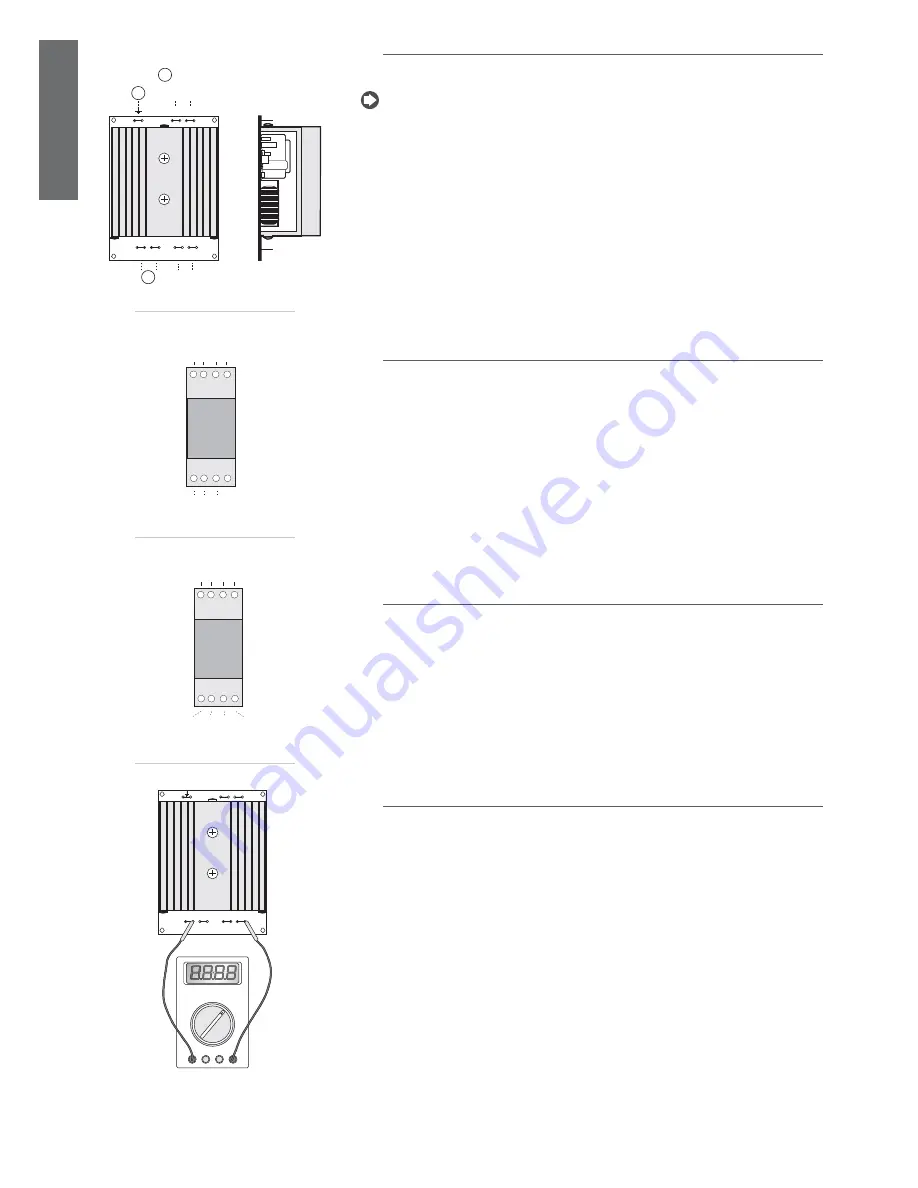
64
LOAD
LINE
220 Vac
GND
-
+
Y
1
2
3
24 Vac
No Com Nc
Y GND
1 2 3 4
5 6 7 8
24 Vac
G0
G0
0-10V
4-20mA
Y GND
1 2 3 4
5 6 7 8
LOAD
N
L
-
+
LINE
N
L
Vac?
ENGLISH
μC
2
SE - +030220426 - rel. 2.1 - 09.06.2010
7.4 Fan speed control board (code MCHRTF*)
The phase cutting boards (code MCHRTF****) are used to control the speed of the condenser
fans.
IMPORTANT:
The power supply to the μC
2
SE (G and G0) and the MCHRTF**** board must be in
phase. If, for example, the power supply to the μC
2
SE system is three-phase, make sure that the
primary of the transformer supplying the μC
2
SE board is connected to the same phase that
is connected to terminals N and L on the speed control board; therefore, do not use
380 Vac/24 Vac transformers to supply the controller if the phase and neutral are used to directly
power the speed control boards.
Connect the earth terminal (where envisaged) to the earth in the electrical panel.
Key:
1. to
μchiller;
2. earth;
3. to
motor.
7.5 Fan ON/OFF control board (code CONVONOFF0)
The relay boards (code CONVONOFF0) are used for the ON/OFF management of the condenser
fans.
The control relay has a switchable power rating of 10 A at 250 Vac in AC1 (1/3 HP inductive).
7.6 PWM to 0 to 10Vdc (or 4 to 20 mA)conversion board for
fans
(code CONV0/10A0)
The CONV0/10A0 boards convert the PWM signal at terminal Y on the μC
2
SE to a standard 0 to 10
Vdc (or 4 to 20 mA) signal. The FCS series three-phase controllers can be connected to the μC
2
SE
without using this module.
7.7 Minimum and maximum fan speed calculation
This procedure should only be performed when the fan speed control boards are sued (code
MCHRTF*).
it must be stressed that if the ON/OFF modules (code CONVONOFF0) or alternatively the PWM
to 0 to 10 V converters (code CONV0/10A0) are used, parameter F03 should be set to zero, and
parameter F04 to the maximum value.
Given the diff erent types of motors existing on the market, the user must be able to set the
voltages supplied by the electronic board corresponding to the minimum and maximum
speeds. In this regard (and if the default values are not suitable), proceed as follows:
• set parameter F02= 3 and set F03 and F04 to zero;
• the condenser control set point (evaporator in HP mode) has been modifi ed to take the output
signal to the maximum value (PWM);
• increase F04 until the fan operates at a suffi
cient speed (make sure that, after having stopped it,
it can rotate freely when released);
• “copy” this value to parameter F03; this sets the voltage for the minimum speed;
• connect a voltmeter (set for AC, 250V) between the two “L” terminals (the two external
contacts);
• increase F04 until the voltage stabilises at around 2 Vac (inductive motors) or 1.6, 1.7 Vac
(capacitive motors). Once the value has been found, it will be evident that even when
increasing F04 the voltage no longer decreases. In any case do not increase F04 further so as to
avoid damaging the motor;
• restore the correct condenser set point (evaporator in HP mode).
The operation is now completed.
Fig. 7.d
Fig. 7.e
to μchiller
Fig. 7.f
to μchiller
Fig. 7.g
Содержание uC2SE
Страница 1: ...C2 SE electronic control User manual...
Страница 2: ......
Страница 4: ...4 E N G L I S H C2 SE 030220426 rel 2 1 09 06 2010...
Страница 6: ...6 E N G L I S H C2 SE 030220426 rel 2 1 09 06 2010...
Страница 72: ...72 E N G L I S H C2 SE 030220426 rel 2 1 09 06 2010...
Страница 73: ...73 E N G L I S H C2 SE 030220426 rel 2 1 09 06 2010...
Страница 74: ...74 E N G L I S H C2 SE 030220426 rel 2 1 09 06 2010...
Страница 75: ......