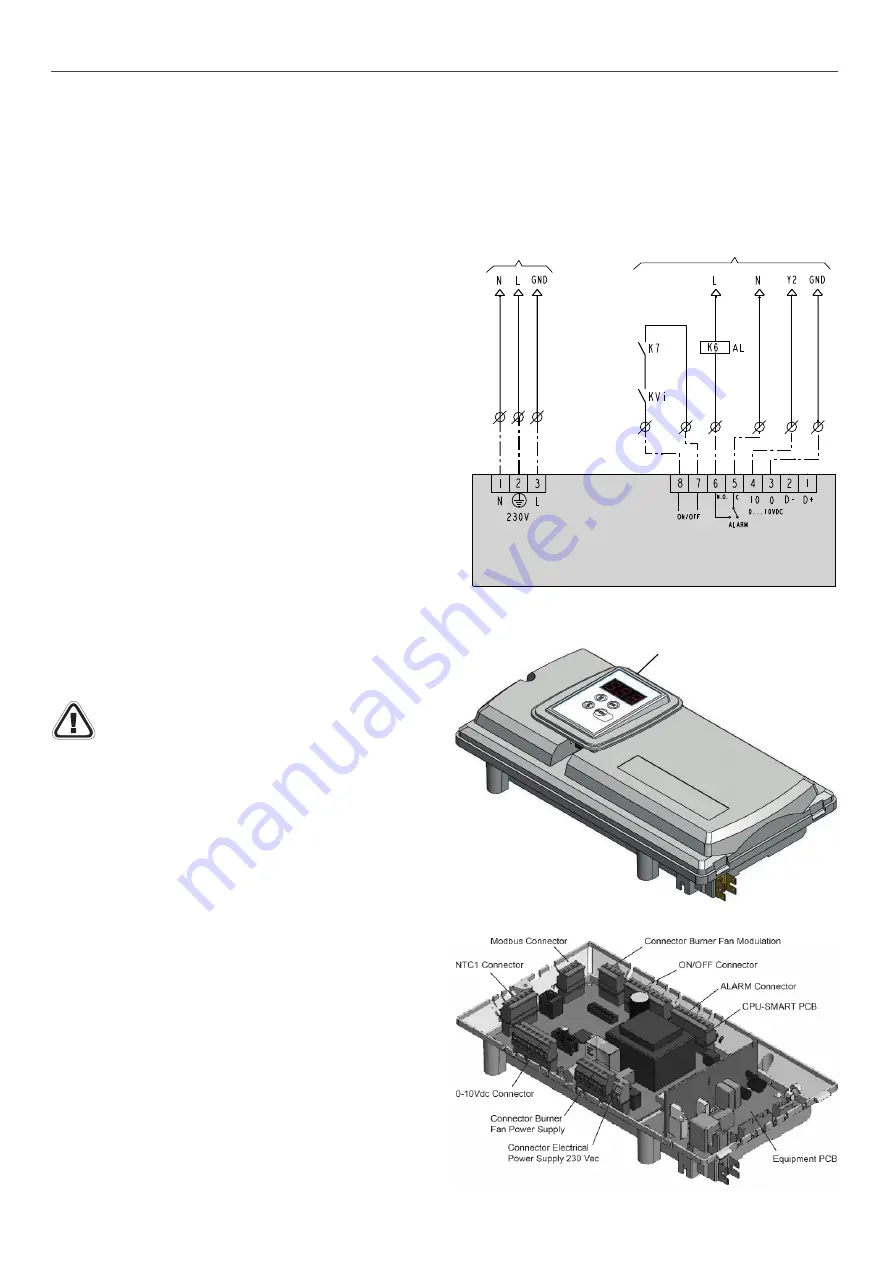
46
12 - FACTORY OPTIONS AND ACCESSORIES
■
Air/gas premixing operation:
The PCH heater is
fi
tted with a burner that completely premixes
air and gas. The air/gas mixing occurs inside the impeller on
the motor-fan.
The air taken into the impeller through the venturi tube,
calibrated, creates a vacuum. The vacuum in the venturi is
rebalanced by the gas valve, which is pneumatically controlled.
The air pressure - gas pressure ratio is 1:1. This ratio can be
corrected by turning the o
ff
set adjustment screw (on the gas
valve). The heater is supplied with the o
ff
set regulated and the
screw sealed.
A second adjustment can be done with the screw on the
venturi, which regulates the value of maximum gas capacity
and determines the amount of carbon dioxide (CO
2
) in the
fl
ue
gases.
This adjustment is also made at the factory. The screw is not
sealed to permit conversion to another type of gas, if desired.
The modulation PCB, mounted on the heater, manages the
motor rotation (in c.c.) depending on the heating capacity
required by the environment. Varying the rotation speed of the
motor changes the air
fl
ow capacity and therefore also the gas
fl
ow capacity. Minimum and maximum rotation values of the
fan are programmed into the PCB and cannot be modi
fi
ed by
the user or installer.
Control of the gas burner
Important:
All the connections to be established by the
client are featured on the wiring diagram included with
the unit.
■
Unit electronic control:
“50FC” control has a proportional output 0/10V (Y2) where
a natural gas or propane gas proportional actuator can be
connected.
The burner connection is managed by the control, in HEATING
mode, through an ON/OFF signal of the digital output NO5
- It is possible to select three operating modes for the burner:
- Operation of the burner as one or two electrical heater stages
(both option not compatible).
- Operation instead of the compressors.
- Operation instead of the compressors if the outdoor
temperature is lower than the value set (5ºC by default).
When the return temperature drops below the value set for the
burner connection the burner will start to operate. The control
of the power is carried out in accordance with the temperatures
of the supply air and return air. The control compares both
temperatures. If the supply temperature is excessively high,
the control limits the power supplied by the burner despite the
demand. This comparison avoids the strati
fi
cation of the hot
air masses and keeps the supply temperature below the safety
value (55ºC by default), which stops the burner.
Moreover, the control compares the supply temperature and the
ambient temperature to improve the feeling of thermal comfort.
The gas burner integrates its own control. “50FC” control only
receives a safety signal from the burner in the event of failure
(digital input DI5). This signal only indicates the failure.
■
Burner control:
The gas burner integrates its own CPU-SMART PCB board
that manages the operation and the safety devices.
The cables “W48-QUE” and “W49-QUE” with the wires
required for the connection of the CPU-SMART PCB board
with the 50FF/FC unit must be connected to the connection
box “BOX8-QUE” that is located inside of the 50FF/FC unit
(please consult the paragraph “Electrical connection of the
burner”.
CPU PCB LCD
Detail of CPU-SMART PCB board
CPU-SMART PCB
burner control
Supply fan
Switch on signal
J13 - NO5
(”50FC” control)
Connector M1
Connector M2
230 - I - 50Hz
47
48
49
40
41
42
43
44
45
W48-QUE
W49-QUE
■
Fxx faults:
The modulation PCB can distinguish between 30 di
ff
erent types
of faults. This ensures accurate diagnostics. Also, codes and
possible causes of faults are listed in this manual.
For more serious faults that require a manual reset, use the
LCD display to reset the CPU PCB on the machine by pressing
the arrows at the same time.
Содержание 50FC Series
Страница 63: ......