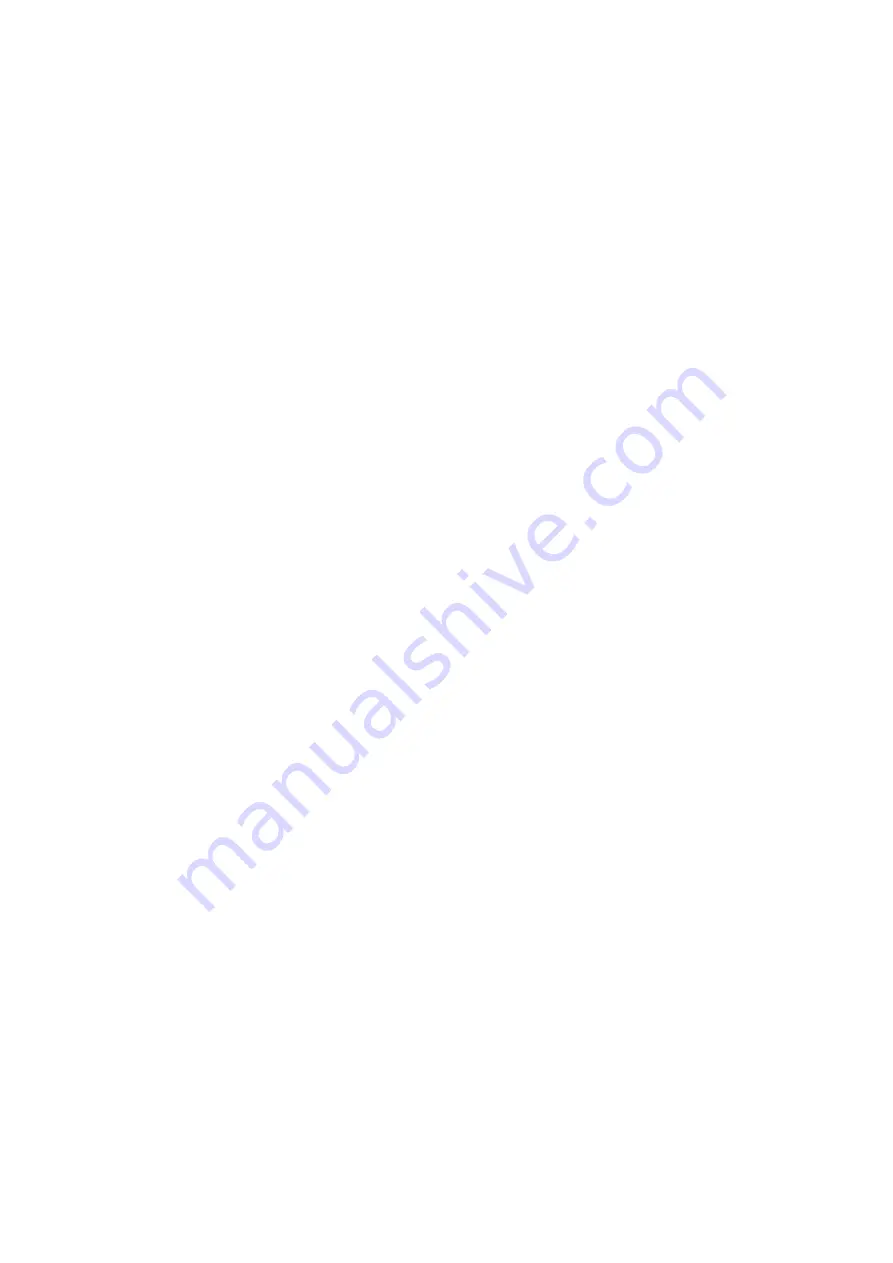
6
During refrigerant removal and storage operations follow
applicable regulations. These regulations, permitting condition-
ing and recovery of halogenated hydrocarbons under opti-
mum quality conditions for the products and optimum safety
conditions for people, property and the environment are
described in standard NFE 29795.
Any refrigerant transfer and recovery operations must be
carried out using a transfer unit. A 3/8” SAE connector on
the manual liquid line valve is supplied with all units for
connection to the transfer station. The units must never be
modified to add refrigerant and oil charging, removal and
purging devices. All these devices are provided with the units.
Please refer to the certified dimensional drawings for the units.
Do not re-use disposable (non-returnable) cylinders or
attempt to refill them. It is dangerous and illegal. When
cylinders are empty, evacuate the remaining gas pressure,
and move the cylinders to a place designated for their
recovery. Do not incinerate.
Do not attempt to remove refrigerant circuit components or
fittings, while the machine is under pressure or while it is
running. Be sure pressure is at 0 kPa before removing
components or opening a circuit.
Any manipulation (opening or closing) of a shut-off valve
must be carried out by a qualified and authorised engineer.
These procedures must be carried out with the unit shut-down.
NOTE: The unit must never be left shut down with the liquid
line valve closed, as liquid refrigerant can be trapped between
this valve and the expansion device. (This valve is situated on
the liquid line before the filter drier box.)
Do not attempt to repair or recondition any safety devices
when corrosion or build-up of foreign material (rust, dirt,
scale, etc.) is found within the valve body or mechanism. If
necessary, replace the device. Do not install safety valves in
series or backwards.
CAUTION: Do not step on refrigerant lines. The lines can
break under the weight and release refrigerant, causing
personal injury.
No part of the unit must use feet, racks or supports during
operation. Periodically monitor and repair or if necessary
replace any component or piping that shows signs of damage.
Do not climb on a machine. Use a platform, or staging to
work at higher levels.
Use mechanical lifting equipment (crane, hoist, etc.) to lift or
move heavy components such as compressors or plate heat
exchangers. For lighter components, use lifting equipment
when there is a risk of slipping or losing your balance.
Use only original replacement parts for any repair or compo-
nent replacement. Consult the list of replacement parts that
corresponds to the specification of the original equipment.
Do not drain water circuits containing industrial brines,
without informing the technical service department at the
installation site or a competent body first.
Close the entering and leaving water shutoff valves and
purge the unit hydronic circuit, before working on the
components installed on the circuit (screen filter, pump, water
flow switch, etc.).
Periodically inspect all valves, fittings and pipes of the
refrigerant and hydronic circuits to ensure that they do not
show any corrosion or any signs of leaks.