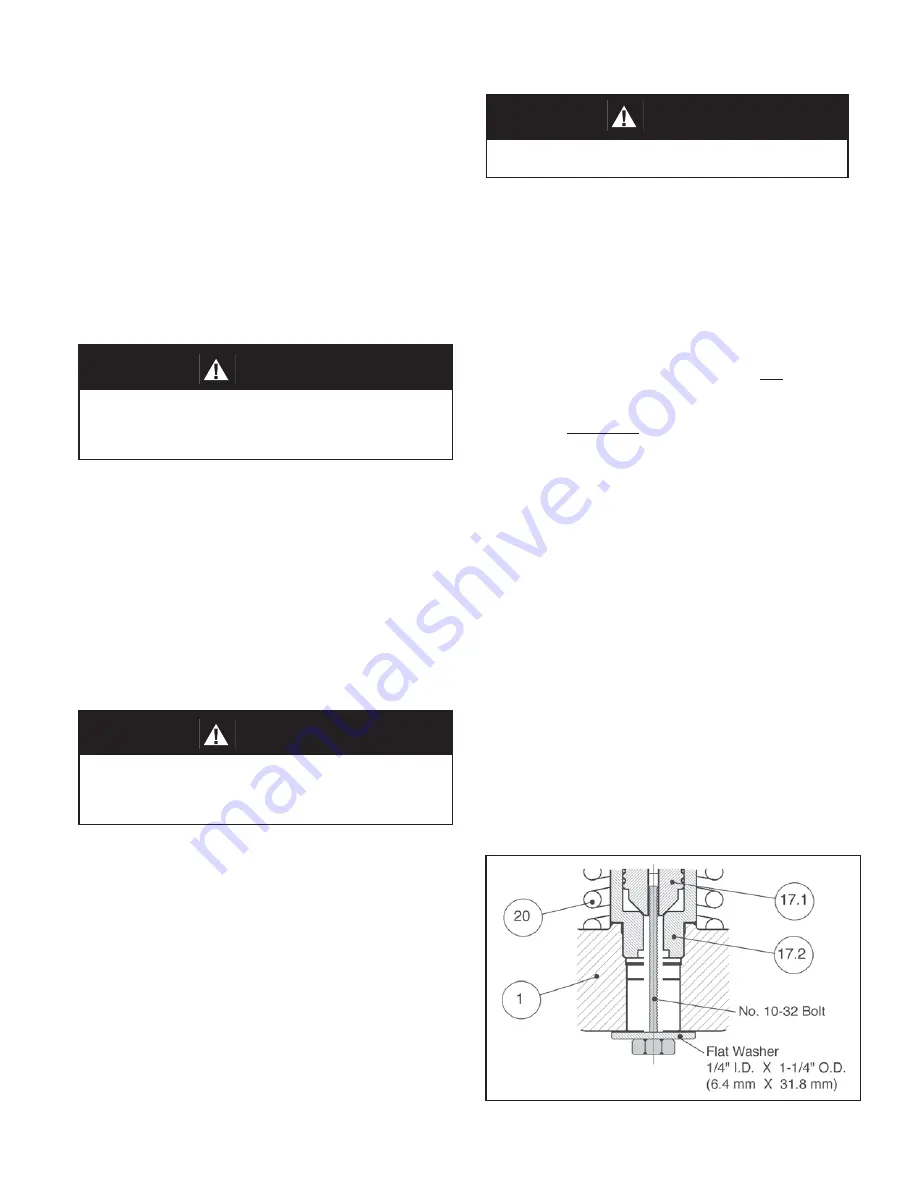
IOM-6987
3
A. General:
1. Maintenance procedures hereinafter are
based upon removal of the regulator unit from
the pipe line where installed.
2. Owner should refer to owner's procedures for
re mov al, handling, cleaning and disposal of
nonreusable parts, i.e. gaskets, etc.
3. Refer to Figure 2 for basic regulator parts.
B. Diaphragm Replacement:
1. For regulators with NPT end connections
only, fabricate the special tool de scribed
in Figure 1. Rotate the No. 10-32 bolt CW
to col lapse the piston spring (20). This will
hold the renewal unit (17) in place during
dis as sem bly. For all other end con nec tion
options, proceed with Step 2.
2. Securely install the body (1) in a vise with the
spring chamber (2) directed upwards.
3. Loosen the adjusting screw lock nut (5) and
rotate the ad just ing screw (17) CCW until
re moved from the spring cham ber (2).
SECTION VI
VI. MAINTENANCE
4. Draw or em bed a match mark on the body (1)
and spring chamber (2) flanges.
5. If the special tool in Figure 1 is not being used,
the piston spring (20) is always under ten sion.
Therefore remove all flange bolts (13)
except two located on opposite sides. Turn
remaining two flange bolts (13) CCW using
even in cre ments. The piston spring (20) will
force the body (1) and spring cham ber (2) to
separate.
6. Remove spring chamber (2), spring buttons
(4), range spring (6), ball bearing (9),
pressure plate (8), diaphragms (10), and
diaphragm gasket (11).
7. Inspect pressure plate (8) for de for ma tion due
to over-pressurization. If de formed, re place.
8. Clean all parts to be reused according to
own er's procedures.
NOTE:
On reg u la tors
orig i nal ly sup plied as “spe cial cleaned”,
Op tion-55, main te nance must in clude a
level of clean li ness equal to Cash co’s
clean ing stan dard #S-1134. On reg u la tors
orig i nal ly sup plied as “spe cial cleaned”,
Op tion-56, main te nance must in clude a level
of clean li ness equal to Cash co’s clean ing
stan dard #S-1542. Con tact fac to ry for details.
SECTION V
2. If the reg u la tor and system are both to be
shut down, slowly close the inlet (upstream) block
valve. Close the outlet (downstream) valve only if
regu la tor re moval is required.
V. SHUTDOWN
1. On systems with a bypass valve, and where
sys tem pres sure is to be maintained as the
regu la tor is shut down, slowly open the bypass
valve while closing the inlet (upstream) block
valve. Fully close the inlet (up stream) block valve.
(When on bypass, the system pressure must be
con stant ly observed and manually reg u lat ed.
Close the outlet (down stream) block valve.
Figure 1:
Special tool for collapsing piston spring (20).
CAUTION
Do not walk away and leave a bypassed reg u la tor
un at tend ed!
WARNING
SYSTEM UNDER PRESSURE. Prior to performing any
main te nance, isolate the regulator from the system
and relieve all pressure. Failure to do so could result in
personal injury.
WARNING
SPRING UNDER COMPRESSION. Prior to removing flange
bolts, relieve spring compression by backing out the ad-
justing screw. Failure to do so may result in flying parts
that could cause personal injury.