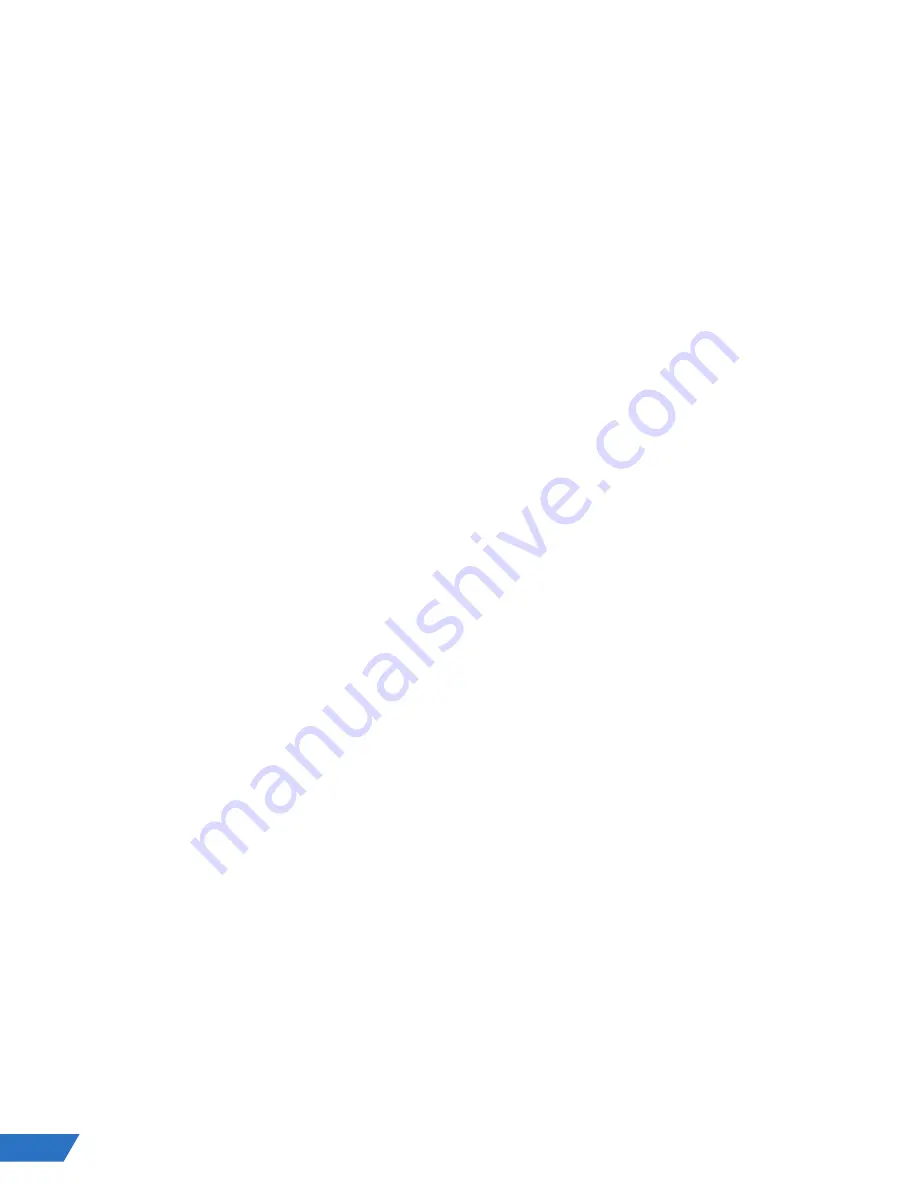
4
TyrFil Flushless Pump
| Flatproofi ng Technical Manual
INTRODUCTION
Flatproofed tires must be processed correctly to provide the customer with the maximum benefi ts of no fl at
tires: full tire life, consistent internal pressure, no rim slippage, improved safety, proper tire fl ex, cost savings
and retreadability.
The tire fl atproofi ng process includes the following steps:
• Inspecting tires and wheels for defects
• Pre-stretching the tire overnight
• Pumping material through the valve stem into the tire replacing all of the air
• Pressurizing the tire to the recommended infl ation pressure
• Curing at the proper time and temperature to ensure optimum fi lled tire performance
It is a precision process and should only be performed by a Carlisle TyrFil Certifi ed Technician. Proper training
and this Manual provide the necessary information to fl atproof tires. This Manual is intended for use with
the TyrFil
™
Flushless Pumping System. As always, we remain available to assist you with all aspects of your
fl atproofi ng business. For any questions or problems, please call our
Sales and Technical Center at (800)
821-4147.
Disclaimer
This Carlisle TyrFil Flatproofi ng Technical Manual contains information pertaining to fl atproofi ng tires with our
manufactured products that have been installed through the Carlisle TyrFil approved processing systems.
This Manual contains information regarding the fl atproofi ng process only, it does not contain other information
which may be relevant with respect to the fl atproofi ng process (for example, the tire manufacturer’s
specifi cations and information, workplace safety information, etc.). It is important that all fl atproofi ng
processors follow not only the safety procedures set forth in this Manual, but also standard safe operation
and work conditions, and other safety procedures that may pertain to the facility in which the fl atproofi ng is
taking place, and the specifi c tire manufacturer’s safety information.
Although this Manual has been developed for the purpose of instruction, the fl atproofi ng processor must
be properly trained in all phases of the job performance, which include, without limitation, installing TyrFil
products into the tire in a safe manner, the proper use and operation of the equipment and the proper
maintenance of such equipment.
Carlisle TyrFil shall not be responsible for any injury or damage to persons or property in connection with the
processing or use of our products. Further, Carlisle TyrFil shall not be responsible for any injury or damage
to persons or property due to a customer’s actions, the customer’s disregard for the safety procedures set
forth in this Manual or other safety procedures, the customer’s failure to comply with the tire manufacturer’s
product guidelines, or due to a customer’s failure to follow our instructions, verbal or written, pertaining to the
fl atproofi ng process.
Carlisle TyrFil’s technical and sales staff make routine visits to its customer’s locations for the purpose
of reviewing processing rooms and procedures. However, a customer should not rely on such visits as
assurance that it has taken all safety and other precautions.
Carlisle TyrFil maintains a knowledgeable technical support staff who can assist our customers with any
questions or troubleshooting that may be needed in connection with our products. Further, Carlisle TyrFil
maintains an inventory of parts, and written technical and safety data on its products.
Any questions regarding information contained in this Manual, our products, or our recommended equipment
should be directed to the Carlisle TyrFil Sales and Technical Center at (800) 821-4147.
Содержание TyrFil
Страница 26: ...NOTES...
Страница 27: ...NOTES...