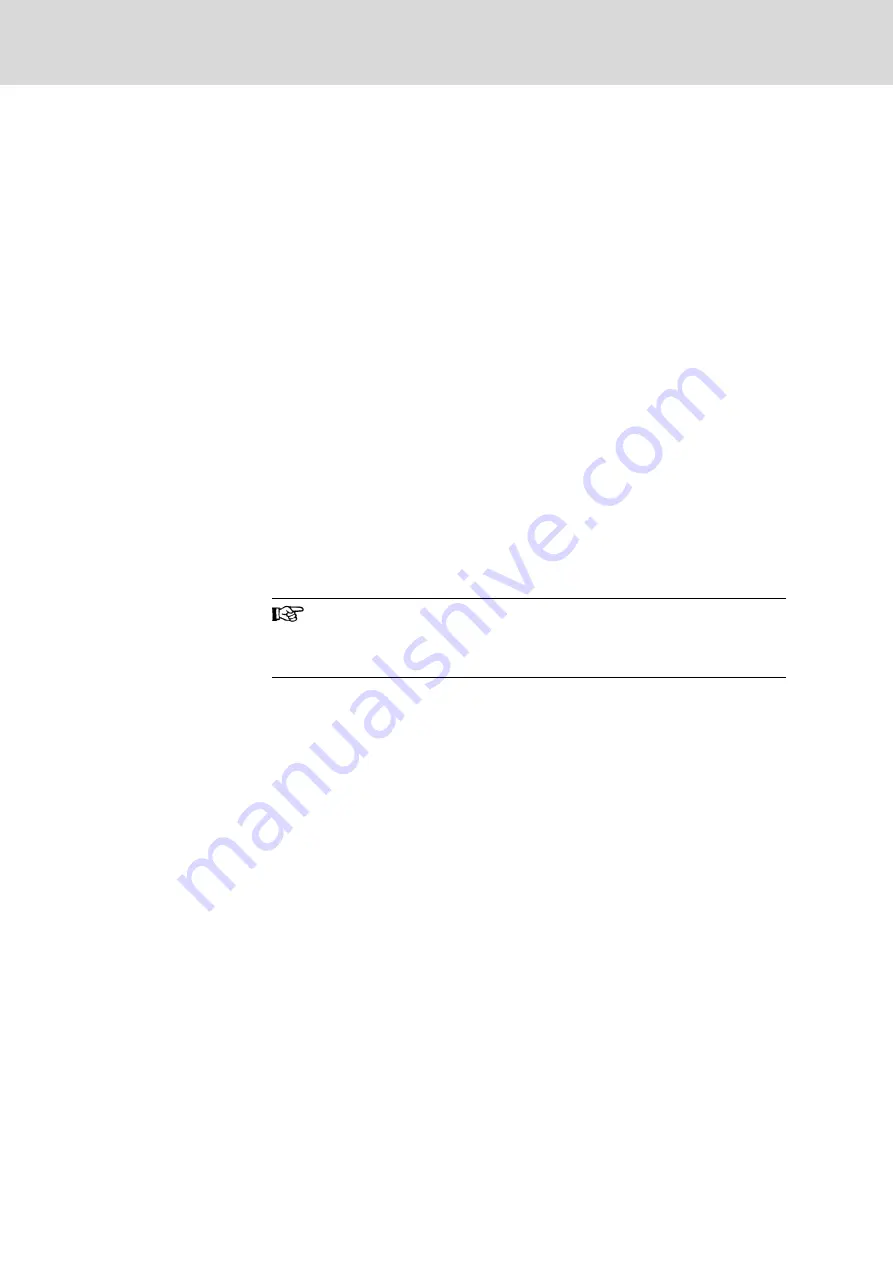
9.20.3
Deactivation by a master control
Deactivation by control functions
Deactivation by the master control should be performed in the following
steps:
1. The machine PLC or the machine I/O level reports the fault to the CNC
control
2. The CNC control deactivates the drives via a ramp in the fastest possi‐
ble way
3. The CNC control causes the power at the power supply module to be
shut down.
Drive initiated via the control shutdown
Deactivation via means of drive functions should be performed in the follow‐
ing steps:
1. The machine I/O level reports the fault to the CNC control and SPS
2. The CNC control or the PLC resets the controller enabling signal of the
drives. If SERCOS interface is used, it deactivates the ”E-STOP” input
at the SERCOS interface module.
3. The drive responds with the selected error response.
4. The power at the power supply module must be switched off 500 ms af‐
ter the controller enabling signal has been reset or the ”E-Stop” input
has been deactivated.
The delayed power shutdown ensures the safe shutdown of the
drive by the drive controller. With an undelayed power shutdown,
the drive coasts in an uncontrolled way once the DC bus energy
has been used up.
9.20.4
Deactivation via mechanical braking device
Shutdown by mechanical braking devices should be activated simultaneously
with switching off the power at the power supply module. Integration into the
holding brake control of the drive controllers is possible, too. The following
must be observed:
●
Braking devices with electrical 24V DC control (electrically-released)
and currents < 2 A can directly be triggered.
●
Braking devices with electrical 24V DC control and currents > 2 A can
be triggered via a suitable protection.
Once the controller enabling signal has been removed, the holding brake
control has the following effect:
●
Fault reaction ”0”, ”1” and ”3”.
The holding brake control drops to 0 V once the velocity is less than 10
mm/min or a time of 400 ms has elapsed.
●
Fault reaction "2":
The holding brake control drops to 0 V immediately after the drive ena‐
bling signal has been removed.
9.20.5
Response to a power outage
In order to be able to shut down the linear drive as fast as possible in the
event of a power outage,
126/197
Application and construction instructions
MCL Ironless Linear Motors
Bosch Rexroth AG R911330592_Edition 06
Содержание rexroth MCL
Страница 1: ...MCL Ironless Linear Motors Project Planning Manual R911330592 Edition 06 ...
Страница 16: ...8 197 MCL Ironless Linear Motors Bosch Rexroth AG R911330592_Edition 06 ...
Страница 52: ...44 197 MCL Ironless Linear Motors Bosch Rexroth AG R911330592_Edition 06 ...
Страница 57: ...MCL Ironless Linear Motors 49 197 Dimension sheets R911330592_Edition 06 Bosch Rexroth AG ...
Страница 68: ...60 197 MCL Ironless Linear Motors Bosch Rexroth AG R911330592_Edition 06 ...
Страница 90: ...82 197 MCL Ironless Linear Motors Bosch Rexroth AG R911330592_Edition 06 ...
Страница 104: ...96 197 MCL Ironless Linear Motors Bosch Rexroth AG R911330592_Edition 06 ...
Страница 162: ...154 197 MCL Ironless Linear Motors Bosch Rexroth AG R911330592_Edition 06 ...
Страница 174: ...166 197 MCL Ironless Linear Motors Bosch Rexroth AG R911330592_Edition 06 ...
Страница 196: ...188 197 MCL Ironless Linear Motors Bosch Rexroth AG R911330592_Edition 06 ...
Страница 198: ...190 197 MCL Ironless Linear Motors Bosch Rexroth AG R911330592_Edition 06 ...
Страница 204: ...Notes 196 197 MCL Ironless Linear Motors ...
Страница 205: ...Notes MCL Ironless Linear Motors 197 197 ...