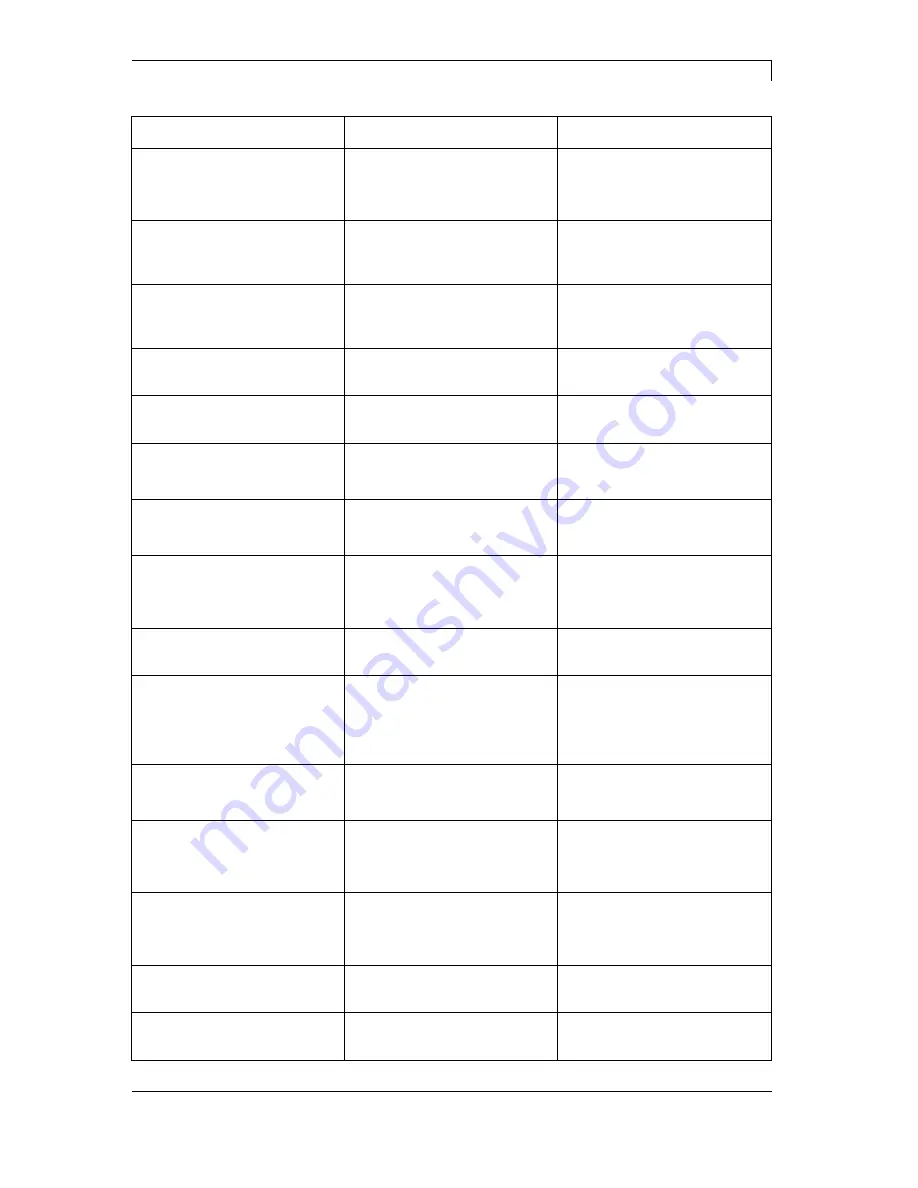
Spectra II
Error correction
09.16
Serviceanleitung
59
Error message
Cause
Remedy
95
Scanner layout
difference
Scanner data does not
correspond to bar code data.
Check adjustment of scanner.
Check scanner settings /
connection.
96
COM break
Serial interface error.
Check settings for serial data
transmission as well as cable
(printer-PC).
97
COM general
Serial interface error.
Check settings for serial data
transmission as well as cable
(printer-PC).
98
No software
printhead FPGA
No printhead-FPGA data
available.
Please contact your
responsible distributor.
99
Load software
printhead FPGA
Error when programming
printhead-FPGA.
Please contact your
responsible distributor.
100
Upper position
Sensor signal up is missing
(option APL 100).
Check input signals /
compressed-air supply.
101
Lower position
Sensor signal down is missing
(option APL 100).
Check input signals /
compressed-air supply.
102
Vacuum plate empty
Sensor does not recognise a
label at vacuum plate
(option APL 100).
Check input signals /
compressed-air supply.
103
Start signal
Print order is active but device
not ready to process it.
Check start signal.
104
No print data
Print data outside the defined
label.
Selection of wrong module type
(design software).
Check selected module type.
Check selection of left/right
version.
105
Printhead
No original printhead is used.
Check the used printhead.
Contact your distributor.
106
Invalid Tag type
Wrong Tag type.
Tad data do not match the Tag
type in the printer.
Adapt data or use the correct
Tag type.
107
RFID invalid
RFID module is not activated.
No RFID data can be
processed.
Activate RFID module or
remove RFID data from label
data.
108
GS1-128 invalid
Transferred GS1-128 bar code
is invalid.
Verify bar code data (see GS1-
128 bar code specification).
109
EPC parameter
Error at EPC calculation.
Verify data (see EPC
specification).
Содержание Spectra II
Страница 1: ......
Страница 12: ......
Страница 18: ......
Страница 46: ......
Страница 52: ......
Страница 62: ......
Страница 68: ......
Страница 69: ...Spectra II Wiring Plan 09 16 Service Instructions 67 10 Wiring Plan Figure 36 ...
Страница 70: ...Wiring Plan Spectra II 68 Service Instructions 09 16 Figure 37 ...
Страница 72: ...Wiring Plan Spectra II 70 Service Instructions 09 16 10 2 Power Electronics Figure 39 ...
Страница 76: ......