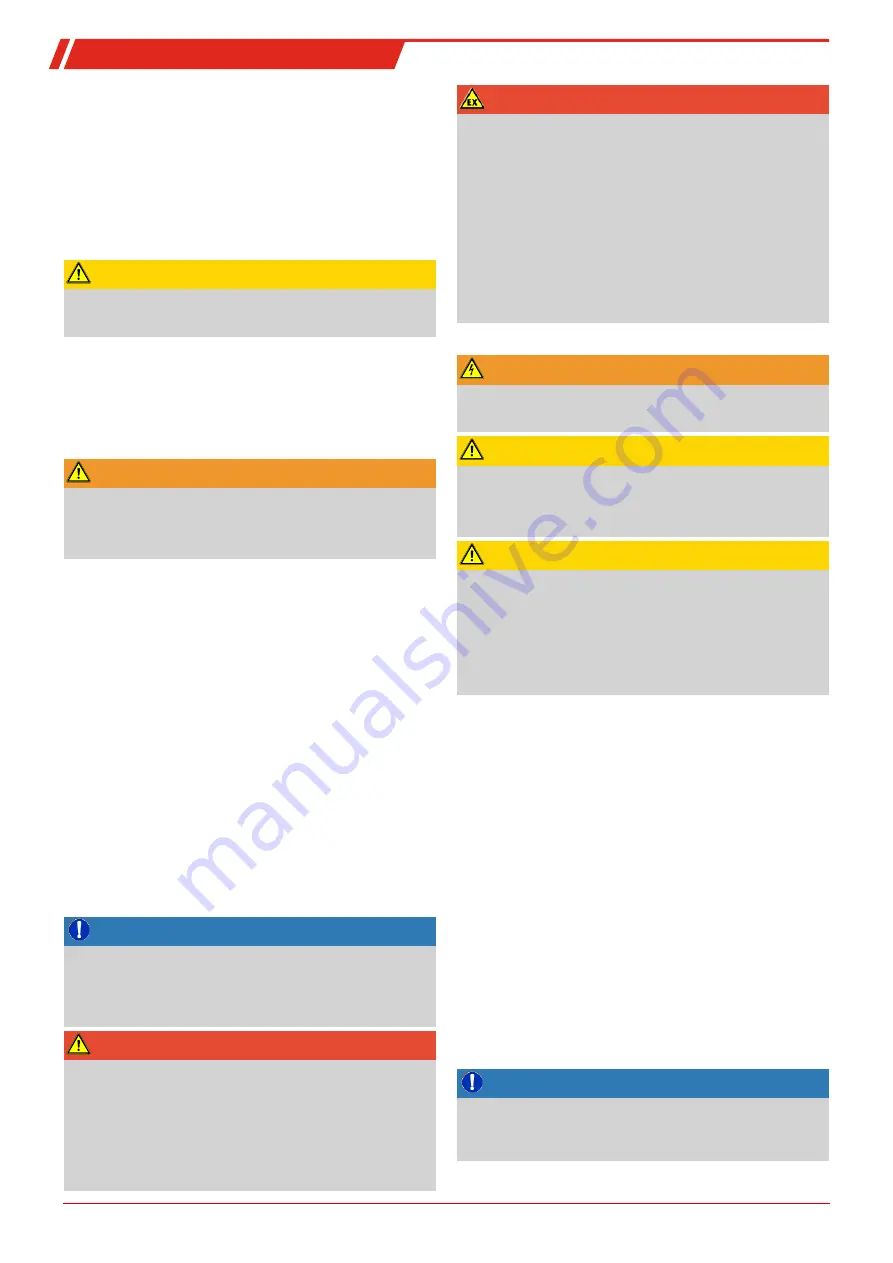
GAS 222.35 AMEX
4.5.2 Connecting the Gas Line
Please note the following items when connecting the sample
gas line (NPT 1/4") on heated probes to prevent thermal
bridges:
• Choose the shortest possible screw connection.
• Shorten the connection pipe for the sample gas line as
much as possible. To do so, remove the insulation around
the sample gas line. This is done by loosening the fixing
bolts.
CAUTION
Fragile
The insulation is fragile. Handle with care, do not drop.
After connecting the sample gas line it must be braced and se-
cured with the clamp.
Long sample gas lines may require additional support clamps
along the way to the analysis system! Once all lines have been
connected and checked for leaks, carefully reinstall and secure
the insulation.
WARNING
Gas emanation
Sample gas can be harmful to the health!
Check the lines for leaks.
4.5.3 Connecting the calibrating gas line (optional)
Connecting the calibrating gas line requires a Ø6 mm or Ø1/4”
pipe fitting.
If the calibrating gas connection was ordered with check
valve, a Ø6 mm or Ø1/4” pipe can be connected directly to the
check valve.
4.6 Connecting the Blowback and Pressure Vessel
(Optional)
The air lines must be connected carefully and properly, using
suitable fittings.
If the probe is equipped with pressure vessel for efficient
blowback (optional), a manual shut-off valve (ball valve) must
be installed in the air supply, immediately upstream from the
pressure vessel.
On probes used to sample flammable gas, nitrogen (inert gas)
must be used for blowback. Blowback of explosive gases is
prohibited.
NOTICE
The operating pressure of the compressed air (inert gas) re-
quired for blowback must always be higher than the process
pressure.
Required pressure differential min. 3 bar (44 psi).
DANGER
Broken pressure vessel
Gas leak, danger due to flying parts.
Maximum operating pressure of the pressure vessel 10 bar
(145 psi)!
The operating pressure reduces based on the operating
voltage (see solenoid valve type plate).
DANGER
Adiabatic compression during gas blowback (explosion
hazard)!
Adiabatic compression may cause high gas temperatures and
must be checked by the user.
Gas blowback may result in high gas temperatures due to
adiabatic compression. This can cause flammable gases to ig-
nite spontaneously.
a) Blowback of explosive atmosphere / gases is prohibited.
b) Flammable atmosphere / gases (non-explosive) may only
be blown back with nitrogen (inert gas).
4.7 Electrical connections
WARNING
Hazardous electrical voltage
The device must be installed by trained staff only.
CAUTION
Wrong mains voltage
Wrong mains voltage may damage the device.
Regard the correct mains voltage as given on the type plate.
CAUTION
Equipment damage
Cables damaged
Do not damage the cable during installation. Install a strain
relief for the cable connection. Secure the cable against twist-
ing and loosening. Please note the temperature resistance of
the cables (> 100 °C/212 °F).
The probe includes two cubic plugs per EN 175301-803 (ex
DIN43650) and a junction box. The plugs are prewired to the
junction box. For safety reasons this connection must not be
modified. The electrical connections must only be run to the
terminals of the junction box.
The power supply for the two heating cartridges (mains sup-
ply 115/230V, 50/60 Hz) and the connection for the thermal
alarm contact are provided via the terminal strip in the junc-
tion box. Per EN 60079-14 and -15, connection for the alarm
output must be connected energy-limited (U
max
= 30 V, I
max
=
100 mA). Please see the enclosed terminal diagram for the
connection.
• Only use cables with a temperature resistance of > 100 °C
to connect to power.
• Make sure the connecting cable has sufficient strain relief
(match cable diameter to the seal on the cubic plug).
• Please note, the heating system briefly has high starting
currents (max. 6 A). Use a suitable fuse (8 A). When con-
necting, please also observe the applicable Ex protection
regulations.
NOTICE
The thermal alarm contact must be connected energy-lim-
ited!
(U
max
= 30 V, I
max
= 100 mA)
11
Bühler Technologies GmbH
BX460058 ◦ 01/2020