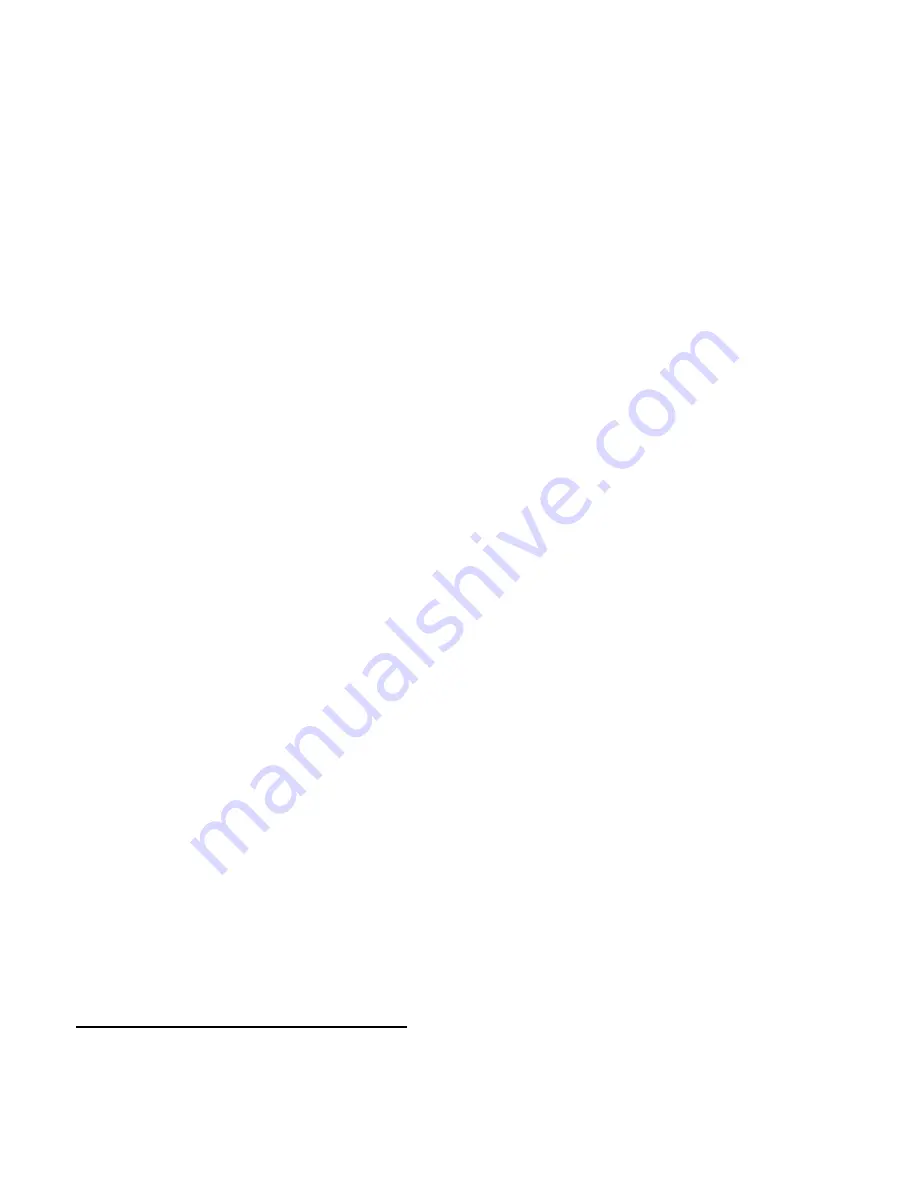
14
the chimney. A thimble should be used to connect the vent connector pipe to the chimney so that the
vent connector pipe may be readily removed in case of inspection or replacement.
Connection to the chimney must be made above the bottom of the chimney to avoid blockage. Vent
piping should extend just into the chimney far enough to expel flue gasses. Inserting the vent piping
too far into the chimney will cause undue obstruction. Use a thimble or a slip joint where vent pipe
enters the chimney to allow easy removal for cleaning.
A draft regulator, which is shipped in the blower compartment, must be installed in the vent piping. It
should be located at least 24 inches from the furnace if possible in either a horizontal or vertical
section of the vent pipe. The draft regulator must be installed in the same room as the furnace and in
such a manner that there is no difference in pressure between the air in the vicinity to the regulator and
the combustion air supply. Ensure that the barometric damper is accessible for adjustment.
With the burner operating, use a draft gauge to adjust the regulator to the proper setting (see
instructions enclosed with draft gauge to adjust the regulator to the proper setting). When the burner
air supply and draft are properly adjusted, the over-fire draft should be a negative .02" W.C.
Two or more oil burning appliances each equipped with a safety control may be permitted to be
connected to one common chimney if sufficient draft is available for the safe simultaneous removal of
all products of combustion.
If two or more openings are provided into one chimney, they shall be at different levels on the same
story of the building, with the smaller appliance entering at the highest possible level consistent with
clearances to combustible materials.
Two or more connectors shall not be joined together unless the common connector, manifold and
chimney are properly sized. Adequate draft must be available to safely remove all products of
combustion simultaneously without leakage, or back flow.
Power Venting
The furnace may be power vented through a side wall by using a listed power side wall Venter. The
vent device must be able to produce a draft of -.02”W.C. over the fire and be equipped with a post
purge timer set to a minimum time of 5 minutes. The power vent must be installed in accordance with
the recommendations of the manufacturer, all applicable building code requirements, and NFPA-31.
Vent Dampers
Do not install a thermal type vent damper on the furnace. Failure to comply could result in severe
personal injury, death or substantial property damage. If a vent damper is required, use only a
motorized damper, wired and installed following the vent damper manufacturer’s instructions.
Blocked Vent Switch
Furnaces installed in a chimney require a blocked vent shut-off system when installed in Canada. A
safety switch is provided on those units shipped to Canada to perform this function. It is the
installer’s responsibility to install the switch in accordance with the instructions provided by the
manufacturer.
The blocked vent switch is a safety device for detecting the spillage of flue gases due to inadequate
draft or a blocked flue
. NEVER RESET THE SWITCH UNLESS THE CAUSE OF THE BLOCKAGE HAS
BEEN CORRECTED.
Ventilation and Combustion Air
Appliances shall be installed in a location where the facilities for ventilation permit the satisfactory
combustion of oil, proper venting and the maintenance of ambient temperature at safe limits under
normal conditions of use. The burner requires a generous amount of clean combustion air to operate
Содержание RSM 500
Страница 20: ...20 Furnace Wiring PSC Motors ...
Страница 21: ...21 Furnace Wiring Nidec ECM Motors ...