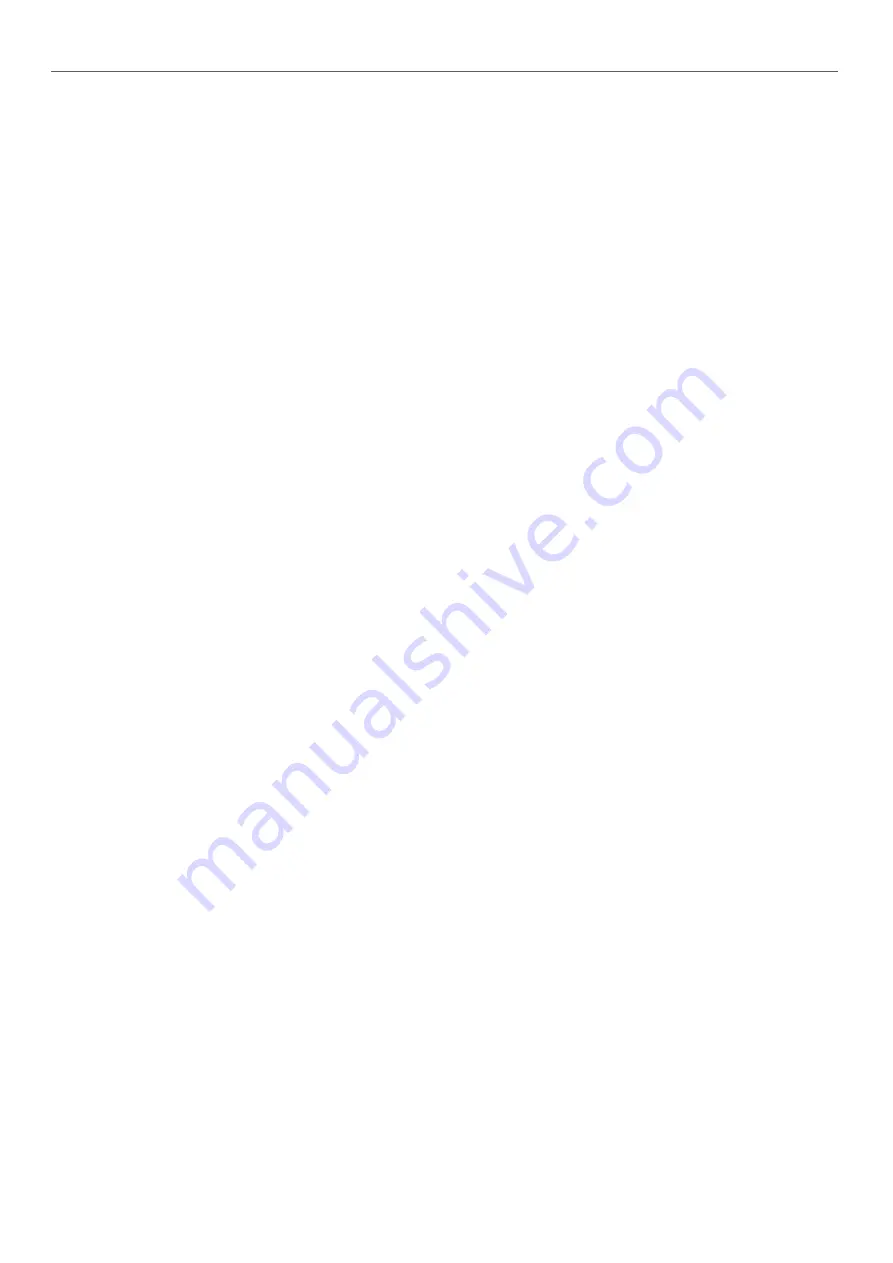
24
9 - MAJOR SYSTEM COMPONENTS AND OPERATION DATA
9.2.1 - Evaporator
61XWH heat pumps use a flooded multi-tube evaporator. The
water circulates in the tubes and the refrigerant is on the outside
in the shell. One vessel is used to serve both refrigerant circuits.
There is a center tube sheet which separates the two refrigerant
circuits. The tubes are 3/4” diameter copper with an enhanced
surface inside and out.
There is just one water circuit with two water passes (one pass
with option 100C and three passes with option 100A, please refer
to chapter 7.5).
The evaporator shell has a polyurethane foam thermal insulation
and a water drain and purge.
It has been tested and stamped in accordance with the applicable
pressure codes. The maximum standard relative operating
pressure is 2100 kPa for the refrigerant side and 1000 kPa for the
water-side. These pressures can be different depending on the
code applied. The water connection of the heat exchanger is a
Victaulic connection.
The products that may be added for thermal insulation of the
containers during the water piping connection procedure must be
chemically neutral in relation to the materials and coatings to which
they are applied. This is also the case for the products originally
supplied by Carrier.
9.2.2 - Condenser and oil separator
The 61XWH heat pumps uses a heat exchanger that is a
combination condenser and oil separator. It is mounted below the
evaporator. Discharge gas leaves the compressor and flows
through an external muffler to the oil separator, which is the upper
portion of the heat exchanger. It enters the top of the separator
where oil is removed, and then flows to the bottom portion of the
vessel, where gas is condensed and subcooled. One vessel is
used to serve both refrigerant circuits. There is a center tube sheet
which separates the two refrigerant circuits. The tubes are 3/4” or
1” diameter internally and externally finned copper tubes.
The oil, once separated from refrigerant, is flowing to an oil receiver
(oil tank).The valve present on top of the tank must be closed
while operating. During refrigerant recovery, vacuum or refrigerant
charging, this valve can be connected via a flexible hose to the
condenser service valve in order to avoid air or other incondensable
substances trapping at the top of the oil receiver.
There is just one water circuit with two water passes (one pass
with option 102C and three passes with option 102A, please refer
to chapter 7.5).
It has been tested and stamped in accordance with applicable
pressure codes. The maximum standard relative operating
pressure is 3000 kPa for the refrigerant side and 1000 kPa for the
water-side. These pressures can be different depending on the
code applied. The water connection of the heat exchanger is a
Victaulic connection.
9.2.3 - Economiser function (depending on model)
The economiser function includes a liquid line valve, a filter drier,
two electronic expansion valves (EXVs), a plate heat exchanger
as well as protection devices.
At the condenser outlet a part of the liquid is expanded via the
secondary EXV in one of the heat exchanger circuits and then
returns as a gas. This expansion permits increase of the liquid
sub-cooling of the rest of the flow that penetrates the evaporator
via the principal EXV. This permits increasing the cooling capacity
of the system as well as its efficiency.
9.3 - Detection of the air pressurization of the
electrical cabinet
The electrical cabinet is equipped (except units with option 330)
with a function for detection of its air pressurization. It is made of
a differential pressure sensor that provides a signal to a voltage
relay. This function insures that the cabinet is always pressurized
above 5Pa in order to avoid any ingress of refrigerant inside the
cabinet. It is aimed at stopping the unit or preventing it from starting
if the pressure differential between the inside and the outside of
the cabinet is lower than the threshold value. This can happen:
-
If the cooling fan of the electrical box fails or if the inlet or
exhaust openings are getting fouled
-
If the ducting providing fresh air to the cabinet (refer to §1
p6) is too much resistant to air flow or fouled
-
If the cabinet is not tight enough (especially mind the power
input plate and cable glands)
9.4 -
Electronic expansion valve (EXV)
The EXV is equipped with a stepper motor (2785 to 3690 steps,
depending on the model) that is controlled via the EXV board.
The EXV is also equipped with a sightglass that permits verification
of the mechanism movement and the presence of the liquid gasket.
For maintenance instruction on expansion valves please refer to
paragraph 12.8.
9.5 - Moisture indicator
Located on the EXV, permits control of the unit charge and
indicates moisture in the circuit. The presence of bubbles in the
sight-glass indicates an insufficient charge or non-condensables
in the system. The presence of moisture changes the colour of
the indicator paper in the sight-glass.
9.6 - Filter drier
The role of the filter drier is to keep the circuit clean and moisture
free. The moisture indicator shows, when it is necessary to change
the element. A difference in temperature between the filter inlet and
outlet shows that the element is dirty.
9.7 - Sensors
The unit uses thermistors to measure the temperature, and
pressure transducers to control and regulate system operation
(see Touch Pilot Control IOM for a more detailed explanation).
9.8 - SRMCR high-pressure safety circuit
9.8.1 - General description
The device is equipped with a high pressure safety loop, also
known as safety related measurement control and regulation
system (SRMCR), consisting of:
-
2 high pressure switches (HPS) with manual reset located
at the outlet of each compressor:
• A pressure switch type PZH
• A pressure switch type PZHH
-
A control relay on the compressor board
-
2 compressor main contactors
See the wiring diagram and bill of material of the unit for details
of identification and references.
This safety loop is designed according to EN 61508 for:
SIL level (Safety Integrity): 2
Demand mode: high and low
Mission Time: 20 years.
Periodic test: The safety loop operation must be tested at least
once a year to maintain its integrity.