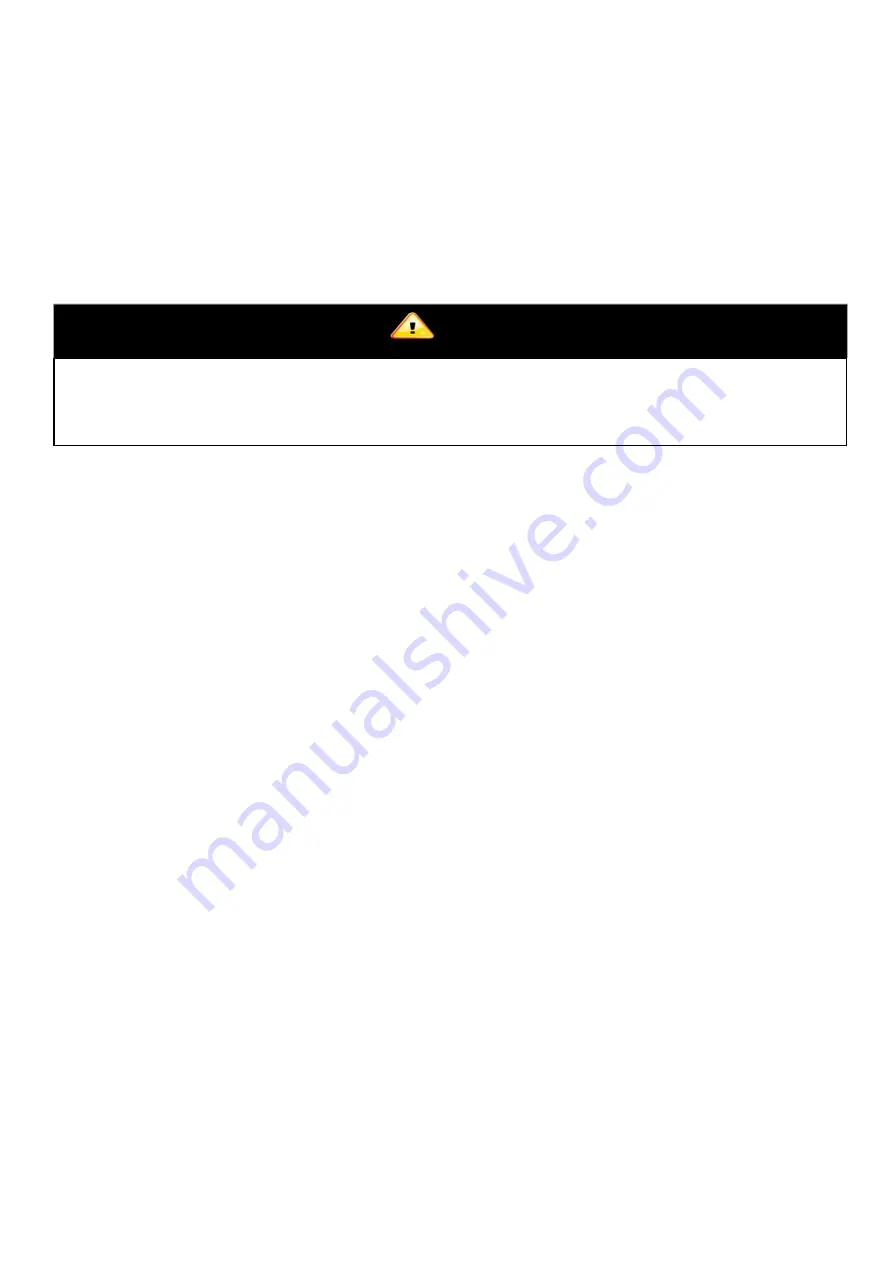
3.5 – Compressor Rotation
It is important to be certain the compressors are rotating in the proper direction. To determine whether or not
compressors are rotating in the proper direction:
1. Connect service gages to suction and discharge pressure fittings.
2. Energize the compressor.
3. The suction pressure should drop and the discharge pressure should rise, as is normal on any start-up.
If the suction pressure does not drop and the discharge pressure does not rise to normal levels:
1. Note that the evaporator fan is probably also rotating in the wrong direction.
2. Turn off power to the unit.
3. Reverse any two of the compressor lead wires.
4. Turn on power to the compressor.
5. Check also phase monitor all ok green led before proceeding.
The suction and discharge pressure levels should now move to their normal start-up levels.
3.6 - Evaporator Fan
Fan belt and variable pulleys are factory installed. Remove tape from the fan pulley. See Table 4 Fan Performance
data. Be sure that fans rotate in the proper direction. See Table 3 Fan RPM at various fan motor pulley settings. To
alter fan performance, see Evaporator Fan Performance Adjustment section.
3.7– Condenser Fans and Motors
Fans and motors are factory set. Refer to Condenser-Fan Adjustment Section as required.
3.8– Return – Air Filters
Check that correct filters are installed in filter tracks. See Table 1 Physical data. Do not operate unit without return
air filters.
3.9 – Base Unit Operation
COOLING, UNITS — when thermostat calls for cooling, terminals G and Y1 are energized. The indoor (evaporator)
fan contactor (IFC), and compressor contactor no. 1 (C1) are energized and evaporator-fan motor, compressor no. 1
and condenser fans start. The condenser-fan motors run continuously while unit is cooling. If the thermostat calls for
a second stage of cooling by energizing Y2, compressor contactor no. 2 (C2) is energized and compressor no. 2
starts.
HEATING, UNITS — (If Accessory or Optional Heater is installed) — upon a call for heating through terminal W1,
IFC and heater contactor no. 1 (HC1) are energized.
NOTE
IMPORTANT
For wire runs up to 50 ft, use no. 18 AWG insulated wire. For 50 to 75 ft, use no. 16 AWG insulated wire. For over 75 ft, use no.
14 AWG insulated wire. All wire larger than no. 18 AWG cannot be directly connected to the thermostat and will require a
junction box and splice at the thermostat.
Page 17
Содержание 50TCM Series
Страница 6: ... LPHQVLRQV 7 8 85 6 76 0 16 216 7 007 Page 6 ...
Страница 8: ... 85 6 76 0 16 216 7 0 LPHQVLRQV 7 5 5 Page 8 ...
Страница 10: ... LPHQVLRQV 7 85 6 76 0 16 216 7 0 5 5 Page 10 ...
Страница 24: ...Typical Wiring Schematic 50TCMA07 400V Page 24 ...
Страница 25: ...Typical Wiring Schematic 50TCMD08 09 400V Page 25 ...
Страница 26: ...Typical Wiring Schematic 50TCMD12 14 400V Page 26 ...
Страница 27: ...Typical Control Schematic 50TCMA Series Page 27 ...
Страница 28: ...Typical Control Schematic 50TCMD Series Page 28 ...
Страница 32: ...Charging Chart 400V 50Hz 50TCMA07 Charging Chart 400V 50Hz 50TCMD08 CIR 1 Page 32 ...
Страница 33: ...Charging Chart 400V 50Hz 50TCMD08 CIR 2 Charging Chart 400V 50Hz 50TCMD09 CIR 1 Page 33 ...
Страница 34: ...Charging Chart 400V 50Hz 50TCMD09 CIR 2 Charging Chart 400V 50Hz 50TCMD12 CIR 1 Page 34 ...
Страница 35: ...Charging Chart 400V 50Hz 50TCMD12 CIR 2 Charging Chart 400V 50Hz 50TCMD14 CIR 1 Page 35 ...
Страница 36: ...Charging Chart 400V 50Hz 50TCMD14 CIR 2 Page 36 ...