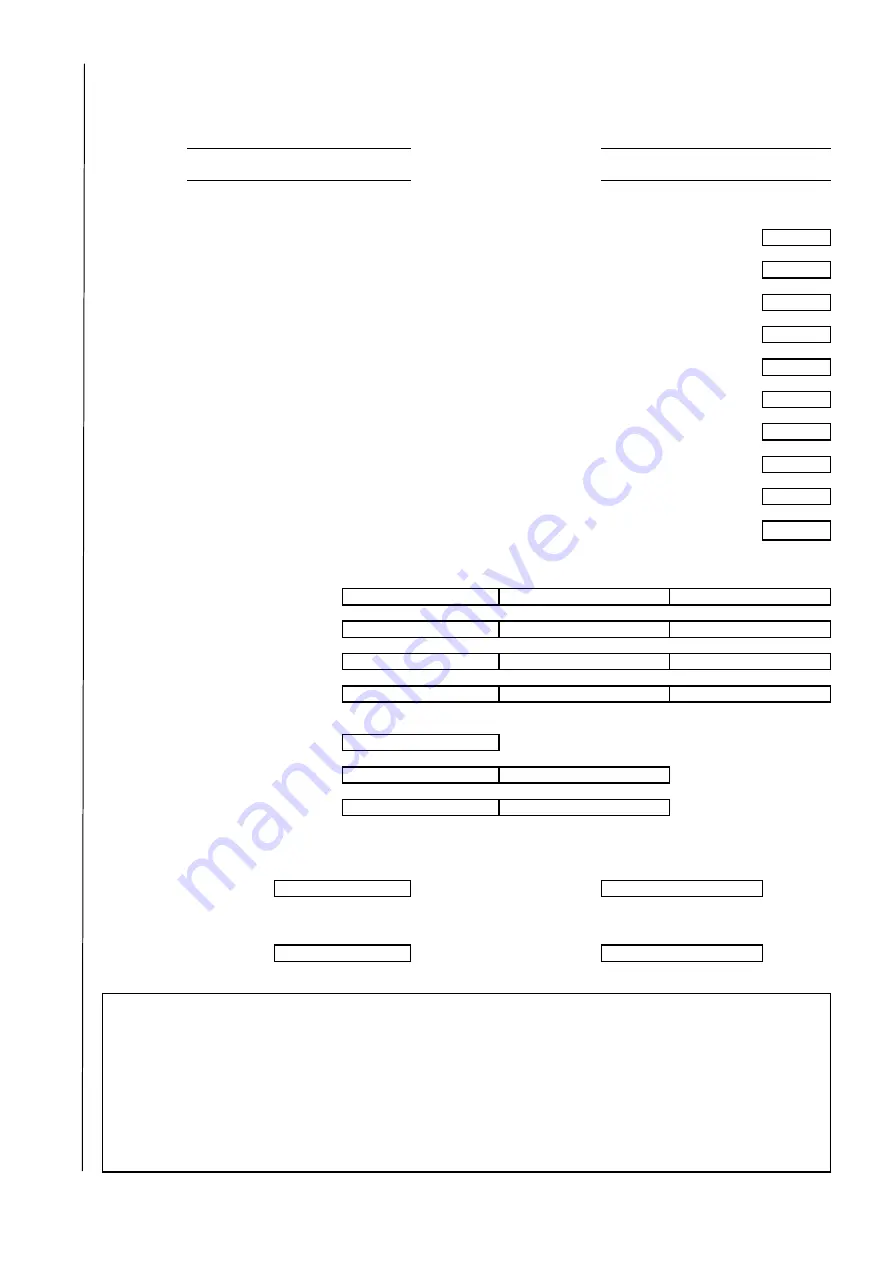
START-UP CHECKLIST
MODEL NO:
DATE:
SERIAL NO:
TECHNICIAN:
3) CONDENSATE CONNECTION IS INSTALLED PER INSTALLATION INSTRUCTION.
4) UNIT GROUNDING WIRE HAS BEEN CONNECTED.
5) POWER WIRES HAVE BEEN SIZED AND INSTALLED PROPERLY TO THE UNIT.
6) CONTROL WIRING CONNECTIONS HAVE BEEN INSTALLED PROPERLY.
7) CHECK ALL WIRING TERMINALS HAVE BEEN TIGHTENED PROPERLY.
(Remove and Store in Job File)
II. PRE-START-UP (Insert checkmark in box as each item is completed)
I. PRELIMINARY INFORMATION
2) VERIFY THAT UNIT INSTALLATION IS LEVEL.
1) ALL PACKING MATERIALS HAVE BEEN REMOVED FROM THE UNIT.
(T
ear
A
long T
hi
s Li
ne)
(L2):
(L2):
III. START - UP
ELECTRICAL:
8) ENERGIZE CRANKCASE HEATERS FOR 12 HOURS.
9) CORRECT FAN ROTATION HAS BEEN CONFIRMED.
10) SEALED ALL POWER AND CONTROL WIRES ENTRY INTO THE UNIT AND INSIDE THE BOX
(L3 - L1):
(L3):
(L3):
(L3):
(L2 - L3):
(L2):
TEMPERATURES:
(BOTH CIRCUITS OPERATING)
SUPPLY VOLTAGE:
COMPRESSOR - 1 AMPS:
COMPRESSOR - 2 AMPS:
INDOOR FAN AMPS:
(L1 - L2):
(L1):
(L1):
(L1):
OUTDOOR AIR:
INDOOR SECTION ENTERING AIR:
INDOOR SECTION LEAVING AIR:
: DB
: DB
: DB
:WB
:WB
PRESSURES:
CIRCUIT - 1
CIRCUIT - 2
REFRIGERANT SUCTION
Notes:
VERIFY REFRIGERANT CHARGE USING CHARGING CHART.
REFRIGERANT SUCTION
REFRIGERANT DISCHARGE
REFRIGERANT DISCHARGE
:PSIG
:PSIG
:PSIG
:PSIG
Page 39
Содержание 50TCM Series
Страница 6: ... LPHQVLRQV 7 8 85 6 76 0 16 216 7 007 Page 6 ...
Страница 8: ... 85 6 76 0 16 216 7 0 LPHQVLRQV 7 5 5 Page 8 ...
Страница 10: ... LPHQVLRQV 7 85 6 76 0 16 216 7 0 5 5 Page 10 ...
Страница 24: ...Typical Wiring Schematic 50TCMA07 400V Page 24 ...
Страница 25: ...Typical Wiring Schematic 50TCMD08 09 400V Page 25 ...
Страница 26: ...Typical Wiring Schematic 50TCMD12 14 400V Page 26 ...
Страница 27: ...Typical Control Schematic 50TCMA Series Page 27 ...
Страница 28: ...Typical Control Schematic 50TCMD Series Page 28 ...
Страница 32: ...Charging Chart 400V 50Hz 50TCMA07 Charging Chart 400V 50Hz 50TCMD08 CIR 1 Page 32 ...
Страница 33: ...Charging Chart 400V 50Hz 50TCMD08 CIR 2 Charging Chart 400V 50Hz 50TCMD09 CIR 1 Page 33 ...
Страница 34: ...Charging Chart 400V 50Hz 50TCMD09 CIR 2 Charging Chart 400V 50Hz 50TCMD12 CIR 1 Page 34 ...
Страница 35: ...Charging Chart 400V 50Hz 50TCMD12 CIR 2 Charging Chart 400V 50Hz 50TCMD14 CIR 1 Page 35 ...
Страница 36: ...Charging Chart 400V 50Hz 50TCMD14 CIR 2 Page 36 ...