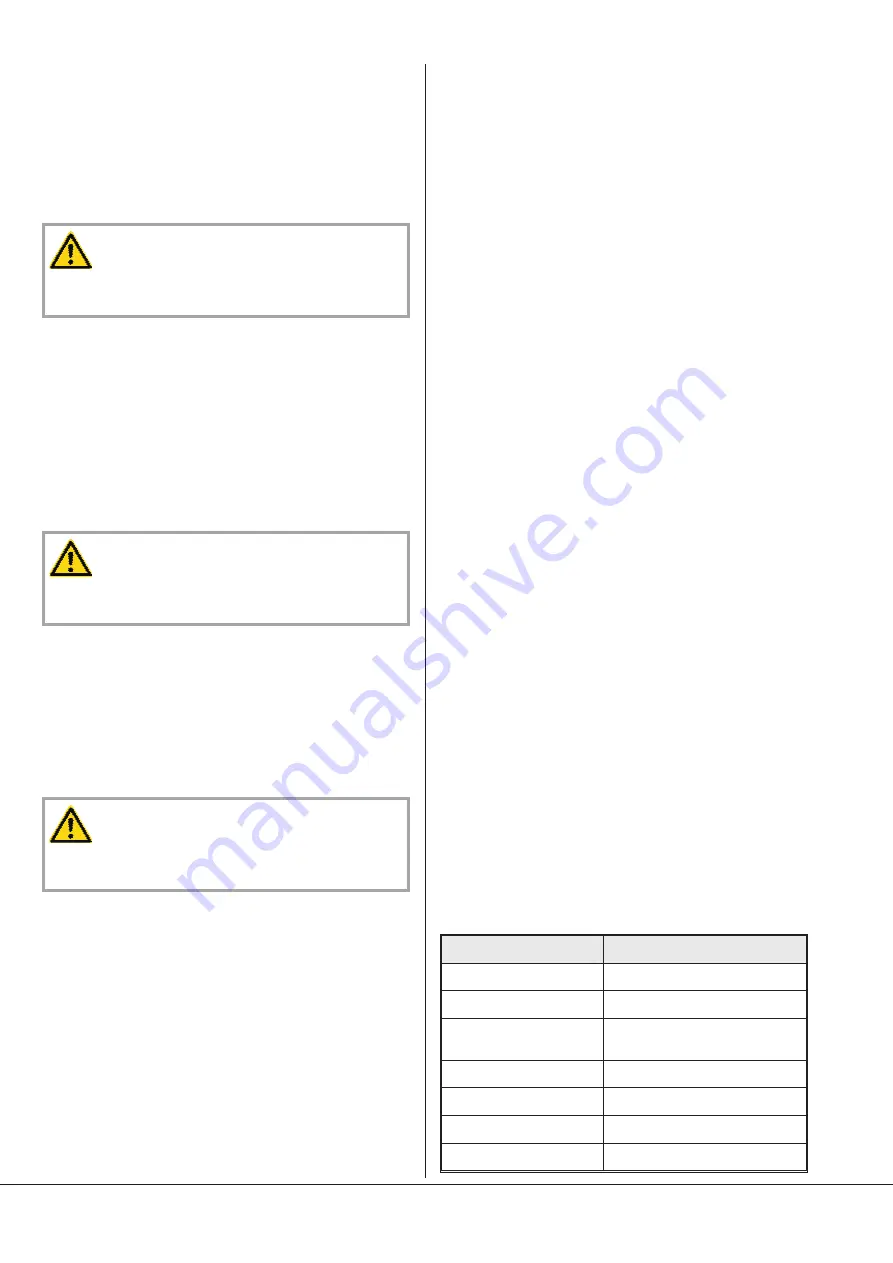
In case the inlet gases can contain dust or other foreign solid particles:
u
Make sure that a suitable filter or protection screen is installed
at the inlet of the vacuum pump
l
Make sure that the nominal diameter of the inlet line is at least
equal to the diameter of the inlet flange to prevent a drop in the
performance of the vacuum pump in the case of a smaller
cross-section.
l
Make sure that the vacuum pump is connected with leak proof
lines.
CAUTION
Once the inlet line has been connected up, make sure that the sys-
tem does not leak. Leakage of dangerous substances must be pre-
vented!
l
Make sure that the inlet line is equipped with a shut-off device
upstream of the inlet flange, so that the flow of drawn gases can
be stopped
l
Make sure that the inlet line does not exercise any pressure on the
inlet flange. Use bellows if necessary.
l
The inlet flange has the following dimension:
–
DN 100 PN 16 or ASME B16.5 4"150 16S
In case of long inlet lines the pipe diameter should be larger than the
inlet flange to prevent a drop in the performance of the vacuum pump.
If you have any doubts, contact your Busch representative.
Discharge connection
CAUTION
Do not put hands into the outlet aperture.
Risk of body damage!
The following instructions for connection to the discharge side only
apply if the drawn gas is discharged into a suitable environment by the
vacuum pump.
l
Make sure that the protection, that was fitted to prevent the in-
gress of particles during transport, has been removed before the
vacuum pump is connected up to the vacuum pipe
l
Make sure that the nominal diameter of the discharge line corres-
ponds at least to the diameter of the exhaust flange of the vacuum
pump in order to prevent a drop in the performance of the vacuum
pump, in case of use of a smaller cross-section
CAUTION
When the discharge piping has been connected up, make sure that
the system does not leak. Leakage of dangerous substances must be
prevented!
l
Make sure that the discharge line is fitted in such a way so as to
prevent any liquids or condensates to re-enter the vacuum pump
(siphon, discharge line sloping away from the pump)
l
Make sure that the discharge line is not equipped with a shut-off
l
Make sure that the discharge line does not exercise any pressure
onto the exhaust flange. Mount bellows if necessary
l
The outlet flange has the following dimension:
–
DN 80 PN 16 or ASME B16.5 3" 150 16S
In the case of long discharge lines, the line cross-section should be
larger than the exhaust flange in order to prevent a drop in the
performance of the vacuum pump. If you have any doubts, contact
your Busch representative.
Cooling liquid connections (CL)
The cooling liquid is generally connected up with a flexible hose.
Connection diameter:
–
G 1/2, ISO 228-1
Connection for the injection liquid into the
cylinder (INJ)
The connection for the injection liquid into the cylinder are usually
established using flexible pipes.
Connection diameter:
–
G 1/2, ISO 228-1
Electrical connection/ Checks
l
Make sure that the requirements according to EMC-Directive
2014/30/EU as well as the current EN-standards, electrical and oc-
cupational safety directives and the local or national regulations
respectively, are complied with (this is the responsibility of the de-
signer of the machinery into which the vacuum pump is to be in-
corporated; see also the corresponding comments in the
EU-Declaration of Conformity).
l
Make sure that the power supply is compatible with the data on
the nameplate of the drive motor
l
Make sure that an overload protection according to EN 60204-1 is
provided for the drive motor
l
Only use shielded cables compatible with the Directive on the elec-
tromagnetic Compatibility 2014/30/EU to connect the motor.
l
Make sure that the drive of the vacuum pump will not be affected
by electric or electromagnetic interference; if unsure please seek
advice from your Busch representative
Monitoring the cooling liquid temperature
(TSA+/0101) (option)
The cooling liquid temperature of the ATEX certified AC 1000 F VR
vacuum pump can be monitored by temperature sensor PT100.
The control of the cooling liquid temperature can be necessary in order
to ensure the difference of temperatures between TSA+/0101 and
TSA+/0102 be
£
70°C.
The temperature sensor must be connected in such a way that the
vacuum pump stops when the temperature reaches the prescribed
switch-off temperature value.
Monitoring the outlet gas temperature of the
pump (TSA+/0102)
The outlet gas temperature must be monitored by a temperature
sensor PT100 (TSA+/0102).
The temperature sensor
must
be connected in such a way that the
vacuum pump stops when the gas temperature reaches the prescribed
switch-off temperature value.
Technical data of the standard product TSA+/0101 and
TSA+/0102
Technical data
Temperature sensor PT100
Busch part no.
0651 550 436
Type
TFE/ TWBa-ADX50XG1/4X90DACB
Material of the protection
tube
1.4571
EC Approval type
PTB 01 ATEX 2206 X
Type of protection
Ex ia IIC T1...T6
Connection
G 1/4" (mâle)
Transmitter (option)
0-300°C => 4-20mA
Installation and Commissioning
Page 8
Содержание COBRA AC 1000 F
Страница 26: ...Note...
Страница 27: ...Note...