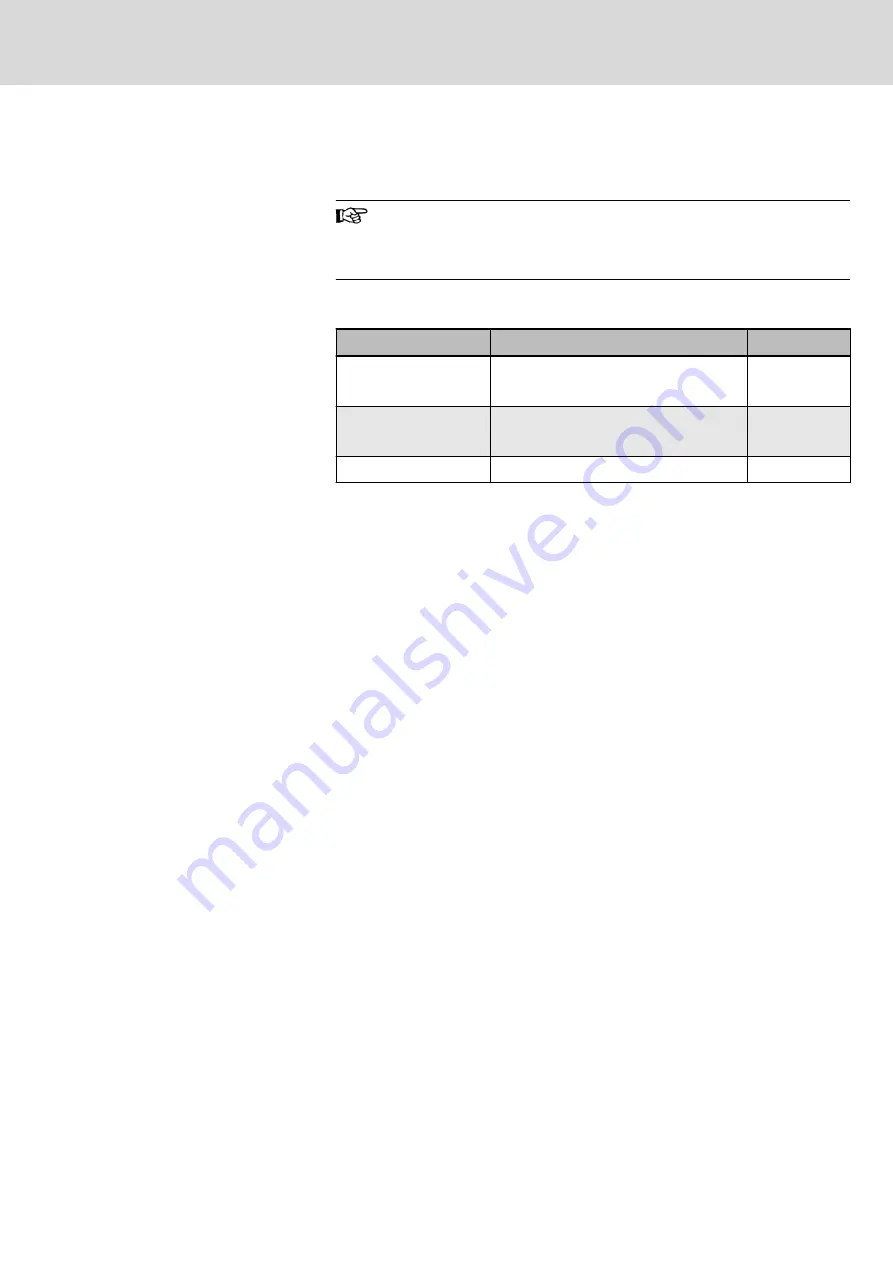
With the above-specified settings, the effective commutation offset
(P-0-0521) is automatically calculated on switching to operating mode. The
drive is ready for power activation.
The procedure “Reference point optimum commutation offset”
cannot be used in the case of analog Hall units, as the necessary
parameter P-0-0508 already uses the procedure “Commutation
via analog Hall units”.
Commutation by means of digital
Hall unit
For operation on Rexroth IndraDrive Cs, the following sercos parameters
must be edited before commissioning:
Ident number
Description
Value
P-0-0509
(for MCP020)
Rough commutation offset
1)
946
P-0-0509
(for MCP030 ... 070)
Rough commutation offset
1)
62
P-0-0074
Encoder type 1 (motor encoder)
23
1)
The parameter is used to enter the motor depending constants.
It is not the actually commutation offset. This is displayed with‐
in parameter P-0-0521 “Effective commutation offset” after au‐
tomatic calculation.
Tab. 14-5:
Parameters to be checked before commutation adjustment
With the above-specified settings, the effective commutation offset
(P-0-0521) is automatically calculated on switching to operating mode. Com‐
mutation by means of digital Hall unit only enables reaching of an electrical
accuracy of +/- 30°. In this respect, a maximum power loss of 14 % is to be
expected.
Hence the maximum motor force is available, a “Reference point optimum
commutation offset” must be stored on the reference point.
Procedure at IndraDrive Cs:
1.
Activate initial commissioning mode (P-0-0522, bit 15)
2.
Carry out commutation adjustment using the sinusoidal procedure.
3.
Switch axis to "AF".
4.
Start fine commutation.
5.
Initiate reference point run.
If the reference point is reached, the "reference point of optimum com‐
mutation offset" (P-0-0508) is placed there.
6.
Deactivate initial commissioning mode.
On each restart of the machine, the rough commutation offset (+/- 30°) is de‐
termined by switching to operating mode. The drive may now run to the refer‐
ence point with reduced force. If the reference point is reached or passed, the
optimum reference point for the commutation offset is applied by the drive
and the maximum force is available to the axis.
14.6.4
Measuring procedure: Measuring of the relation between primary and
secondary part
For commutation setting, this procedure requires determination of the relative
position of the primary part in relation to the secondary part. This procedure
has the advantage that commutation adjustment does not require any power
MCL Ironless Linear Motors
177/197
Commissioning, operation and maintenance
R911330592_Edition 06 Bosch Rexroth AG
Содержание rexroth MCL
Страница 1: ...MCL Ironless Linear Motors Project Planning Manual R911330592 Edition 06 ...
Страница 16: ...8 197 MCL Ironless Linear Motors Bosch Rexroth AG R911330592_Edition 06 ...
Страница 52: ...44 197 MCL Ironless Linear Motors Bosch Rexroth AG R911330592_Edition 06 ...
Страница 57: ...MCL Ironless Linear Motors 49 197 Dimension sheets R911330592_Edition 06 Bosch Rexroth AG ...
Страница 68: ...60 197 MCL Ironless Linear Motors Bosch Rexroth AG R911330592_Edition 06 ...
Страница 90: ...82 197 MCL Ironless Linear Motors Bosch Rexroth AG R911330592_Edition 06 ...
Страница 104: ...96 197 MCL Ironless Linear Motors Bosch Rexroth AG R911330592_Edition 06 ...
Страница 162: ...154 197 MCL Ironless Linear Motors Bosch Rexroth AG R911330592_Edition 06 ...
Страница 174: ...166 197 MCL Ironless Linear Motors Bosch Rexroth AG R911330592_Edition 06 ...
Страница 196: ...188 197 MCL Ironless Linear Motors Bosch Rexroth AG R911330592_Edition 06 ...
Страница 198: ...190 197 MCL Ironless Linear Motors Bosch Rexroth AG R911330592_Edition 06 ...
Страница 204: ...Notes 196 197 MCL Ironless Linear Motors ...
Страница 205: ...Notes MCL Ironless Linear Motors 197 197 ...