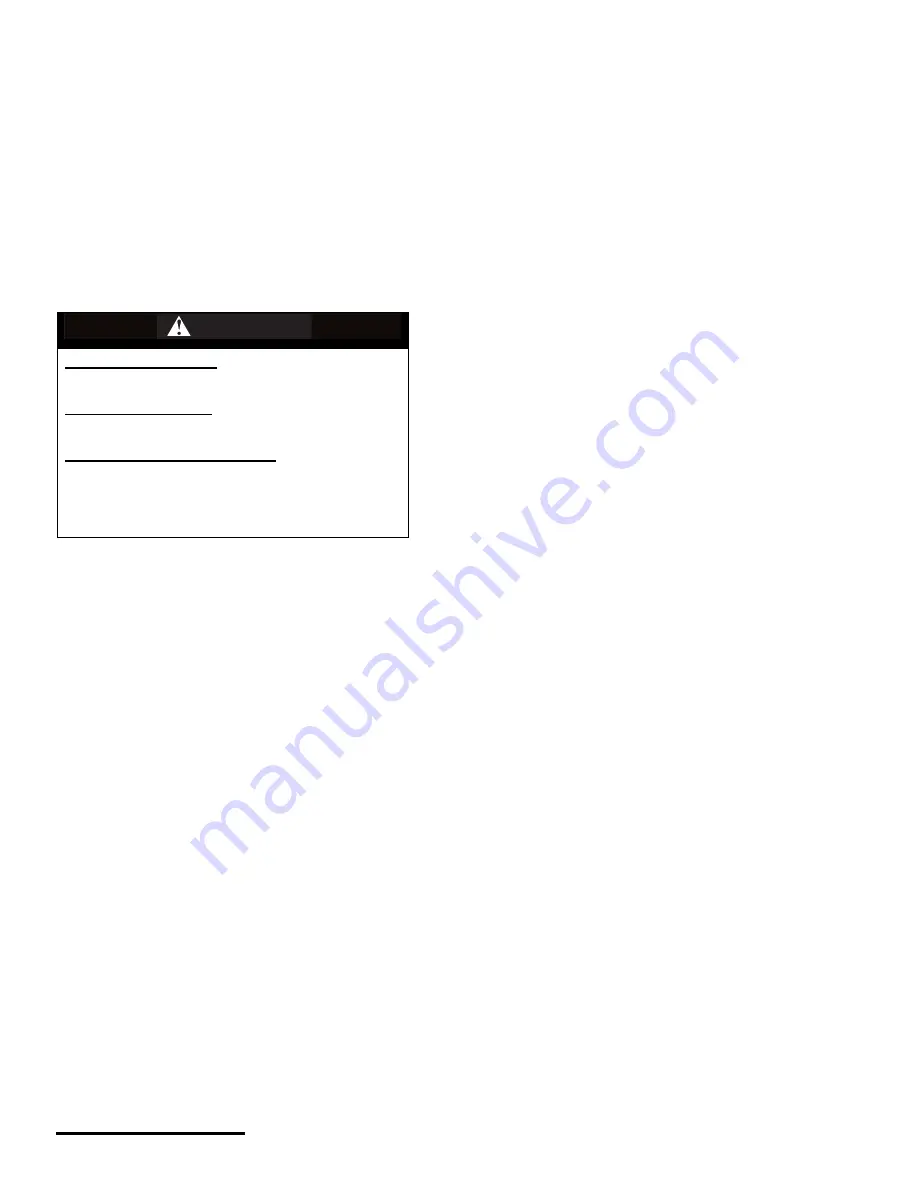
© 2001 Cannondale Corporation - All Rights Reserved
56
X440s Owner's Manual.fm
ELECTRICAL
SYSTEM SERVICING
Many electrical problems are caused by faulty electrical
connectors or couplers. For example, wet terminals/pins,
dirty or corroded terminals/pins, or broken or bent cable pins
within multi-plug couplers.
CONNECTORS AND COUPLERS
Within this manual “connectors” refer to a single male lead
that connects into a single female lead.
Couplers contain multi-pins and usually have some sort of
locking device (e.g., barb, hook, eye) which must be
released before the two halves can be separated. Both
couplers and connectors will be referred to as quick-
connects.
Refer to the following tips when disconnecting or connecting
electrical connectors or couplers.
1.
When disconnecting a connector, be sure to hold the
coupler/connectors; do not pull the leads.
2. Always check for a locking device which must be
released before the coupler can be separated. Also,
be sure to hold both halves of the coupler; do not pull
the leads.
3. Inspect couplers for bent terminals/pins, damaged
cable terminal/pin joints, water, dirt, or corrosion, and
secure wiring. If a terminal or pin is bent, carefully
straighten it with a thin-blade screwdriver.
4. When connecting a connector or coupler, make sure
there is no dirt present. Be sure to push the male and
female ends together squarely to ensure that the
terminals/pins do not get bent or incorrectly located.
And most importantly, make sure the two halves
connect positively.
5. Whenever a connector or coupler is disconnected or
checked, be sure to clean it and apply some dielectric
grease before reconnecting.
CLEANING CONNECTORS
Wipe the connector or coupler with a clean, lint-free rag and
blow off any moisture using compressed air. Remove
corrosion, rust, stains or other foreign material using contact
cleaner on terminals and a water-displacement chemical on
connector seals. Apply a light coat of dielectric grease onto
the terminals/pins and properly connect the halves.
ENGINE MANAGEMENT SYSTEM
All Cannondale models use advanced fuel injection
systems. Engine operation is supported by an Engine
Management System (EMS) which controls both ignition
and fuel delivery.
The engine management system consists of three types of
electrical components: an Engine Control Module (ECM),
sensors, and actuators.
•
The engine control module (ECM or ECU) precisely
calculates ignition timing and fueling delivery for all
engine speeds and loads (based on the currently
installed ECM mapping). The ECM is an extremely
reliable component and should be the last
component checked in the event there is a problem
with the fuel injection system.
•
Sensors collect engine operating information and
transmit it to the ECU.
•
Actuators are devices like the fuel injectors, fuel
pump, fuel pressure regulator, spark plug coil, and
relays.
IGNITION TIMING
Ignition timing is continuously changed based on rpm and
engine load conditons determined by the ECM and the
installed map(s). The ignition system is a constant energy
type ignition with 12 V primary and approximately 10,000-
20,000 V secondary.
•
Igntion timing is controlled by the ECM and is not
user adjustable.
•
Ignition dwell time is controlled by the ECM and is
not user adjustable.
Timing is accomplished by the crankshaft position sensor
which is located in the generator housing. The wide tooth/
wide space pattern on the flywheel passes under the sensor
near bottom dead center (BDC).
WARNING
POTENTIAL HAZARD
Damaged electrical system.
WHAT CAN HAPPEN
A damaged electrical system can cause a fire.
HOW TO AVOID THE HAZARD
Always disconnect the battery when working on an
electrical part on the vehicle. When reconnecting
the battery ALWAYS connect the positive (+) lead
first.