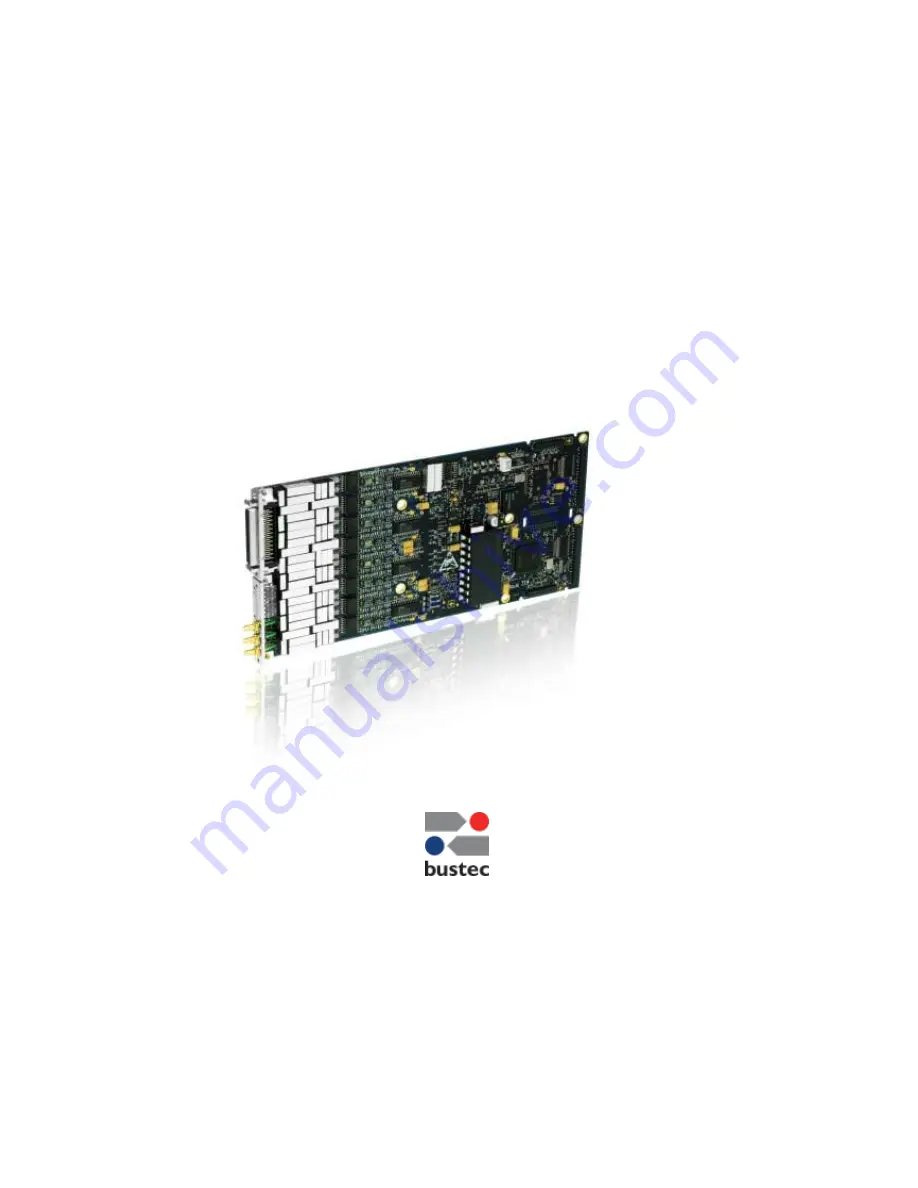
USER MANUAL
ProDAQ Data Acquisition Function Cards
ProDAQ 3424 8-Channel, 24-Bit,
Sigma-Delta ADC Function Card
PUBLICATION NUMBER: 3424-XX-UM-0010
Copyright, © 2014, Bustec Production, Ltd.
Bustec Production, Ltd.
Bustec House, Shannon Business Park, Shannon, Co. Clare, Ireland
Tel: +353 (0) 61 707100, FAX: +353 (0) 61 707106