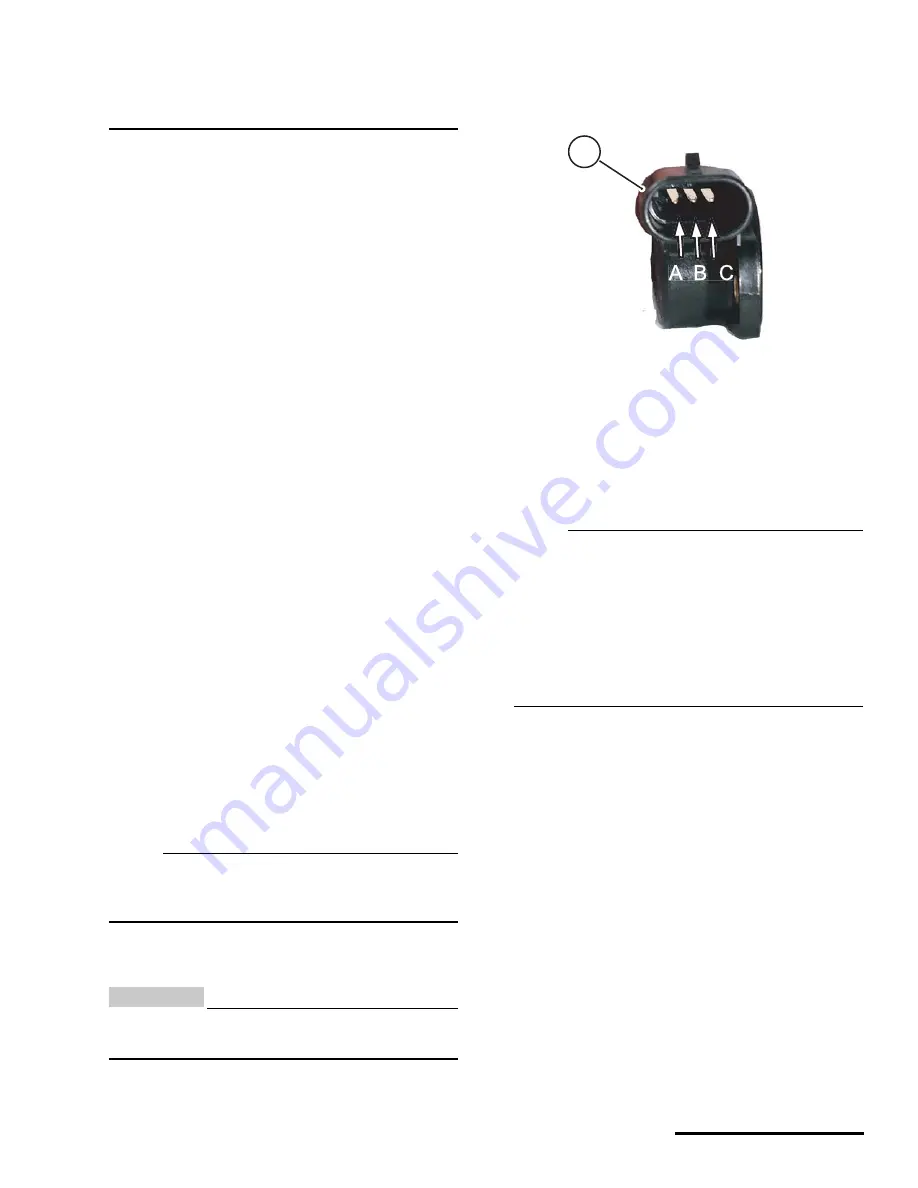
11
8/14/02
11
required on a “perfect” throttle body to match the
air flow of the vehicle's throttle body at the closed
position. Typical values are from 0.0 to 1.0%"
starting on page 37.
The TPS sensor signal informs the ECU of not only
the relative position of the throttle plate, but also the
speed with which it is being opened or closed. The
engine load is determined by the TPS and engine
speed (rpm). The voltage output from the TPS
increases proportionately as the throttle is opened.
The sensor contains no user serviceable items.
Dynamic Test - ECU Monitor
1. Use the ECU Monitor windows of the Cannondale
Diagnostic and Maintenance Tool and read the
Throttle position (%) field. This field is the percent
the throttle plate is open as translated by the
ECU. With the throttle plate completely closed,
this value should read between 2% to 3%. When
the throttle is fully opened, a normal reading is
97% to 100%. When the idle adjustment is set,
this value should be approximately 3% higher
than the completely closed percent to achieve
rough idle. Fine tuning of the idle adjustment
screw which changes the% percent may be
required
If the Throttle Position (%) field values in the ECU
monitor window are erratic or inconsistent as
described above, the sensor can be tested further
by removing it and reading the resistance values
with an Ohmmeter.
2. Attach a vacuum pump/pressure pump to the
hose end and monitor change. The reading
should increase when increased pressure is
applied. The reading should decrease when vac-
uum is applied.
NOTE :
Be sure to convert the atmospheric pressure units
displayed in the ECU monitor window with units
displayed with the tools.
CAUTION
:
Use of high pressure or vacuum when testing
may damage the sensor diaphragm.
Static Test - Resistance
1. To test the sensor resistance, remove the sensor
harness connector, remove the mounting bolts,
and remove the sensor from the throttle body.
NOTE :
Removing the sensor from the throttle plate shaft
to measure the resistance is not required.
Removing it and inspecting the housing and shaft
socket for damage can be helpful. Remember that
is the sensor is removed, you will have to reset the
sensor min and max values using the software
tool. Refer to "Setting the throttle position sensor
minimum and maximum values" starting on
page 34.
2. Measure resistance across sensor terminals A
and B.
The resistance should be 1200 ± 240 Ohms.
3. Measure the resistance across sensor terminals
A and C.
- slowly rotate the sensor wheel clockwise and
observe variable resistance. Resistance should
increase smoothly from 0 to 1200 ± 240 Ohms.
1. TPS sensor (shown removed)
1