
cyl in der (16). Do not remove pusher plate (11).
Inspect parts for excessive wear, espe cially
at seat sur fac es. Re place if worn, nicked or
de pressed.
4. Remove the cylinder gasket (18) and clean
con tact ing surface of body (1).
5. Clean flat mating surfaces of body (1) to body
cap (5) shoulder.
6. Clean debris from within body (1) cavity. Clean
parts to be reused.
NOTE:
On regulators originally supplied as
“oxygen clean”, Option 55, maintenance must
include a level of clean li ness equal to Cashco
cleaning stan dard #S-1134.
7. Reinstall a new cyl in der gasket (18). Press
firmly and evenly into place using the cyl in der
(16). Do not use a “homemade” cyl in der gas ket.
Pipe seal ant may be lightly coated to cylinder
gasket (18) surfaces prior to in stal la tion, ex cept
when utilized as Item 6 above.
9. Reinstall
the
cyl
in der (16) con cen tri cally with in
the body cap (5) opening.
10. Slide the piston (15) slowly into place, as sur ing
that the piston (15) post slides into the female
groove of the pusher plate (11).
12. Place piston spring (17) into piston (15) cav i ty.
13. Use pipe thread sealant applied to the body
cap (5) threads. Thread body cap (5) into body
(1). Impact until body cap (5) is metal to metal
against body (1) at the body cap (5) shoulder.
14. Bench test unit for suitable operation.
NOTE:
Regulators are not tight shutoff devices. Even if
pressure builds up be yond set point, a regulator
may or may not de velop bubble tight shutoff. In
general, tighter shutoff can be expected with
com po si tion seat.
WARNING
SYSTEM UNDER PRESSURE. Prior to per form ing any
maintenance, isolate the reg u la tor from the system and
relieve all pressure. Failure to do so could result in
personal injury.
1. Shut down system in accordance Section VI.
2. Disconnect the external sensing line, from
the pilot valve sensing port.
3. Loosen all fittings and remove tubing that con-
nect the inlet filter to the stabilizer, the cover
dome to the metering valve and the outlet of
the metering valve to the outlet of the body.
4. Loosen and remove the two nuts (24) that
secure the mounting bracket (3) and pilot to
the cover dome (2).
5. Remove pilot assembly from main valve.
6. Place the pilot valve body (30.1) in a vise with
the spring chamber (30.2) upwards.
7. Loosen adjusting screw nut (30.18) one revo-
lution CCW. Relax range spring (30.4) forces
by rotating adjusting screw (30.17) CCW until
removed from spring chamber (30.2).
8. Loosen the diaphragm flange bolts (30.19)
and nuts (30.21) uniformly and remove bolt-
ing.
9. Place match marks on body (30.1) spring
chamber (30.2) flanges. Remove spring
chamber.
10. Remove spring button (30.5), range spring
(30.4) and pressure plate (30.6).
11. Remove diaphragm (30.13).Examine dia-