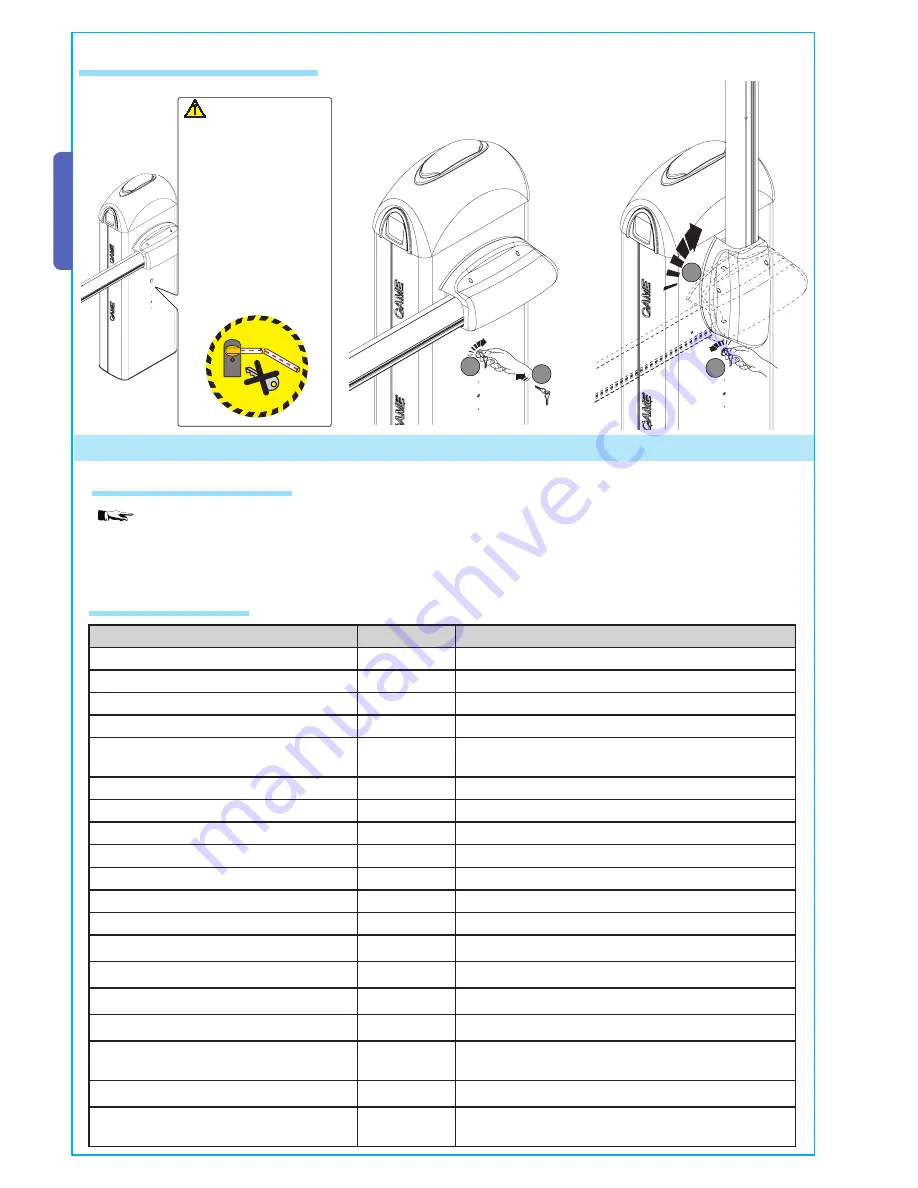
14
T
h
e d
at
a a
n
d i
n
fo
rm
at
io
n p
rovi
d
ed
i
n
t
h
is
m
an
u
al
a
re to b
e c
o
n
si
d
er
ed
s
u
sc
ep
ti
b
le to c
h
an
g
e a
t a
n
y t
im
e w
it
h
o
u
t w
ar
n
in
g
, by CAM
E c
an
ce
ll
i a
u
to
m
at
ic
i S
.p
.A
.
ENGLISH
WARNING! The release
procedure may constitute a
hazard for the user when,
for whatever reason – the
bar is fixed improperly to
the housing during assem-
bly, or the bar is cracked or
broken in an accident, and
so on – the tension springs
no longer provide balance!
These can thus cause a
brusque rotation of the bar
attachment and/or of the
bar itself.
5.9 Manual release of the barrier
MALFUNCTIONS
REFERENCES
CHECKS
The unit neither opens nor shuts
1-2-3-4-6-8-20 1 - Chiudere sportello d’ispezione con la chiave
The unit opens but does not close
4-7-10
2 - Disable “steady movement” with dipswitch
The unit shuts but does not open
7-9
3 – Check power supply and fuses
No automatic closure
11-12-13
4 - N.C. safety contacts open (1-2 / 2-C1)
The unit does not work if the remote control
is used
2-14-16
6 - Disable master-slave function
The unit inverts direction
7
7 – Check spring tension and balancing
The unit works only with remote control
22
8 – Disable obstacle detection with dipswitch
The photoelectric cell does not react
12-23-24
9 – Check if end stop opens
The signalling LED indicator flashes rapidly
4
10 – Check if end stop closes
The signalling LED indicator remains on
13
11 - Activate “automatic closure” dip switch
The unit does not end its run
7
12 – Check the correct direction of movement
The bar is not properly balanced
7-15
13 - (2-3 / 2-4 / 2-7) command button
14 -Check jumper on AF43S, turn on/off power
15 – Check the bar length ratio with mountable accessories
16 – Re-save radio code
20 - Raise the motor torque
22 - Enter or duplicate the same code in all the remote
controls
23 - Activate the photoelectric cell with the dipswitch
24 - Connect the photoelectric cells in a series, not in
parallel
6.1 Periodic maintenance
The unit does not require specifi c maintenance. Only as a precautionary measure and in case of intensive use, we re-
commend periodic checks (every 6 months) on the state of the electric wire connected to the motor, the spring-bar balance, the
tightness of the nuts and the proper oiling of the sliding points between fi xed and mobile parts.
All checks must be recorded (in a dedicated record-book).
6 Maintenance
6.2 Problem solving
- Manually raise the bar
and block it again by
turning the key counter-
clockwise.
- Insert the key into the lock and
turn it clockwise.