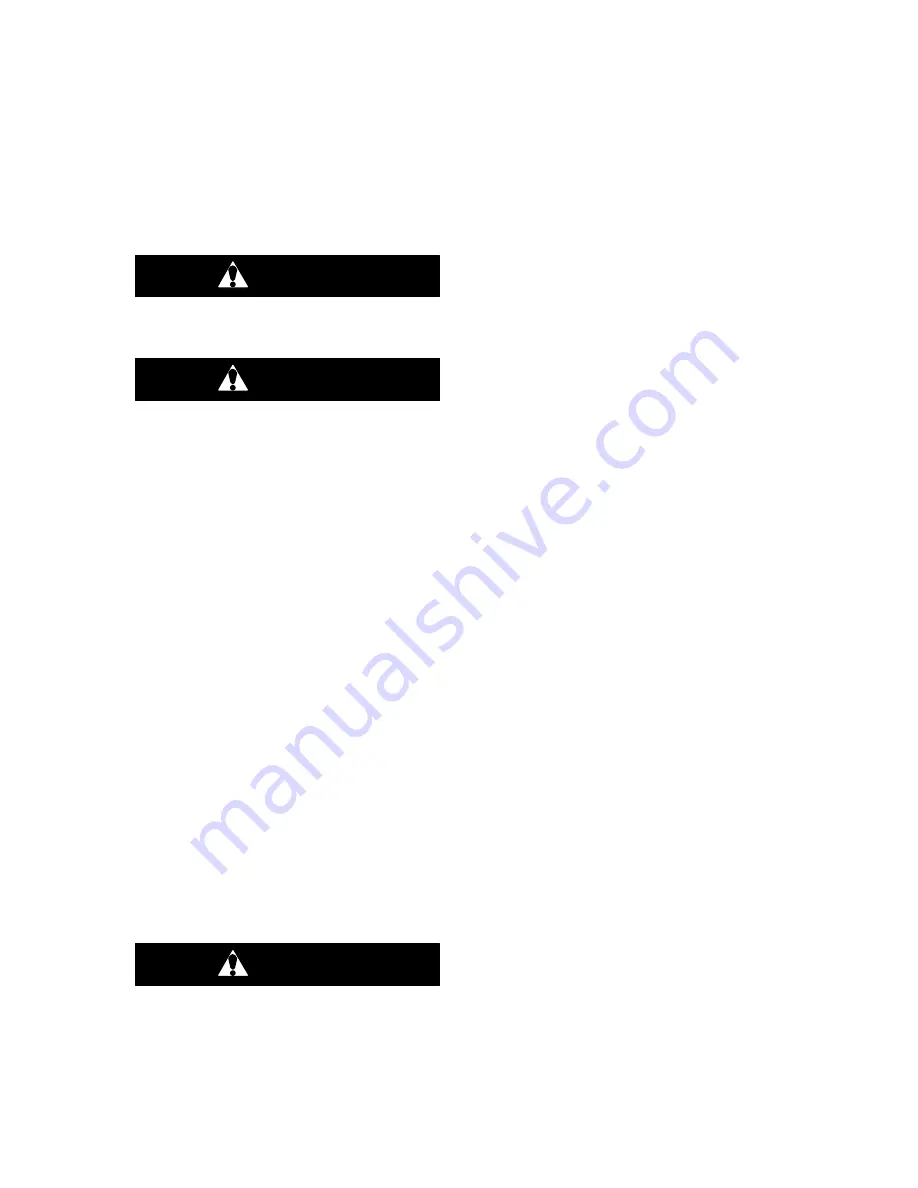
6
−
9
T
−
318
6.8.5 Installing the Components
a. Push pistons from the inside of the crankcase through
the cylinders, being careful not to break the rings.
Place rods so that the chamfered side will be against
radius of crankpins. Install the crankshaft and thrust
washer through the pump end of the compressor. En-
sure thrust washer is fitted on locating pin. Do not
damage main bearings. Bring rods in position against
crank bearings.
b. Install the pump end thrust washer on the two dowel
pins located on the bearing head (see Figure 6-8).
CAUTION
Ensure that thrust washer does not fall off
dowel pins while installing oil pump.
CAUTION
The set screw on the crankshaft must be
removed for this type of oil pump (see
c. Install the bearing head assembly with a new gasket
on the compressor crankshaft. Carefully push oil
pump on by hand, ensuring the thrust washer re-
mains on the dowel pins. The tang on the end of the
drive engages the slot in the crankshaft, and the oil
inlet port on the pump is aligned with the oil pickup
tube in the crankcase. The pump should be mounted
flush with the crankcase, and oriented with the oil pick
up tube and oil inlet port, and aligned as shown in
d. Align the gasket and install the eight cap screws in the
mounting flange. Refer to Table 6-8 for applicable
torque values.
e. Install matching connecting rod caps Be sure rod is
not bound and crankshaft will turn correctly as each
set of rod bolts is torqued.
f. Be sure key fits properly when installing rotor on
shaft. Screw on equalizer tube and lock screw
assembly with lock washer and bend over tabs of lock
washer. Assemble suction strainer to motor and
cover, and bolt cover to crankcase. Assemble valve
plates and gaskets. Assemble cylinder heads and
gaskets. Turn the shaft by hand to see that it moves
freely.
g. Install the oil suction screen, the oil suction screen
hold down plate, and the bottom plate.
6.8.6 Compressor Oil Level
CAUTION
Use only Carrier Transicold approved
Polyol Ester Oil (POE)
−
Castrol-Icematic
SW20 compressor oil with R-134a. Buy in
quantities of one quart or smaller. When
using this hygroscopic oil, immediately
reseal. Do not leave container of oil open or
contamination will occur.
a. Checking the Oil Level in the Compressor
1. Operate unit in cooling mode for at least 20 minutes.
2. Check the front oil sight glass on the compressor to
ensure that no foaming of the oil is present after 20
minutes of operation. If the oil is foaming excessively
after 20 minutes of operation, check the refrigerant
system for flood-back of liquid refrigerant. Correct
this situation before performing step 3.
3. Turn unit off to check the oil level. The correct oil level
range should be between the bottom to one-eighth
level of the sight glass. If the level is above one-
eighth, oil must be removed from the compressor. To
remove oil from the compressor, follow step d in this
section. If the level is below the bottom of the sight
glass, add oil to the compressor following step b
below.
b. Adding Oil with Compressor in System
1. The recommended method is to add oil using an oil
pump at the oil fill valve (see item 11, Figure 6-5).
2. In an emergency where an oil pump is not available,
oil may be drawn into the compressor through the
suction service valve.
Connect the suction connection of the gauge man-
ifold to the compressor suction service valve port,
and immerse the common connection of the gauge
manifold in an open container of refrigeration oil.
Extreme care must be taken to ensure the manifold
common connection remains immersed in oil at all
times. Otherwise air and moisture will be drawn into
the compressor.
Crack the suction service valve and gauge valve to
vent a small amount of refrigerant through the com-
mon connection and the oil to purge the lines of air.
Close the gauge manifold valve.
With the unit running, frontseat the suction service
valve and induce a vacuum in the compressor crank-
case. SLOWLY crack the suction gauge manifold
valve and oil will flow through the suction service
valve into the compressor. Add oil as necessary.
c. Adding Oil to Service Replacement Compressor
Service replacement compressors are shipped without
oil. If oil is present in the crankcase, it must be tested to
ensure it is the correct oil and that the moisture level is
acceptable.
When adding oil to a service replacement compressor
add three liters (6.3 pints) using an oil pump at the oil fill
valve (see item 11, Figure 6-5). This quantity is
recommended to allow for return of any oil that may be in
the refrigerant system. Install compressor and check oil
level after it is placed in operation (refer to paragraph
6.8.6).
d. Removing Oil from the Compressor
1. If the oil level is above one-eighth sight glass, oil
must be removed from the compressor.
2. Close (frontseat) suction service valve and pump
unit down to 1.2 to 1.3kg/cm
(2 to 4psig). Frontseat
discharge service valve and remove remaining re-
frigerant.
3. Loosen the oil drain plug on the bottom plate of the
compressor and drain the proper amount of oil from
the compressor to obtain the correct level.
Backseat
the suction and discharge service valves.
4. Repeat step a to ensure proper oil level.
Содержание 69NT40-541-300
Страница 2: ......
Страница 4: ......
Страница 20: ......
Страница 32: ......
Страница 128: ......
Страница 131: ...7 3 T 318 Based on Drawing 62 66058 Figure 7 2 SCHEMATIC DIAGRAM Units with 3 Phase Evaporator Motors...
Страница 133: ...7 5 T 318 6 Heater FCCH FCCH Figure 7 4 SCHEMATIC DIAGRAM Units with Normal Evaporator Fan Capability...
Страница 134: ...7 6 T 318 FCCH FCCH Figure 7 5 SCHEMATIC DIAGRAM Units with Single Evaporator Fan Capability...
Страница 136: ...7 8 T 318 To ST10 To TRX2 To QC1 To QC1 To QC1 To MC6 CONTROLLER Figure 7 7 SCHEMATIC DIAGRAM Emergency Bypass...
Страница 138: ...7 10 T 318 Based on Drawing 62 66058 Figure 7 9 UNIT WIRING DIAGRAM Units with 3 Phase Evaporator Motors Sheet 1 of 2...
Страница 139: ...7 11 T 318 Based on Drawing 62 66058 Figure 7 10 UNIT WIRING DIAGRAM Units with 3 Phase Evaporator Motors Sheet 2 of 2...
Страница 144: ......
Страница 150: ......
Страница 151: ......