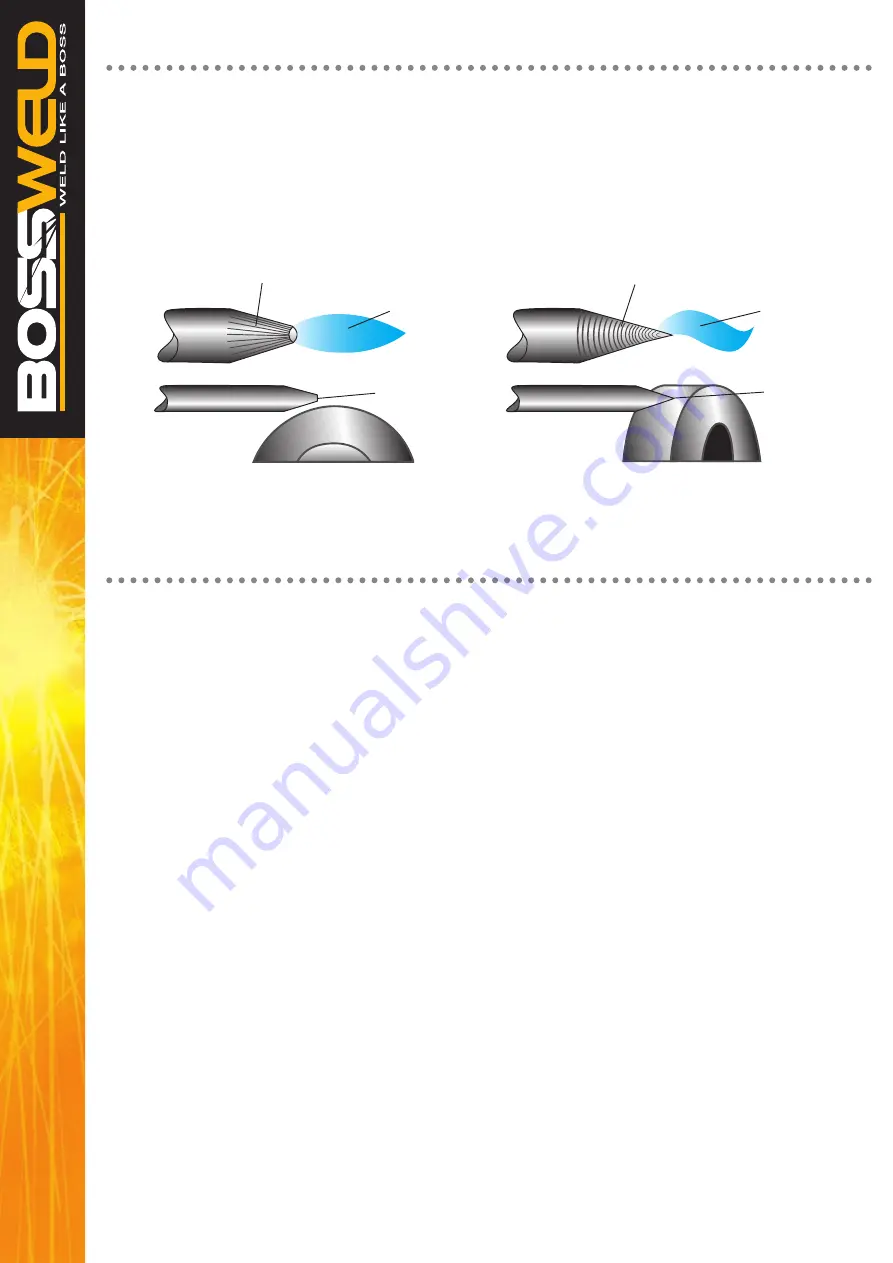
38
TIG WELDING
Tungsten inert gas (TIG) welding became an overnight success in the 1940s for joining magnesium and
aluminium. Using an inert gas shield instead of a slag to protect the weldpool, the process was a highly
attractive replacement for gas and manual metal arc welding. TIG has played a major role in the acceptance
of aluminium for high quality welding and structural applications.
PROCESS CHARACTERISTICS
In the TIG process the arc is formed between a pointed tungsten electrode and the workpiece in an inert
atmosphere of argon or helium. The small intense arc provided by the pointed electrode is ideal for high
quality and precision welding. Because the electrode is not consumed during welding, the welder does not
have to balance the heat input from the arc as the metal is deposited from the melting electrode. When filler
metal is required, it must be added separately to the weldpool.
POWER SOURCE
TIG must be operated with a constant current power source - either DC or AC. A constant current power
source is essential to avoid excessively high currents being drawn when the electrode is short-circuited onto
the workpiece surface. This could happen either deliberately during arc starting or inadvertently during
welding. If, as in MIG welding, a flat characteristic power source is used, any contact with the workpiece
surface would damage the electrode tip or fuse the electrode to the workpiece surface. In DC, because arc
heat is distributed approximately one- third at the cathode (negative) and two-thirds at the anode (positive),
the electrode is always negative polarity to prevent overheating and melting. However, the alternative power
source connection of DC electrode positive polarity has the advantage in that when the cathode is on the
workpiece, the surface is cleaned of oxide contamination. For this reason, AC is used when welding
materials with a tenacious surface oxide film, such as aluminium.
ARC STARTING
The welding arc can be started by scratching the surface, forming a short-circuit. It is only when the
short-circuit is broken that the main welding current will flow. However, there is a risk that the electrode may
stick to the surface and cause a tungsten inclusion in the weld.
TUNGSTEN PREPARATION & GRINDING
Grinding creates the greatest hazard as the exposed tungsten/thoria area is greatly increased and fine
particles of potentially radioactive dust are released into the atmosphere. It is recommended that a dedicated
grindstone with local dust extraction is used, and a simple filter mask is worn. If the grinding wheel is not
fitted with a protective viewing screen, eye protection must be worn.
TRIGGER
WELDING WIRE
FLUX COATING
ROD
ARC
CONTACT TIP
DROPLETS
SHIELDING GAS
ARC
MOLTEN WELD METAL
SHROUD
WORK PIECE
WORK PIECE
WORK PIECE
WORK PIECE
WORK PIECE
WORK PIECE
WORK PIECE
WORK PIECE
STRAIGHT GROUND
CORRECT PREPERATION
- STABLE ARC
INCORRECT PREPERATION
- STABLE ARC
RADIAL GROUND
ARC WANDER
TUNGSTEN ELECTRODE
GAS LENS
STABLE ARC
FLAT TIP
POINTED TIP
GRINDING WHEEL
GRINDING WHEEL
FILLER WIRE
Note: Do not use wheel for other jobs or tugsten can become contaminated and cause lower weld quality
Содержание 660250
Страница 1: ...DUAL PULSE SYNERGIC MST INVERTER WELDER MANUAL POWERPULSE 250 2 YEAR LIMITED WARRANTY ...
Страница 47: ...47 ...