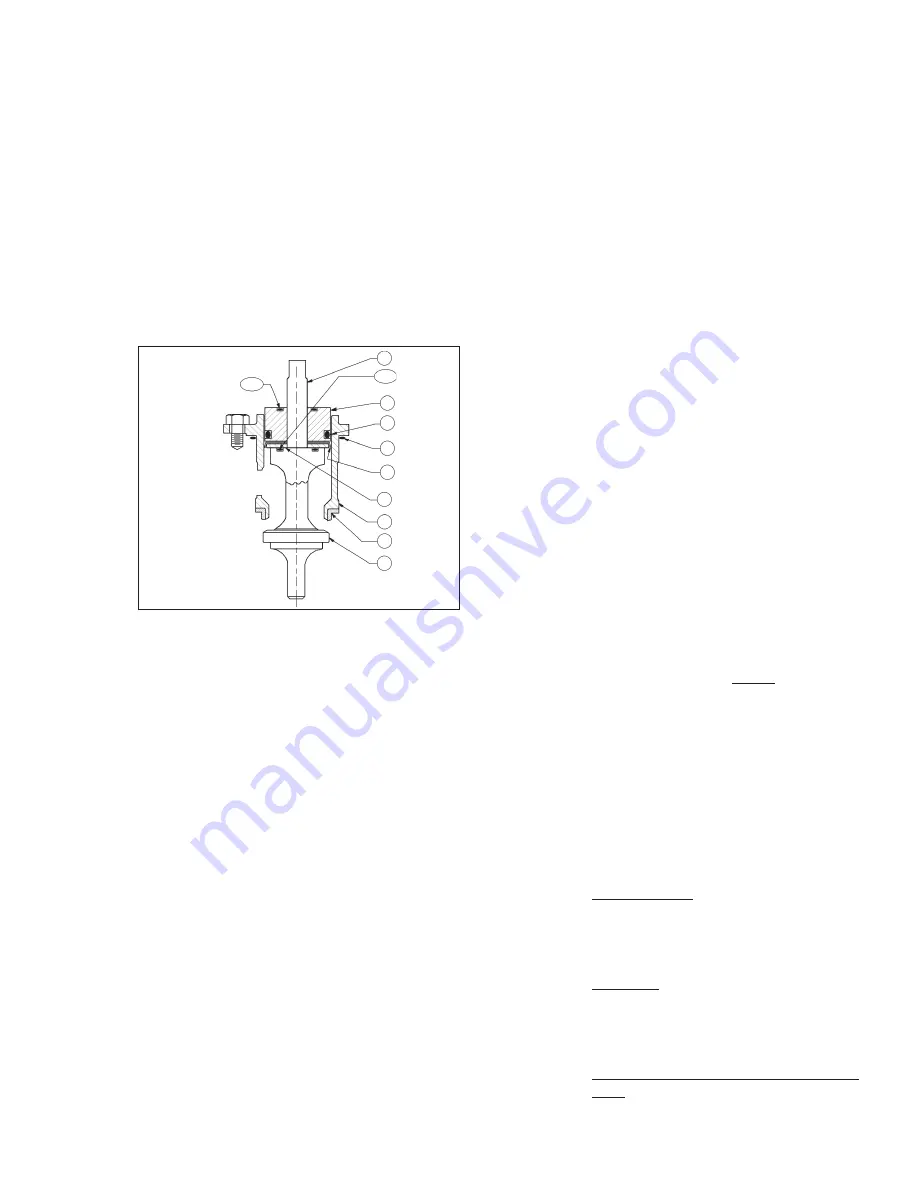
IOM-ALR-1
5
10. Re
move lower diaphragm plate (10).
11. Evenly loosen the three cage cap screws (18)
in single revolution increments.
NOTE:
Regu-
lator may con tain a lower piston spring (22);
the ITA should rise as the cage cap screws
(18) are evenly backed out. A down wards
holding force should be ap plied to the top of
the guide bearing (13) to pre vent the ITA from
pop ping up as the last threads of the cage cap
screws (18) are backed out.
12. Remove the ITA by pulling up on the valve
plug (20). Set ITA aside.
Figure 3:
Assembled ITA
13. Remove the lower piston spring (22), as ap-
pli ca ble, from within the body (23).
14. Remove o-ring cage seal (15).
15. If supplied, remove internal sensing drilled
plug (33) using 5/32" (4 mm) Allen wrench.
16. Remove body (23) from vise. Clean all re us able
metal parts according to owner's pro ce dures.
C. Disassembly of the ITA: (
See Figure 3)
1. Pull the valve plug (20) down wards and out
of the guide bear ing (13) and cage (19).
2. Remove the guide bearing (13) from the upper
end of the cage (19).
3. Remove o-ring middle stem seal (14.2) from
guide bearing (13).
4. Examine
the
com
po nents (27.1, 27.2, 27.3,
27.4) of the dy nam ic side seal (27) mechanism
to de ter mine if sig nif i cant leakage was oc cur-
20
21
19
17
16
15
27
13
14.3
20
14.2
ring. If the dy nam ic side seal (27) shows signs
of sig nif i cant leakage, de ter mine if op er at ing
con di tions are ex ceed ing pres sure, pres sure
drop, or tem per a ture limits.
Remove dynamic side seal (27) com po nents.
Special care should be taken when using
“tools” to remove the components to ensure
that no scratches are imparted to any portion
of the guide bearing (13) groove.
5. Remove wiper seal (16), if supplied, from within
cage (19) I.D.
6. Remove wiper washer (17.1) from within the
cage (19) I.D.
7. Remove o-ring lower stem seal (14.3) from
plug (20).
8. Remove seat ring (21); examine for signs of
leakage. If seat ring shows signs of significant
leakage, determine if op er at ing con di tions of
pressure, pressure drop, or temperature are
ex ceed ing limits.
9. Clean all reusable metal parts according to
owner's procedures.
D. Inspection of Parts:
1. After inspection remove from the work area
and dis card the old “soft goods” parts (i.e. o-
rings, di a phragms, seals, gaskets, etc.) after
in spec tion. These parts MUST be re placed
with fac to ry supplied new parts.
2. Inspect metal parts that will be reused. The
parts should be free of surface con tam i nants,
burrs, oxides, and scale. Rework and clean
parts as necessary. Surface con di tions that
affect the regulator performance are stated
below; replace parts that can not be re worked
or cleaned.
3. QC
Requirements:
a. Valve plug (20);
1. 16 rms finish on its seating surface
for tight shutoff.
2. No major defects on bottom guide
spin dle.
b. Cage
(19);
1. 16 rms finish on cylinder bore. No
“ledges” formed due to wear from
moving dynamic side seal (27) or
wiper seal (16).
c. Lower guide bushing (24) (non-re place-
able):