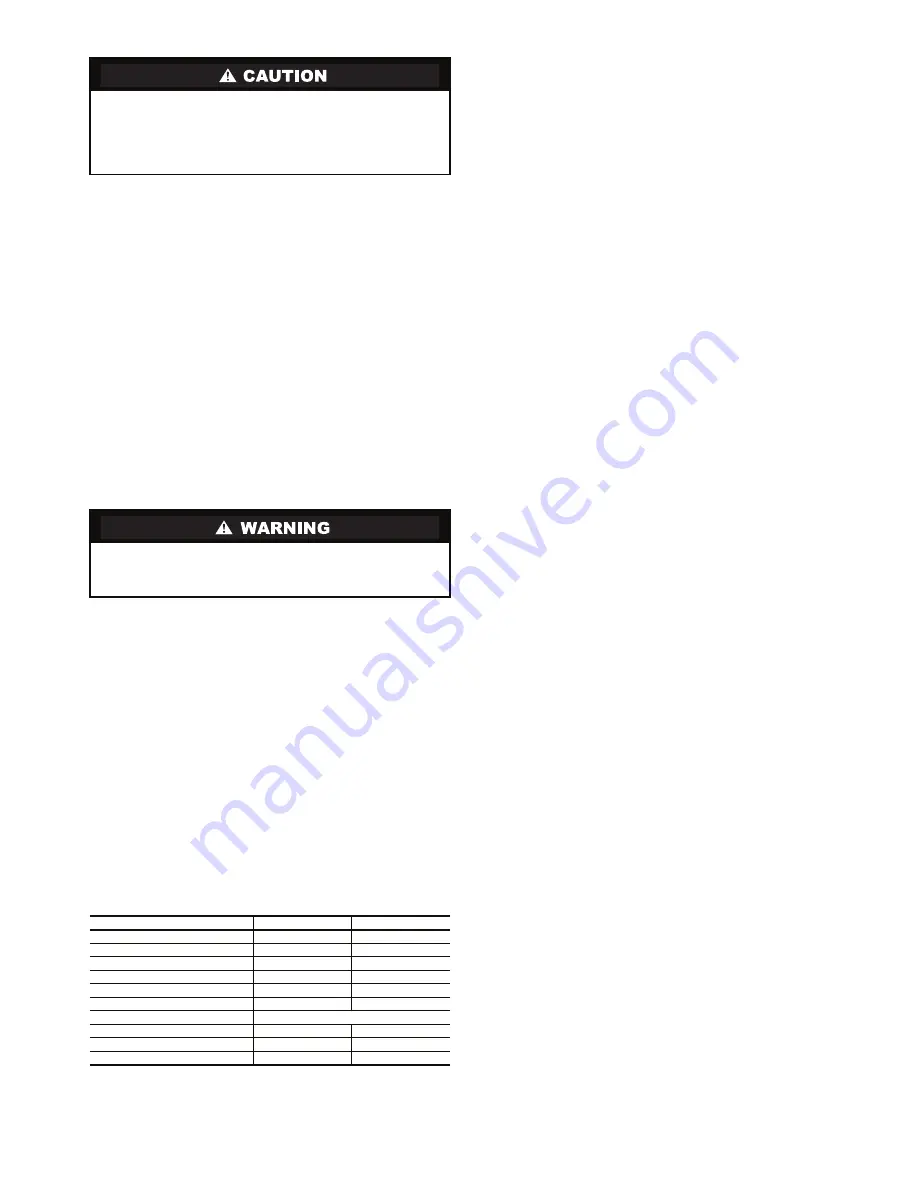
33
START-UP
Use the procedure outlined below to initiate proper unit
start-up.
NOTE: This equipment is designed for indoor installation only.
Operating Limits
ENVIRONMENT — This equipment is designed for indoor
installation ONLY. Extreme variations in temperature, humidi-
ty and corrosive water or air will adversely affect the unit per-
formance, reliability and service life.
POWER SUPPLY — A voltage variation of ± 10% of name-
plate utilization voltage is acceptable.
UNIT STARTING CONDITIONS — All units start and op-
erate in an ambient of 45 F with entering-air at 40 F, entering-
water at 20 F and with both air and water at the flow rates used.
NOTE:
These operating conditions are not normal or continu-
ous operating conditions. It is assumed that such a start-up is
for the purpose of bringing the building space up to occupancy
temperature.
Start Up System
1. Restore power to system.
2. Turn thermostat fan position to ON. Blower should start.
3. Balance airflow at registers.
4. Adjust all valves to the full open position and turn on the
line power to all heat pump units.
5. Operate unit in the cooling cycle. Room temperature
should be approximately 45 to 100 F dry bulb. Loop
water temperature entering the heat pumps should be
between 40 and 90 F.
NOTE: Three factors determine the operating limits of a
unit: (1) entering-air temperature, (2) water temperature and
(3) ambient temperature. Whenever any of these factors are
at a minimum or maximum level, the other two factors must
be at a normal level to ensure proper unit operation. See
Table 21.
Table 21 — 50HQL,VQL Units
Operating Limits
LEGEND
*With antifreeze, optional extended range insulation and low temperature cut-
out jumper clipped for antifreeze.
Scroll Compressor Rotation —
It is important to be
certain compressor is rotating in the proper direction. To
determine whether or not compressor is rotating in the proper
direction:
1. Connect service gages to suction and discharge pressure
fittings.
2. Energize the compressor.
3. The suction pressure should drop and the discharge
pressure should rise, as is normal on any start-up.
If the suction pressure does not drop and the discharge
pressure does not rise to normal levels:
1. Turn off power to the unit. Install disconnect tag.
2. Reverse any two of the unit power leads.
3. Reapply power to the unit and verify pressures are correct.
The suction and discharge pressure levels should now move
to their normal start-up levels.
When the compressor is rotating in the wrong direction, the
unit makes an elevated level of noise and does not provide
cooling.
After a few minutes of reverse operation, the scroll com-
pressor internal overload protection will open, thus activating
the unit lockout. This requires a manual reset. To reset, turn the
thermostat on and then off.
NOTE: There is a 5-minute time delay before the compressor
will start.
Unit Start-Up Cooling Mode
1. Adjust the unit thermostat to the warmest position.
Slowly reduce the thermostat position until the compres-
sor activates.
2. Check for cool air delivery at unit grille a few minutes
after the unit has begun to operate.
3. Verify that the compressor is on and that the water flow
rate is correct by measuring pressure drop through the
heat exchanger using P/T plugs. Check the elevation and
cleanliness of the condensate lines; any dripping could be
a sign of a blocked line. Be sure the condensate trap in-
cludes a water seal.
4. Check the temperature of both supply and discharge
water.
5. Air temperature drop across the coil should be checked
when compressor is operating. Air temperature drop
should be between 15 and 25 F.
Unit Start-Up Heating Mode
NOTE: Operate the unit in heating cycle after checking the
cooling cycle. Allow 5 minutes between tests for the pressure
or reversing valve to equalize.
1. Turn thermostat to lowest setting and set thermostat
switch to HEAT position.
2. Slowly turn the thermostat to a higher temperature until
the compressor activates.
3. Check for warm air delivery at the unit grille within a few
minutes after the unit has begun to operate.
4. Check the temperature of both supply and discharge
water.
5. Air temperature rise across the coil should be checked
when compressor is operating. Air temperature rise
should be between 20 and 30 F after 15 minutes at load.
6. Check for vibration, noise and water leaks.
Flow Regulation —
Flow regulation can be accom-
plished by two methods. Most water control valves have a flow
adjustment built into the valve. By measuring the pressure drop
through the unit heat exchanger, the flow rate can be deter-
mined. Adjust the water control valve until the flow of 1.5 to
2 gpm is achieved. Since the pressure constantly varies, two
pressure gages may be needed in some applications.
To avoid equipment damage, DO NOT leave system filled
in a building without heat during the winter unless anti-
freeze is added to system water. Condenser coils never
fully drain by themselves and will freeze unless winterized
with antifreeze.
When the disconnect switch is closed, high voltage is
present in some areas of the electrical panel. Exercise
caution when working with the energized equipment.
AIR LIMITS
COOLING (F)
HEATING (F)
Min. Ambient Air
45
45
Rated Ambient Air
80
70
Max. Ambient Air
100
85
Min. Ent. Air
50
40
Normal Entering Air db/wb
75/63-80/67
70
Max. Entering Air db/wb
110/83
80
WATER LIMITS
Min. Entering Water
*30
45 (*20)
Normal Entering Water
40-90
40-90
Max. Entering Water
110
90
db
—
Dry Bulb
wb
—
Wet Bulb