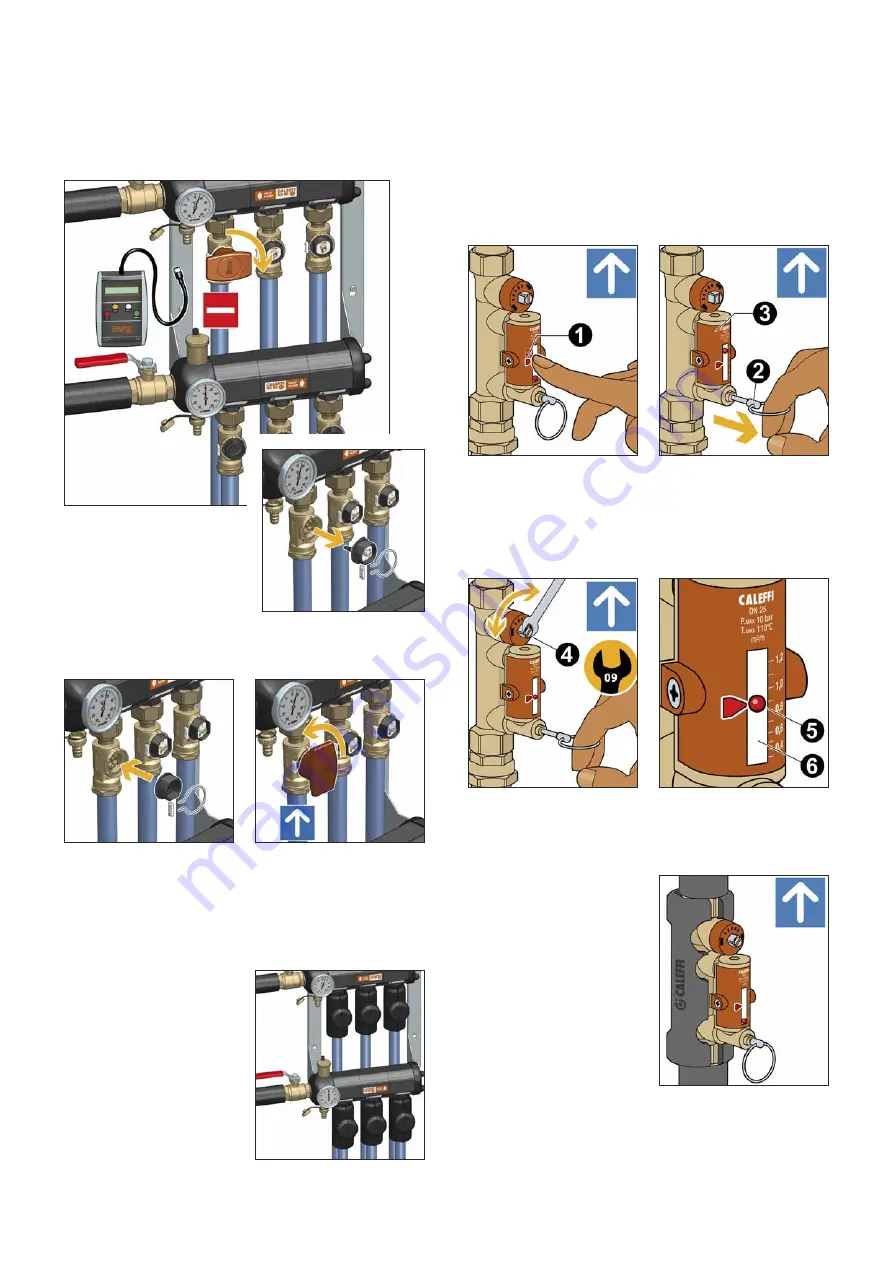
4)
After completing the balancing, release the ring (2) of the flow
meter obturator which, thanks to an internal spring, will
automatically go back
̀
into the closed position.
5)
After balancing the system
insert
the
insulation
and
ensure that it is correctly
closed.
13
Balancing valve – 112 series
Flow rate regulation is carried out as follows:
3)
Keeping the obturator open, use a 9 mm fixed hex spanner on
the valve’s control stem (4) to regulate the flow rate. The flow
rate is indicated by a metal ball (5) running inside a transparent
guide (6) along
̀
a graduated scale in m
3
/min.
1)
With the aid of the indicator
(1), mark the reference flow
rate on which the
̀
valve is to
be set.
2)
Use the ring (2) to open the
obturator that shuts off the
flow of medium in the flow
meter
(3)
under
normal
operating conditions.
After balancing, disconnect the electronic meter and put the
shut-off valves back into their standard operating condition as
follows:
10)
Close the valve using the specific knob and take out the sensor
by removing the ring stop and the seal ring.
Repeat the operations for all the circuits.
The sensors, the electronic meter and the control lever are only
used for start-up. The installer requires a single kit to operate all
systems of this type: this notably reduces costs and prevents
needless system head loss caused by the presence of an obstacle
in the flow.
11)
Fit the cap back in and
secure it with the seal ring
and the stop.
12)
Reopen the valve with the
knob.
13)
After balancing the system
insert
the
insulation
and
ensure that it is correctly
closed.