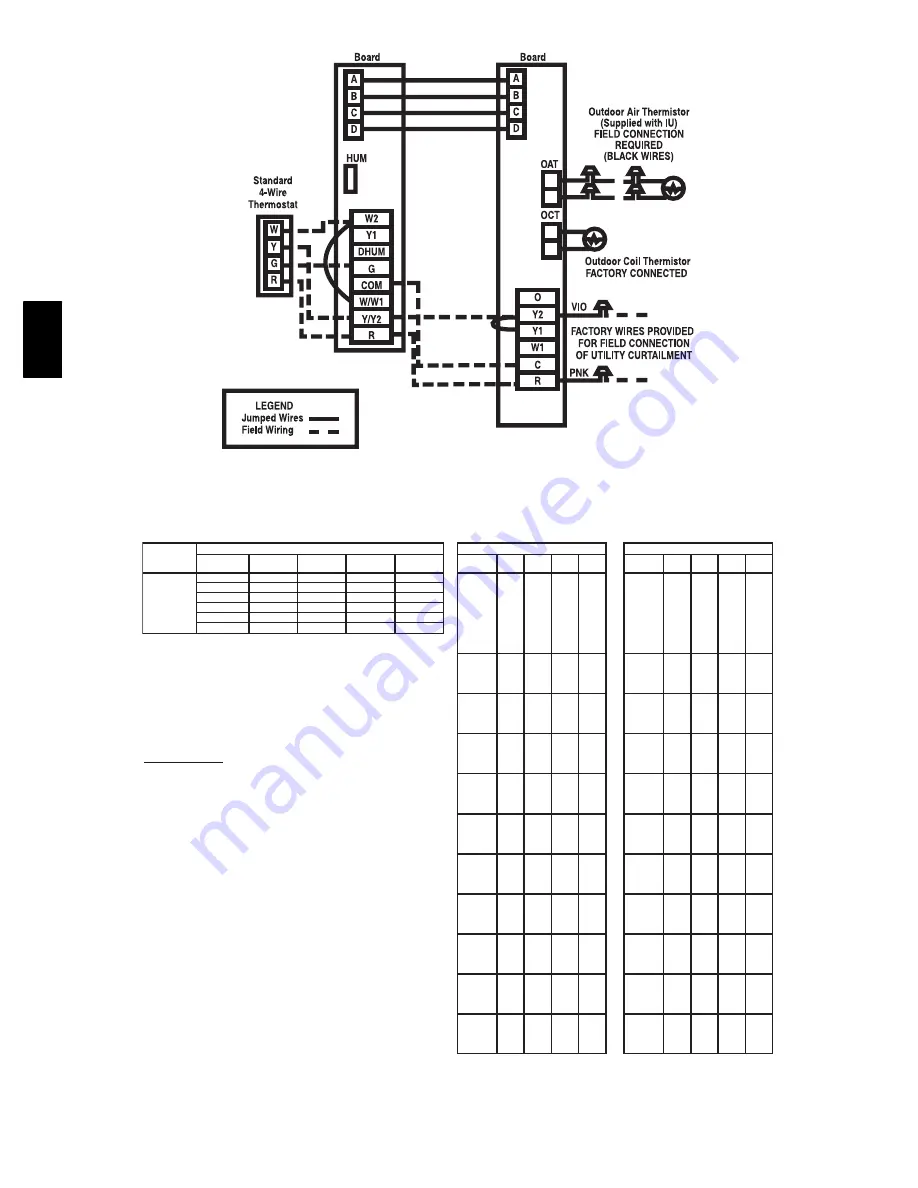
26
Evolution Furnace
Evolution HP/AC
A06360
Fig. 21 -- Non--Communicating Emergency Cooling/Heating Wiring Connections
75 (24)
82 (28)
85 (29)
95 (35)
105 (41)
Pressure
(psig)
5
10
15
25
Pressure
(kPa)
3
6
8
14
024
15.5 ( 8.6 )
15.6 ( 8.7 )
15.7 ( 8.7 )
15.8 ( 8.8 )
15.9 ( 8.9 )
174
56
51
46
36
1200
13
11
8
2
030
16.8 ( 9.3 )
16.4 ( 9.1 )
16.2 ( 9 )
15.6 ( 8.7 )
15 ( 8.3 )
181
59
54
49
39
1248
15
12
9
4
036
14 ( 7.7 )
13.9 ( 7.7 )
13.9 ( 7.7 )
13.8 ( 7.7 )
13.7 ( 7.6 )
188
61
56
51
41
1296
16
13
10
5
042
19.2 ( 10.7 ) 19.1 ( 10.6 ) 19.1 ( 10.6 ) 18.9 ( 10.5 ) 18.7 ( 10.4 )
195
63
58
53
43
1344
17
14
12
6
048
21 ( 11.6 )
20.8 ( 11.5 ) 20.7 ( 11.5 ) 20.4 ( 11.3 ) 20.2 ( 11.2 )
202
65
60
55
45
1393
18
16
13
7
060
16.2 ( 9 )
16.6 ( 9.2 )
16.8 ( 9.3 )
17.3 ( 9.6 )
17.8 ( 9.9 )
209
67
62
57
47
1441
20
17
14
9
216
69
64
59
49
1489
21
18
15
10
223
71
66
61
51
1537
22
19
16
11
189
61
56
51
41
1303
16
13
11
5
196
63
58
53
43
1351
17
15
12
6
203
66
61
56
46
1399
19
16
13
8
210
68
63
58
48
1448
20
17
14
9
217
70
65
60
50
1496
21
18
15
10
224
72
67
62
52
1544
22
19
16
11
231
74
69
64
54
1593
23
20
18
12
238
76
71
66
56
1641
24
21
19
13
245
77
72
67
57
1689
25
22
20
14
252
79
74
69
59
1737
26
23
21
15
Charging Procedure
260
81
76
71
61
1792
27
25
22
16
268
83
78
73
63
1848
29
26
23
17
276
85
80
75
65
1903
30
27
24
19
284
87
82
77
67
1958
31
28
25
20
292
89
84
79
69
2013
32
29
26
21
300
91
86
81
71
2068
33
30
27
22
309
93
88
83
73
2130
34
31
28
23
318
95
90
85
75
2192
35
32
29
24
327
97
92
87
77
2254
36
33
31
25
336
99
94
89
79
2316
37
34
32
26
345
101
96
91
81
2378
38
35
33
27
354
103
98
93
83
2440
39
36
34
28
364
105
100
95
85
2509
40
38
35
29
374
107
102
97
87
2578
41
39
36
30
384
108
103
98
88
2647
42
40
37
31
394
110
105
100
90
2716
44
41
38
32
404
112
107
102
92
2785
45
42
39
33
414
114
109
104
94
2854
46
43
40
34
424
116
111
106
96
2923
47
44
41
35
434
118
113
108
98
2992
48
45
42
36
444
119
114
109
99
3061
48
46
43
37
454
121
116
111
101
3130
49
47
44
38
464
123
118
113
103
3199
50
48
45
39
474
124
119
114
104
3268
51
48
46
40
484
126
121
116
106
3337
52
49
47
41
494
127
122
117
107
3406
53
50
47
42
504
129
124
119
109
3475
54
51
48
43
514
131
126
121
111
3544
55
52
49
44
524
132
127
122
112
3612
56
53
50
45
534
134
129
124
114
3681
56
54
51
45
Required Subcooling (
o
F)
Required Subcooling (
o
C)
Required Liquid Line Temperature for a Specific Subcooling (R-410A)
1- Measure Discharge line pressure by attaching a gauge to the service port
2- Measure the Liquid line temperature by attaching a temperature sensing device to it
3- Insulate the temperature sensing device so that the Outdoor Ambient doesn’t affect the reading
4- Refer to the required Subcooling in the table based on the model size and the Outdoor Ambient
temperature
5- Interpolate if the Outdoor temperature lies in between the table values. Extrapolate if the
temperature lies beyond the table range
6- Find the Pressure Value corresponding to the the measured Pressure on the Compressor
Discharge line
7- Read across from the Pressure reading to obtain the Liquid line temperature for a required
Subcooling
8- Add Charge if the measured temperature is higher than the liquid line temperature value in the
table
9- Add Charge using the service connection on the Suction line of the Compressor
Required Subcooling
o
F (
o
C)
Outdoor Ambient Temperature
Model Size
A06315
Fig. 22 -- Cooling Charging Table--Subcooling
577D
Содержание EVOLUTION 577D
Страница 4: ...4 A06604 Fig 5 577D024 030 Unit Dimensions ...
Страница 5: ...5 A06605 Fig 6 577D036 060 Unit Dimensions ...
Страница 17: ...17 6 0 A06310 Fig 16 Wiring Schematic 577D Single Phase 577D ...
Страница 35: ...35 577D ...