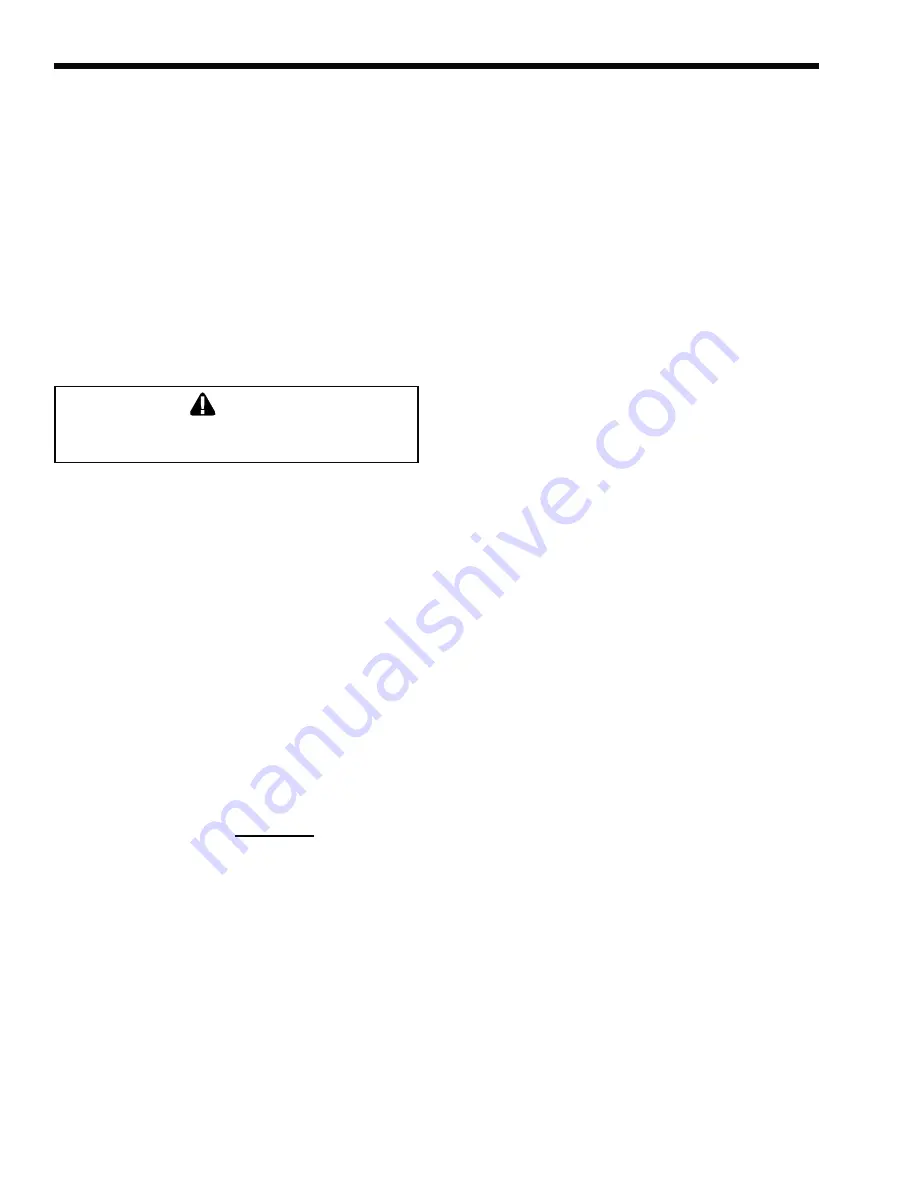
B
RADFORD
W
HITE
C
ORP.
Page 14
7.
All threaded joints should be coated with
piping compound resistant to action of liquefied
petroleum gas.
8.
The appliance and its individual shutoff valve
must be disconnected from the gas supply piping
during any pressure testing of that system at test
pressures in excess of 1/2 PSIG (3.45kpa).
9.
The unit must be isolated from the gas supply
system by closing its individual manual shutoff
valve during any pressure testing of the gas
supply piping system at test pressures equal to or
less than 1/2 PSIG (3.45kpa).
10. The appliance and its gas connection must be
leak tested before placing it in operation.
11. Purge all air from gas lines.
WARNING
Open flame can cause gas to ignite and result in
property damage, severe injury, or loss of life.
NOTE
: The Brute Magnum appliance and all other
gas appliances sharing the gas supply line must be
firing at maximum capacity to properly measure the
inlet supply pressure. The pressure can be measured
at the supply pressure port on the gas valve. Low
gas pressure could be an indication of an undersized
gas meter, undersized gas supply lines and/or an
obstructed gas supply line. A bleed line from the
diaphragm-type automatic valve shall be vented per
local code requirements. Brute Magnum units are
equipped with low and high gas pressure switches that
are integrally vent limited. These types of devices do
not require venting to atmosphere.
Section 4A
WATER CONNECTIONS —
BRUTE MAGNUM BOILER
4A.1 Heating System Piping:
Hot Supply Connections — Boiler
NOTE:
This appliance must be installed in a closed
pressure system with a minimum of 12 psi (82.7kPa)
static pressure at the boiler.
Hot water piping should be supported by suitable
hangers or floor stands. Do not support piping with
this appliance. Due to expansion and contraction of
copper pipe, consideration should be given to the type
of hangers used. Rigid hangers may transmit noise
through the system resulting from the piping sliding in
the hangers. It is recommended that padding be used
when rigid hangers are installed. Maintain 1" (2.5cm)
clearance to combustibles for hot water pipes.
Pipe the discharge of the relief valve (full size)
to a drain or in a manner to prevent injury in the event
of pressure relief. Install an air purger, an air vent,
a diaphragm-type expansion tank, and a hydronic
flow check in the system supply loop. Minimum fill
pressure must be 12psig (82.7kPa). Install shutoff
valves where required by code.
Suggested piping diagrams are shown in Figures
4, 5, and 6. These diagrams are meant only as a guide.
Components required by local codes must be properly
installed. The Brute Magnum boiler’s efficiency
is higher with lower return water temperatures.
Therefore, to get the most of low return temperature
with multiple boilers, pipe as shown in Figure 4.
The Brute Magnum boiler has an internal mixing
system that ensures that the condensation does not
occur on the finned copper heat exchanger, with
boiler return temperature down to 50°F (10°C).
This
system, that consists of automatically actuated
and linked valves, is set up at the factory, and is
non-adjustable.
The return water goes through the
stainless steel heat exchanger, then to the mixing
system (see Figure 7).
If the water at the inlet of the copper heat
exchanger is less than 140°F (60°C), water from the
outlet of the copper heat exchanger will be directed
back to the inlet of the copper heat exchanger, and will
mix to bring the inlet water up to 140°F (60°C). Once
through the copper heat exchanger, the water picks up
another 20-25°F (11-14°C) (when at high fire), and
it leaves the boiler at 160-165°F (71-74°C). This hot
water is then sent to the system.
If the water at the inlet of the copper heat exchanger
is 140°F (60°C), or higher, the water will be allowed to
flow through the copper heat exchanger and directly to the
outlet of the Brute Magnum, and there will be a 20-25°F
(11-14°C) temperature rise between the inlet and outlet of
the unit, when the unit is at high fire.
The pump in the boiler is sized for the boiler’s
heat exchangers, the internal mixing system, and 30
feet of full-sized piping, with a normal number of
fittings taken into consideration. The piping must be
primary/secondary, ensuring that the boiler’s pump is
only used for the boiler, and that the system pump(s)
do not interfere with the Brute Magnum pump or
mixing system.
The minimum inlet water temperature for the
Brute Magnum is 50°F (10°C) to avoid condensing
on the copper coils.
4A.2 Cold Water Make-Up — Boiler
1.
Connect the cold water supply to the inlet
connection of an automatic fill valve.
2.
Install a suitable back flow preventer between the
automatic fill valve and the cold water supply.
3.
Install shut off valves where required.
NOTE:
The boiler, when used in connection with a
refrigeration system, must be installed so the chilled
Содержание BRHHH
Страница 2: ...BRADFORD WHITE CORP Page 2...
Страница 20: ...BRADFORD WHITE CORP Page 20 Figure 8 Water Heater Piping One Heater One Tank...
Страница 21: ...Brute Magnum Page 21 Figure 9 Water Heater Piping Multiple Heaters One Tank...
Страница 22: ...BRADFORD WHITE CORP Page 22 Figure 10 Water Heater Piping One Heater Multiple Tanks...
Страница 23: ...Brute Magnum Page 23 Figure 11 Water Heater Piping Multiple Heaters Multiple Tanks...
Страница 30: ...BRADFORD WHITE CORP Page 30 Figure 17 Wiring Diagram Size 1200 Standard and Codes A and F...
Страница 31: ...Brute Magnum Page 31 Figure 18 Wiring Diagram Sizes 1600 2000 and 2400 Standard and Codes A and F...
Страница 32: ...BRADFORD WHITE CORP Page 32 Figure 19 Wiring Diagram Size 1200 Code B...
Страница 33: ...Brute Magnum Page 33 Figure 20 Wiring Diagram Sizes 1600 2000 and 2400 Code B...
Страница 39: ...Brute Magnum Page 39 Figure 27 Gas Trains...
Страница 49: ...Brute Magnum Page 49 Figure 30 Combustion Components...
Страница 50: ...BRADFORD WHITE CORP Page 50 Figure 31 Gas Train Combustion Air Components...
Страница 51: ...Brute Magnum Page 51 Figure 32 Gas Train Components...
Страница 52: ...BRADFORD WHITE CORP Page 52 Figure 33 Electrical Components...
Страница 53: ...Brute Magnum Page 53 Figure 34 Heat Exchanger Water Path Components...
Страница 54: ...BRADFORD WHITE CORP Page 54 Figure 35 Heat Exchanger Water Path Components...
Страница 55: ...Brute Magnum Page 55 Figure 36 Jacket Components...