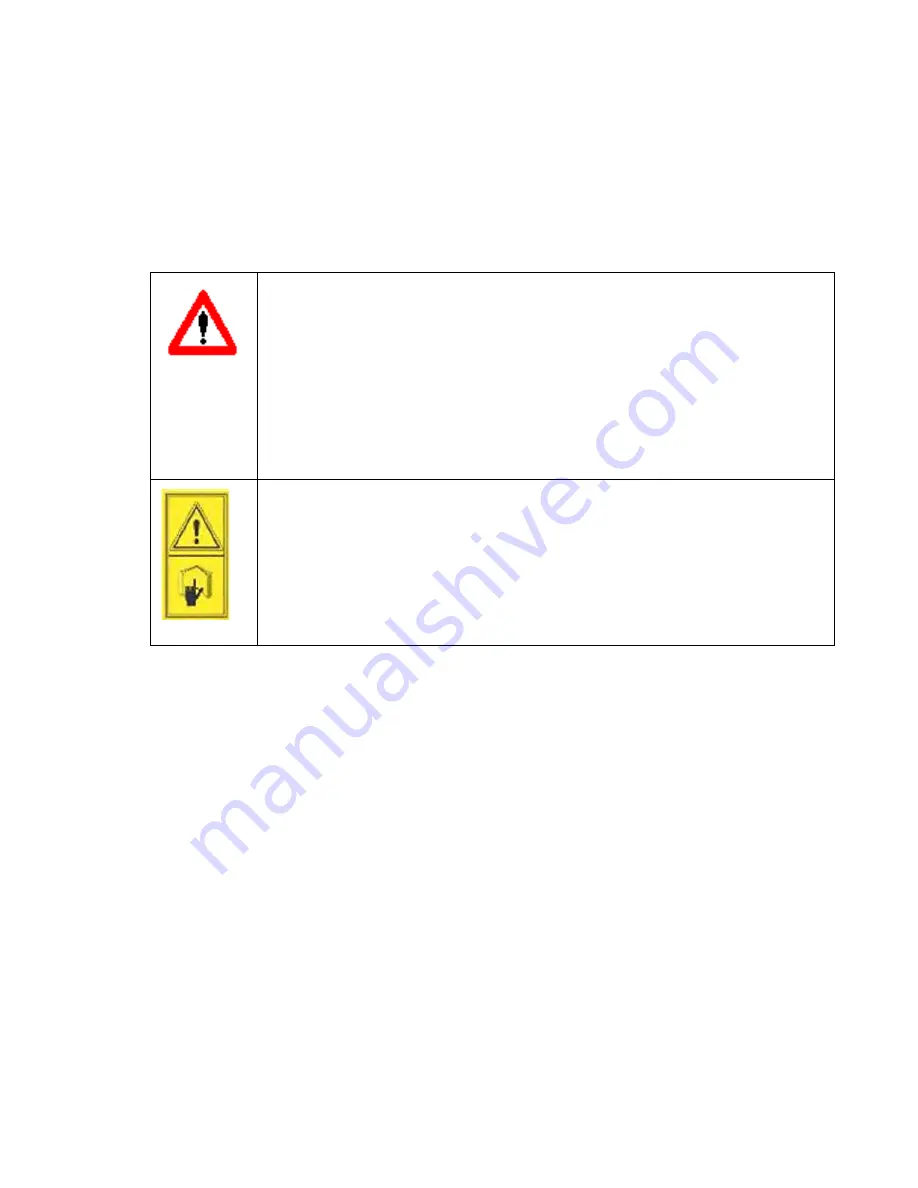
CPB-515 Operation and Maintenance Manual – TTS 70, 80,100, 110 Series (10-2021)
14
4.
Remove the tire and rim assemblies.
5.
Remove the axle and hub assemblies from the implement frame (as required).
6.
Install track fitment axle. For two axle midroller track systems, make sure the
stabilizer brackets on the axle are facing to the front of the implement. Tighten
mounting hardware.
WARNING
Danger of crushing. Use suitable lifting devices (capacity at least
9000 lbs (4100Kg)), wear safety equipment and observe the safety
rules.
If using a fork lift use, for handling operations, be careful not to
damage the rubber track. Metal chains or cables are not
recommended.
IMPORTANT
Should a motorized lifting device be used, assistance on ground
during operation of handling, coupling and assembly is needed.
Do not stand between lifting device and axle assembly when
mounting axles to implement. Be careful: risk of injury.