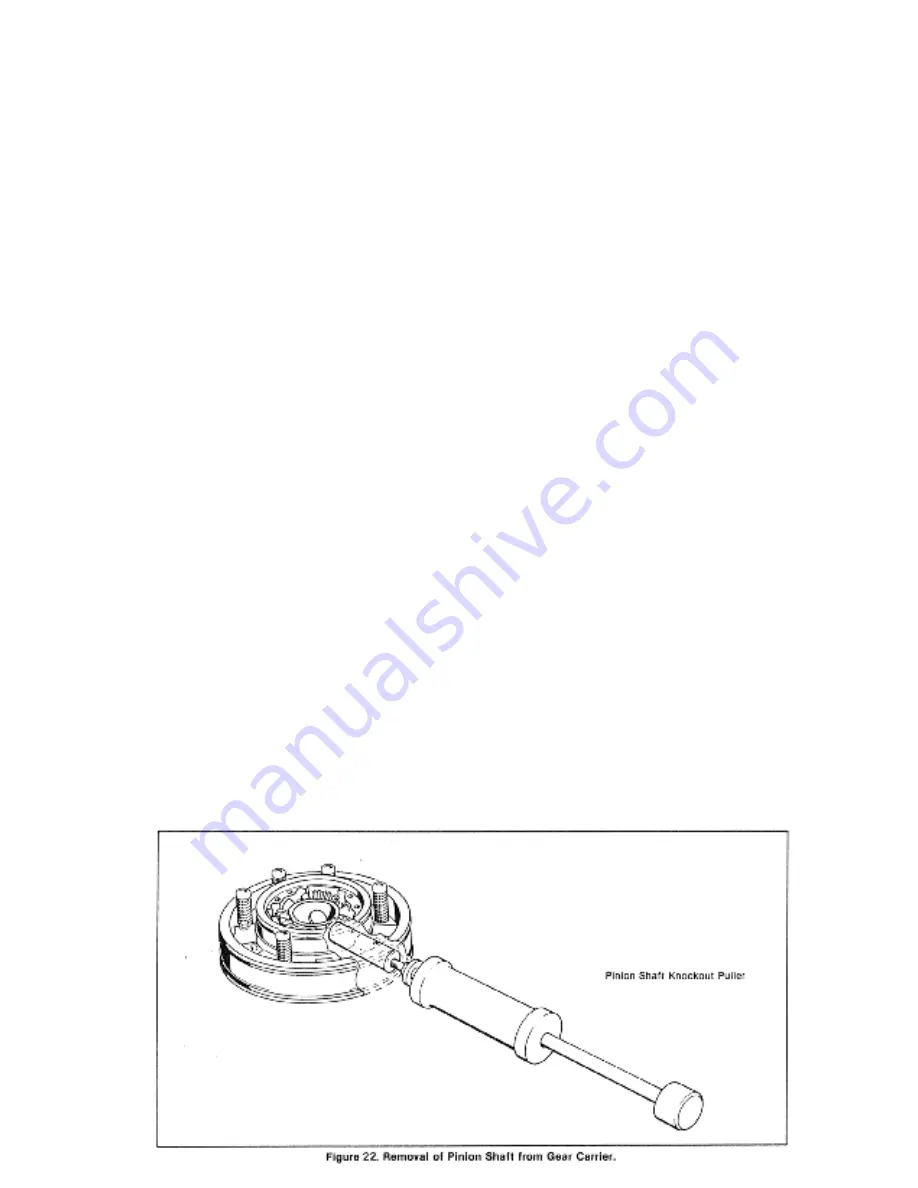
30
7.3 CLUTCH
A) DISASSEMBLY
NOTE: FOR REMOVAL
INSTRUCTIONS SEE PAGE 22.
1. Remove socket head, capscrews, lock
washers, (and Allen nuts) securing both
clutch flanges to bevel gear carrier.
2. Lift off clutch flanges and clutch discs
3. Press and remove bearing and driving
gear from both forward and reverse
clutch flanges.
4. Remove locknuts, clutch identification
tag and capscrews from outer perimeter
of cylinders.
5. Separate and remove cylinder
6. Remove and discard quad rings from
bevel gear carrier.
7. Remove capscrews and locknuts
securing pinion shafts in bevel gear
carrier and remove bevel pinion shaft
with puller (See special tool No. 1-
90008-0000, pinion shaft knockout
puller). Refer to fig.22
B) CLEANING AND INSPECTION
1. Inspect bevel pinions for wear,
chips, and breaks or out of round
condition. If there is any damage
we recommend replacing all of
them as a set.
2. Check all pinion bearings and
washers for distortion or rough
operation. If one bearing needs
replacement we recommend
replacing all of them as a set.
3. Clean all parts with a good grade
cleaning solvent or diesel fuel. Blow
dry with compressed air.
4. Inspect all oil passages in bevel
gear carrier to see that they are free
from obstruction.
5. Inspect bevel gear carrier for
cracks, chips or worn mounting
surfaces. Pay special attention to
seal ring grooves. Discard carrier if
damaged.
6. Inspect forward commutator
bushing for chips, heat scores,
scratches, distortion or wear (See
Wear limits, p. 23). Repair or
replace as necessary.
7. Inspect all hardware and springs for
wear or distortion. Repair or replace
as necessary.
8. Remove clutch discs from flanges
and inspect discs for broken teeth,
heat scores or wear (See Wear
Limits, page 23). Replace as
necessary.
9. Inspect driving gear, and driven
gear, for wear, chips or cracks. If
either one is damaged we
recommend replacing both as a set.
Содержание HY- 6900
Страница 1: ...1 HY 6900 HY 7700 SERVICE MANUAL ...
Страница 5: ...5 ...
Страница 6: ...6 ...
Страница 16: ...16 ...
Страница 30: ...29 ...
Страница 47: ...46 46 ...
Страница 49: ...48 48 1 5 CLUTCH Clutch no 1 00100 6000 ...
Страница 51: ...50 50 ...
Страница 54: ...53 53 8 8 PINION SHAFT AND RELATED PARTS 8 9 IDLER GEAR AND RELATED PARTS ...
Страница 56: ...55 55 ...
Страница 62: ...61 61 ...
Страница 63: ...62 62 8 16 HY 6900 ...
Страница 65: ...64 64 8 17 PINION SHAFT AND RELATED PARTS HY 6900 ...
Страница 67: ...66 66 HY 6900 ...
Страница 70: ...69 69 ...
Страница 71: ...70 70 ...