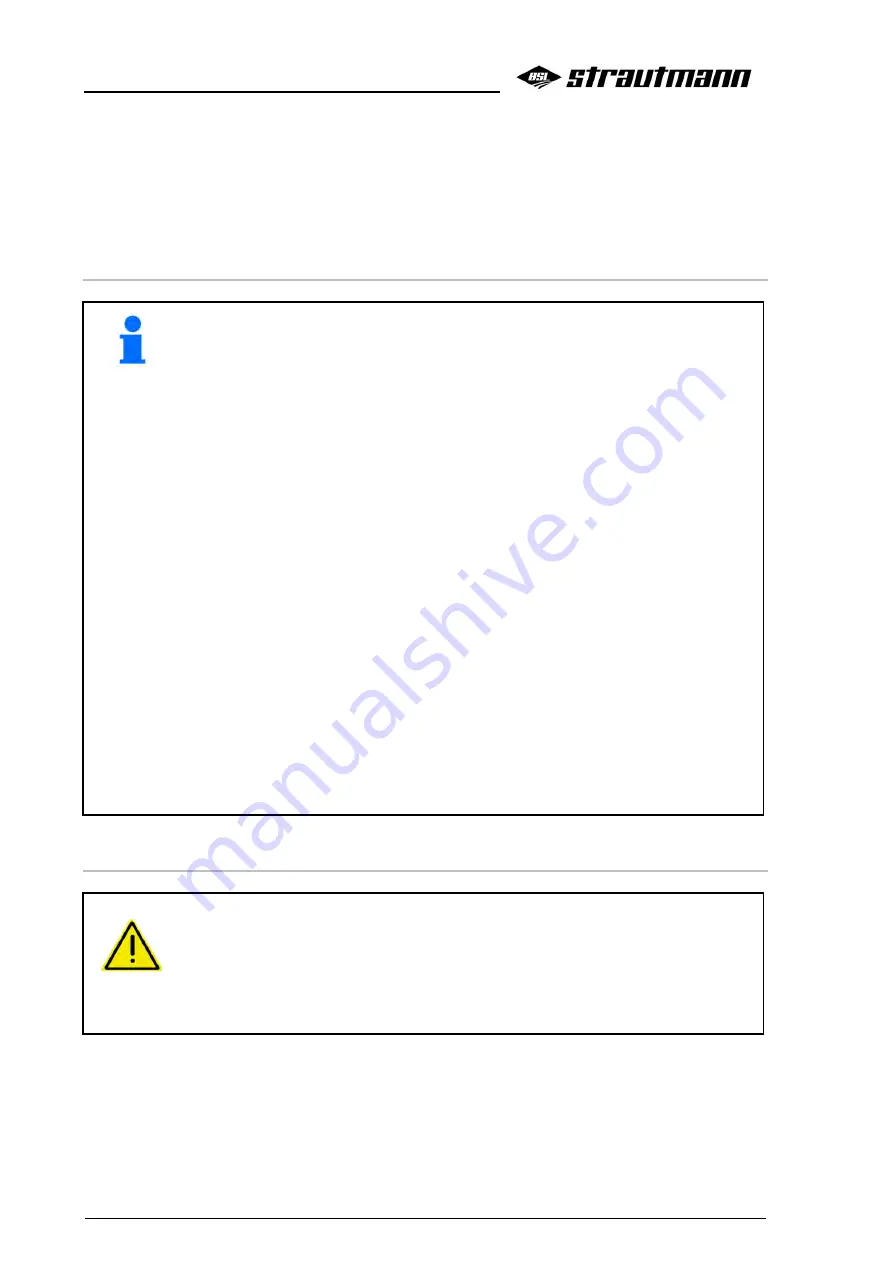
Use of machine
136
Verti-Mix 951-1651, Verti-Mix 951 L-1251 L, Verti-Mix 1501 D-2401 D 10.13
4. Fill in grass silage.
5. Fill in maize silage, grain silage.
6. Fill in fodder components with a high proportion of water, e.g. draff, potato pulp or beet chips
7. Fill liquid components such as liquid yeast, molasses into the mixing container by means of the
loading tool together with the last portion of maize silage.
10.2
Mix fodder components
The type and the structure of the used fodder components and the desired cutting
length of the fodder mixture determine the duration of the last mixing cycle.
The mixing process will be extended for highly-structured fodder components
which must be cut.
Monitor the mixing process from the ladder.
Stop the mixing process when the fodder components have been homogeneously
mixed. In case of a too long mixing process, the mixture risks to lose its structure.
Depending on the structure of the fodder components, the counter-cutters can be
extended into the mixing container at different positions.
The counter-cutters slow down the horizontal revolving of the fodder in the mixing
container, e. g. during chopping and mixing of round or cuboid bales. The further
the counter-cutters project into the mixing container, the larger the slowing-down
effect.
Extend the counter-cutters into the mixing container only as far as to ensure that
the fodder will not get entangled by / pile up on the counter-cutters.
Swivel the counter-cutters only with the mixing auger stopped.
Reduce the driving speed of the mixing auger if light fodder components are
thrown over the edge of the mixing container during mixing.
If, however, the mixing container happens to overflow, an overflow ring (optional
extra) may help. Observe the information in the chapter "Overflow ring", page 55.
Sharp cutting knives reduce the required mixing auger power. Regularly sharpen
cutting knives. Observe the information in the chapter "Grind cutting knives“, page
10.3
Fodder discharge
WARNING
Risk of impact to people and animals if objects are thrown out of the discharge
opening or the crossover conveyor during fodder discharge!
Make sure that people leave the hazardous area of the discharge opening or the
crossover conveyor before opening the discharge opening or switching the crossover
conveyor on.
Keep animals away from the hazardous area.
The fodder discharge can be started after the mixing process has been finished.
The fodder quantity discharged onto the feeding table is set via:
the driving speed of the mixing auger,
the opening width of the discharge door,