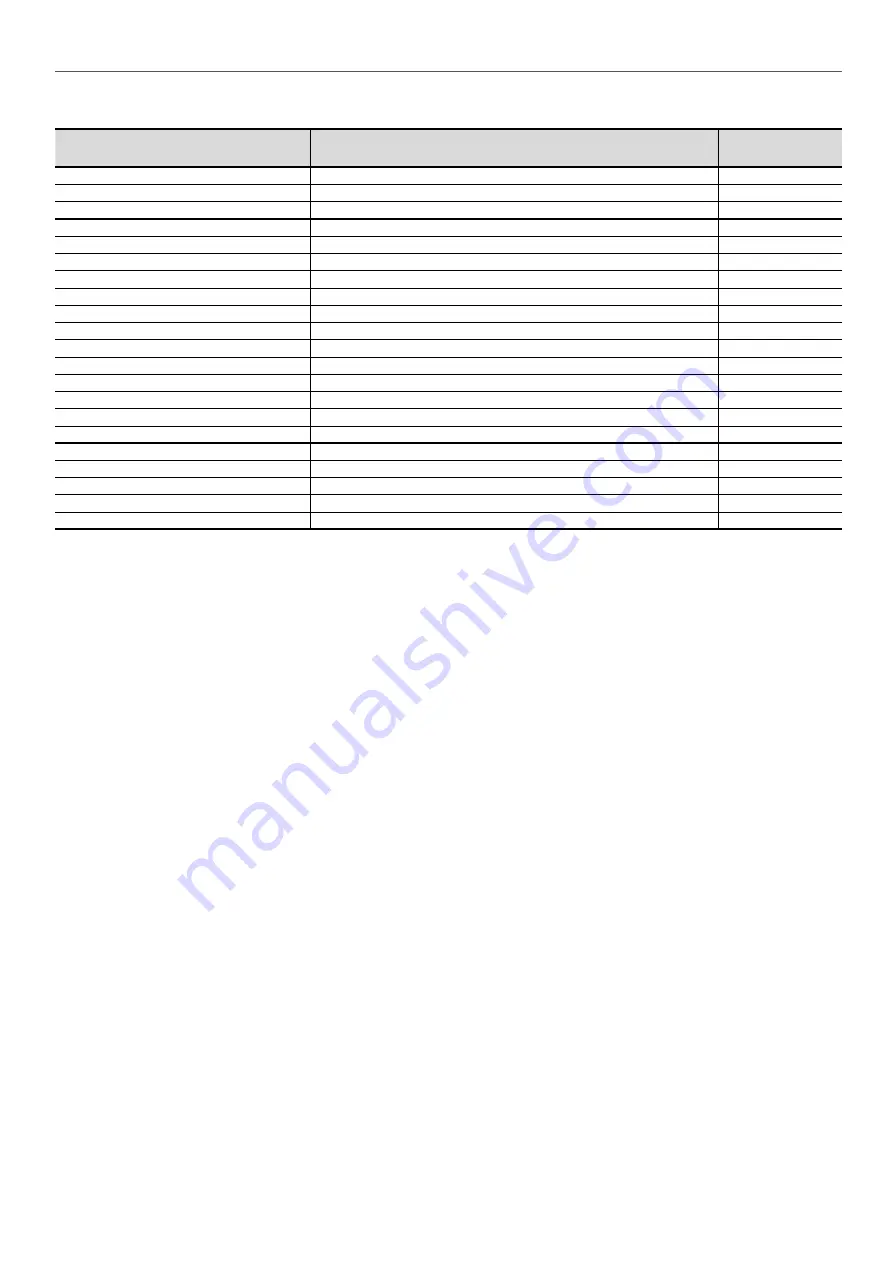
29
11 - STANDARD MAINTENANCE
11.5 -
Tightening torques for the main bolts and screws
Screw type
Used for
Torque value, N·m
M20 nut
Chassis
190
M20 nut
Heat exchanger side-side connection
240
M16 nut
Compressor fixing
190
H M16 screw
Heat exchanger water boxes, structure
190
H M16 screw
Compressor suction flanges TT
190
H M20 screw
Compressor suction flanges TU & TV
240
M16 nut
Compressor discharge line TT & TU
190
M20 nut
Compressor discharge line TV
240
H M12 screw
Economiser port flange & economiser port valve, option 92
80
H M8 screw
Drier cover
35
1/8 NPT connection
Oil line
12
TE nut
Compressor oil line
24,5
1 1/16-12 UNF-2A
Oil level
130
7/8 ORFS nut
Oil line & injection line
130
5/8 ORFS nut
Oil line
65
3/8 ORFS nut
Oil line
26
H M6 screw
Stauff collar
10
Taptite screw M6
Oil line collar
7
Taptite screw M6
Brass body, economiser line
10
Metric screw M6
Steel plate fixing, control box, terminal box
7
Taptite screw M10
Oil filter, economiser module, control box fixing
30
11.6 - Evaporator and condenser maintenance
Check that:
the insulating foam is intact and securely in place,
the sensors and flow switch are correctly operating and correctly
positioned in their support,
the water-side connections are clean and show no sign of leakage.
11.7 - Compressor maintenance
11.7.1 -
Oil filter change schedule
As system cleanliness is critical to reliable system operation, there
is a filter in the oil line at the oil separator outlet. The oil filter is
specified to provide a high level of filtration (5 µm) required for
long compressor life.
The filter should be checked after the first 500 hours of operation,
and every subsequent 2000 hours. The filter should be replaced
at any time when the pressure differential across the filter exceeds
2 bar.
The pressure drop across the filter can be determined by
measuring the pressure at the discharge port (at the oil separator)
and the oil pressure port (at the compressor).
The difference in these two pressures will be the pressure drop
across the filter, check valve, and solenoid valve. The pressure
drop across the check valve and solenoid valve is approximately
0.4 bar, which should be subtracted from the two oil pressure
measurements to give the oil filter pressure drop.
11.7.2 - Compressor rotation control
Correct compressor rotation is one of the most critical application
considerations. Reverse rotation, even for a very short duration,
damages the compressor and can even destroy it.
The reverse rotation protection scheme must be capable of
determining the direction of rotation and stopping the compressor
within one second. Reverse rotation is most likely to occur
whenever the wiring at the compressor terminals has been
modified.
To minimise the opportunity for reverse rotation, the following
procedure must be applied. Rewire the power cables to the
compressor terminal pin as originally wired. Apply a counter-torque
at the lower nut at the supply cable terminal during installation.
For replacement of the compressor, a low pressure switch is
included with the compressor. This low pressure switch should be
temporarily installed as a hard safety on the high pressure part of
the compressor. The purpose of this switch is to protect the
compressor against any wiring errors at the compressor terminal
pin. The electrical contact of the switch would be wired in series
with the high pressure switch. The switch will remain in place until
the compressor has been started and direction of rotation has
been verified; at this point, the switch will be removed.
The switch that has been selected for detecting reverse rotation
is Carrier part number HK01CB001. This switch opens the contacts
when the pressure falls below 7 kPa. The switch is a manual reset
type that can be reset after the pressure has once again risen
above 70 kPa. It is critical that the switch be a manual reset type
to preclude the compressor from short cycling in the reverse
direction
11.8 -
Expansion valves maintenance
Replacing of all expansion valves motor is mandatory after 33000
hours of operation.
Maintenance work must be carried out by a trained person fully
qualified to work on these units. Please contact your Carrier
Service representative for information.
NOTE: Any deviation or non-observation of these maintenance
criteria will render the guarantee conditions for the heatpump unit
null and void, and the manufacturer will no longer be held
responsible.