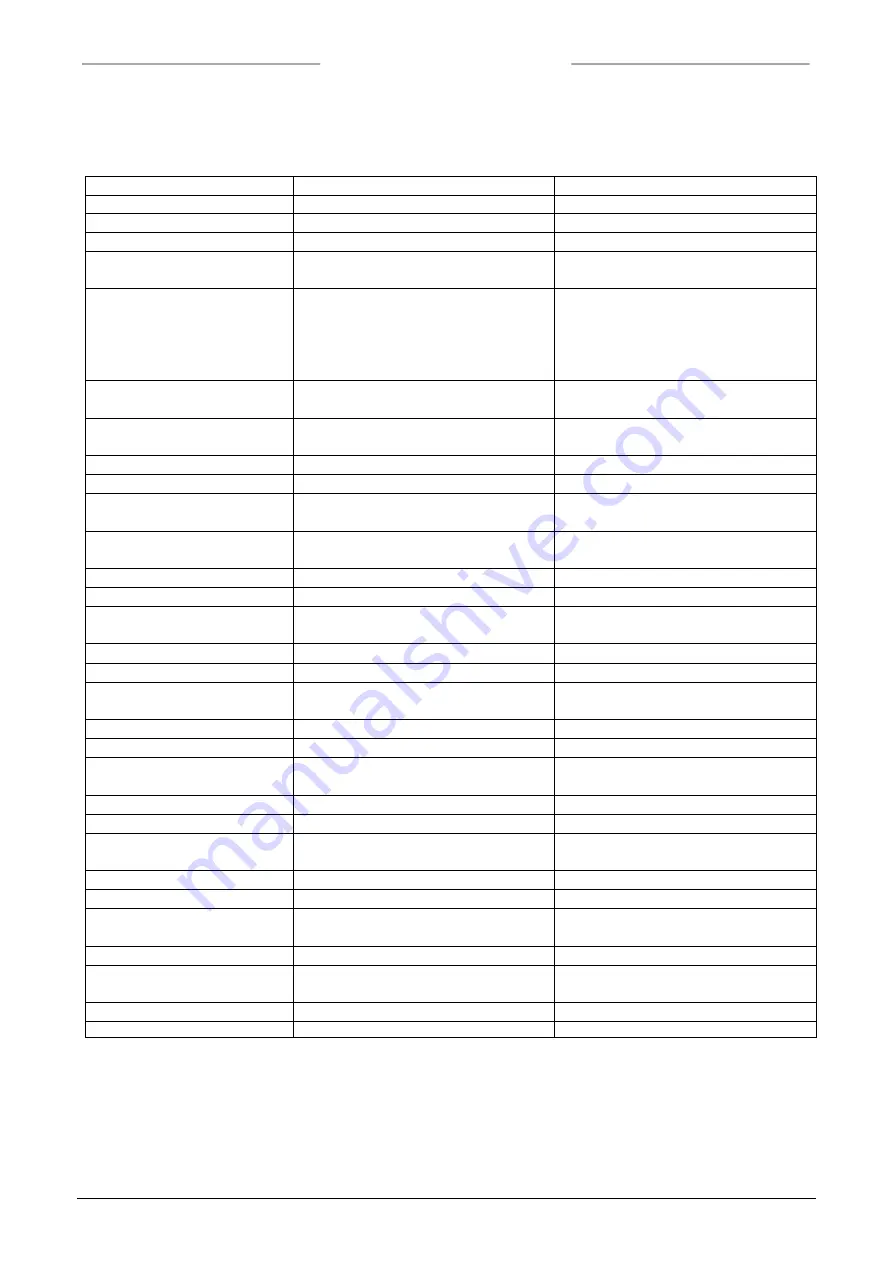
Bronkhorst
®
9.17.057
page 24
5.3 Troubleshooting summary general
Symptom
Possible cause
Action
No output signal
No power supply
Check power supply and hook-up
Check cable connection and hook-up.
Check status of LED’s
(see manual 9.17.023 chapter 10)
No setpoint
For analog used instruments measure
between pin 3 and 8 of sub-D9
connector.
For digital use make sure to perform a
read setpoint after sending
Cable damaged or hooked-up wrong
Check and compare signals at both ends
of cable.
PC-board damaged due to long lasting
shortage and/or high-voltage peaks
Return to factory
No or too low inlet pressure
Increase inlet pressure
Open shut-off at inlet and outlet
Supply pressure too high, or differential
pressure across meter too high
Reduce supply pressure
Valve blocked / contaminated
Set control mode to valve fully open
and check if it opens
Sensor / capillary failure
Return to factory
Maximum output signal
Leakage of control valve
Set control mode to valve close and
check if it closes
Sensor / capillary failure
Return to factory
Output signal much lower than
setpoint signal or desired flow
Incorrect type of gas or too low inlet
pressure
Test instrument on conditions for which
it was designed
Oscillation
Supply pressure / diff. pressure too high Reduce pressure
Pressure regulator of supply pressure is
oscillating or wrong sized
Replace pressure regulator
Controller adjustment wrong
Adjust controller with PID settings
Flow is gradually decreasing
Condensation, can occur e.g. with NH
3
Decrease supply pressure and / or heat
gas to be measured
Small flow at zero setpoint
Valve leaks due to damage or dirt
Return to factory
Increased zero reading without flow
caused by raised zero-point
Perform an auto-zero action
No digital communication
Occupied or wrong bus address
Change address with software or
rotary-switches
No or wrong bus termination
Check cabling and termination