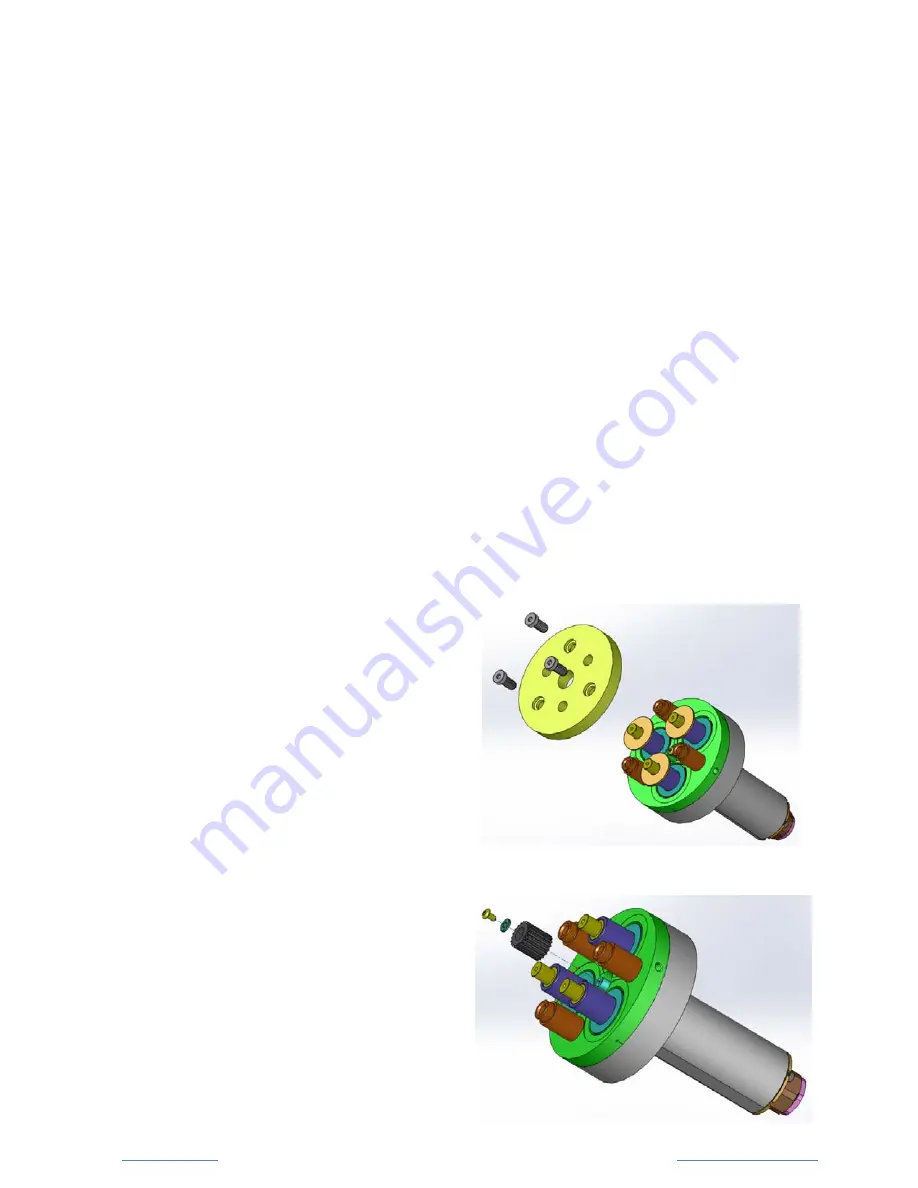
CJWinter Page 9
Periodic Maintenance
CJWinter recommends an annual teardown and inspection of this tool.
We recommend the periodic lubrication of all moving parts with oil, and
replacement of the Thrust Bearings (#10) and Thrust Washers (#11 & #22) in
the tool. The frequency of lubrication and replacement depends greatly on the
severity of service the tool sees, the type of knurl being rolled, and the
adherence to proper setting and operation procedures. The frequency should
be determined by your own in-shop experience, and be scheduled in a
preventative manner. At a minimum, we recommend replacement of these
components during the annual inspection.
The remaining components are not generally considered "wear" parts, and
should be replaced only in the event of damage or excessive wear.
Preparing the Tool
To install the appropriate knurl rolls, follow these simple steps:
1.
Remove the three Low Head Cap
Screws (#8) from the Front Plate
(#1).
2.
Pull the Front Plate (#1) away
from the rest of the tool body,
being careful not to drop any of
the Thrust Washers (#11 & #22),
Bearings (#10) or Carbide
Bushings (#5).
3.
Install a new master pinion by
loosening the Button Head
Socket Screw (#17) at the
center of the gear, replacing the
gear, and reinstalling the screw
with the Thrust Washer (#15)
under the head.
Содержание CJWINTER 192 Series
Страница 1: ...192 Series Precision Involute Knurl Spline Tools Instruction Manual ...
Страница 16: ...Assembly Drawing ...