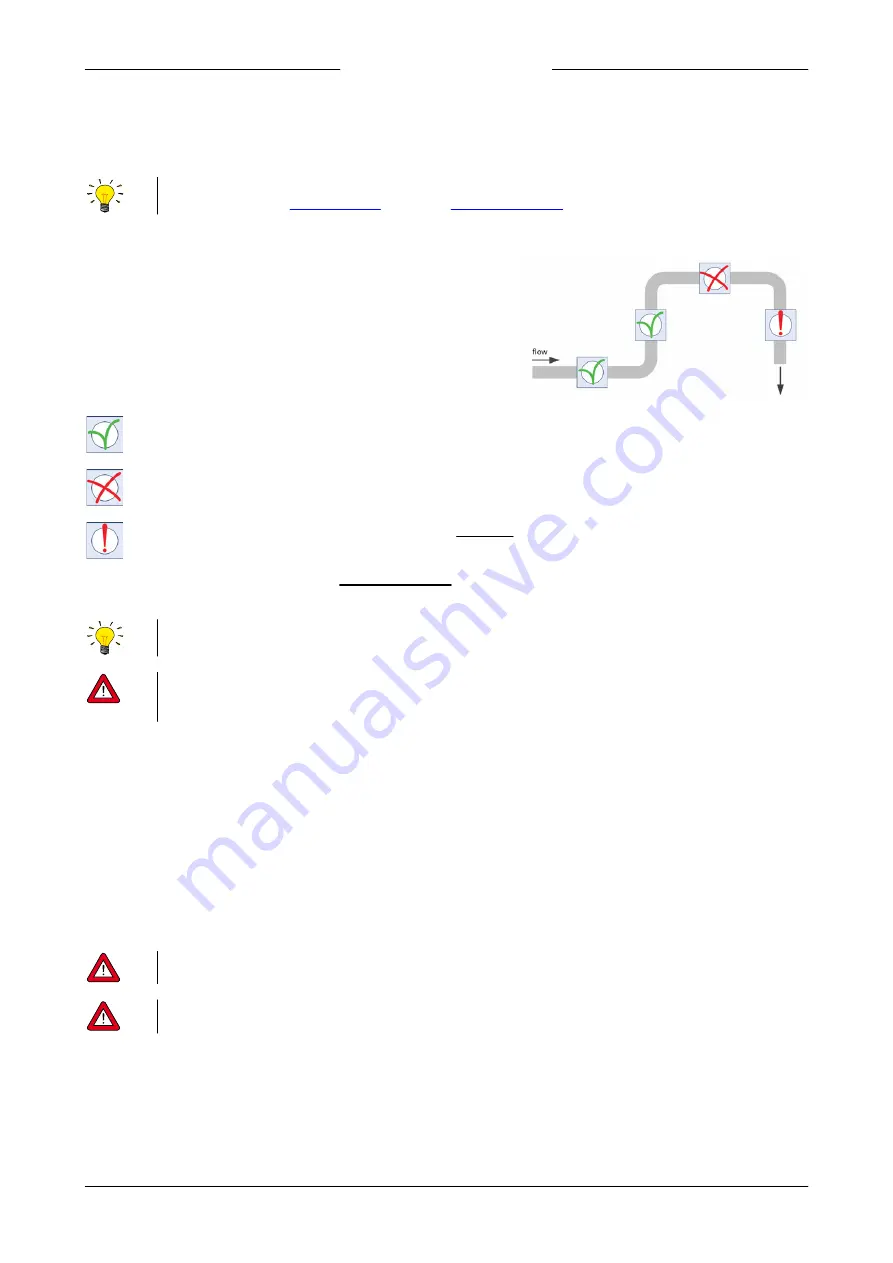
Bronkhorst®
Instruction Manual ES-FLOW™ 1xxC
9.17.153A
14
4
Installation
4.1
Mounting
For stable fixation to a rigid and stable surface or construction, use the threaded mounting holes in the rear of the
instrument housing (see
). Consult the
for the exact size and locations.
4.1.1
Location
Gas bubbles in the liquid can lead to measuring errors. In general, the
instrument should be mounted in a pipe segment where gas bubbles
cannot accumulate. The image on the right shows the preferable
mounting locations.
·
In general, the best location is a horizontal pipe segment or a segment where the fluid direction is upward.
·
Gas might accumulate in the horizontal segment if it is followed by a downward segment. Do not mount
the instrument in a location like this.
·
Mounting in a downward pipe segment with an open end is strongly dissuaded, especially if the pipe
diameter is 1/2" or more. Gravity might let the segment run empty; depending on the specific system
dimensions and the viscosity of the metered fluid, this effect might be stronger or weaker.
·
If the instrument is part of a closed fluid system, mounting the instrument in a downward pipe segment is
not preferable, but may be considered if other mounting locations are problematic.
To minimize the risk of gas bubbles caused by cavitation, the preferred location to install a (control) valve is downstream
from the instrument, the preferred location for a pump is upstream.
To prevent damage to the internal electronics, make sure the temperature inside the instrument housing does not get
above 60 °C. If necessary, take appropriate heat dissipation measures, especially if the instrument is operated inside an
enclosure (e.g. a control cabinet).
4.1.2
Orientation
Aside from specific application requirements, the ES-FLOW™ has no preferred mounting orientation.
4.2
Fluid connections
For regular (mono-directional) use, install the ES-FLOW™ in the process line, in accordance with the direction of the FLOW
arrow on the instrument. For bi-directional measuring, install the instrument in the direction in which the highest flow will
be measured (if applicable). When deciding which direction to install the instrument in, take into account that the
measuring range in the reverse direction is approximately 73% of the full scale range (whereas the instrument can measure
131% FS in the normal direction).
Tighten fittings according to the instructions issued by their manufacturer.
Do not apply fluid pressure until all required fluid connections and electrical connections have been made.
Check the fluid system for leaks before applying full operating pressure, especially when using hazardous media (e.g. toxic
or flammable).