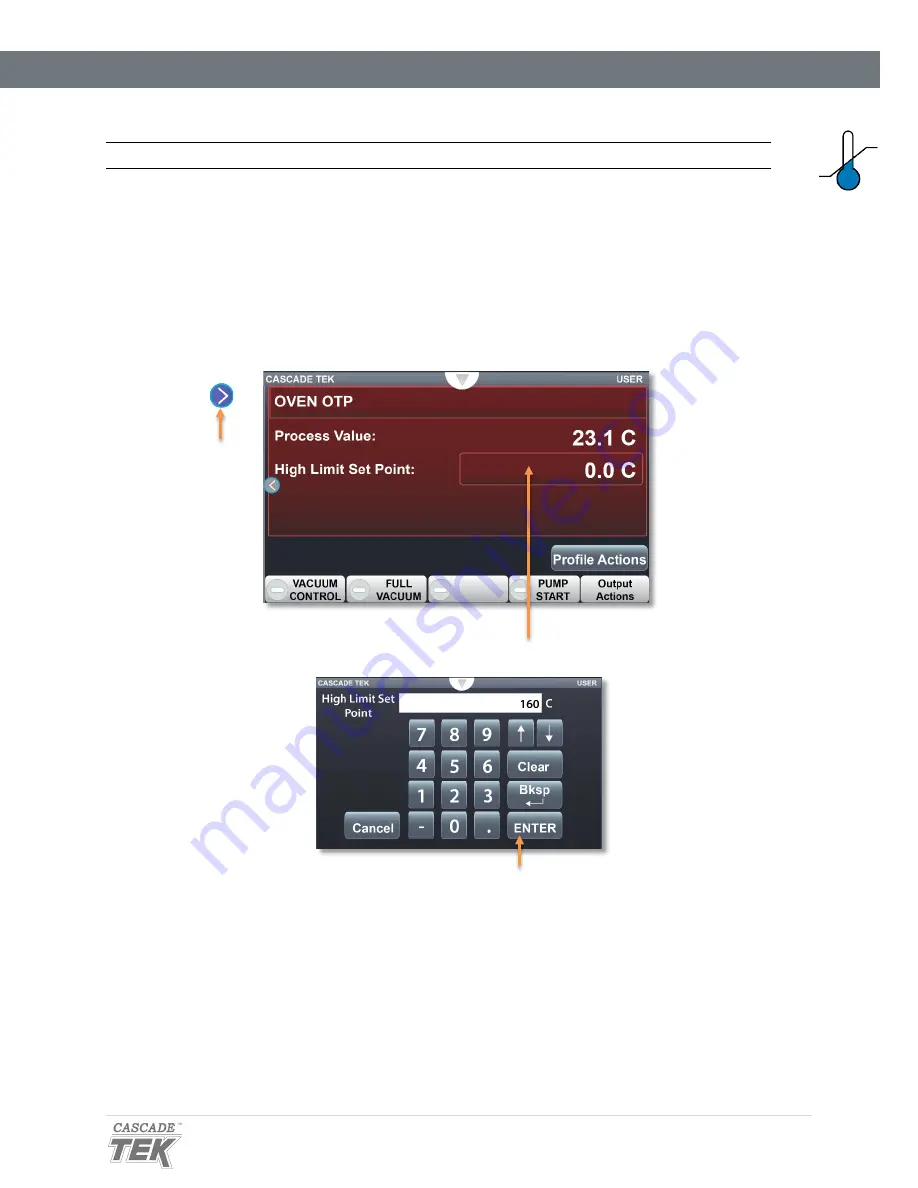
41
|
P a g e
OPERATION
S
ET THE
O
VEN
L
IMIT
(OTP)
T
EMPERATURE
Note:
Test the oven limit system once per year for functionality.
Set the oven limit threshold where the independent Temperature Limit circuitry cuts off heating of
the oven chamber.
Considerations when setting the oven limit cutoff:
•
Set the limit prior to activating heating.
•
The oven limit cutoff setpoint should be set
at least 10°C
above the highest temperature of your
baking application.
1.
Tap the right chevron button to bring up the Oven Limit page.
2.
Tap the High Limit Set Point button.
3.
Set the temperature cutoff limit
4.
Return to the Homepage.
End of Procedure
Tap
Tap
Tap
Содержание CTVR522-H
Страница 1: ...Vacuum Control Oven SVO 5 VC Installation and Operation Manual ...
Страница 6: ...6 P a g e TABLE OF CONTENTS ...
Страница 16: ...16 P a g e RECEIVING ...
Страница 28: ...28 P a g e SYMBOLS ...
Страница 34: ...34 P a g e CONTROLS ...