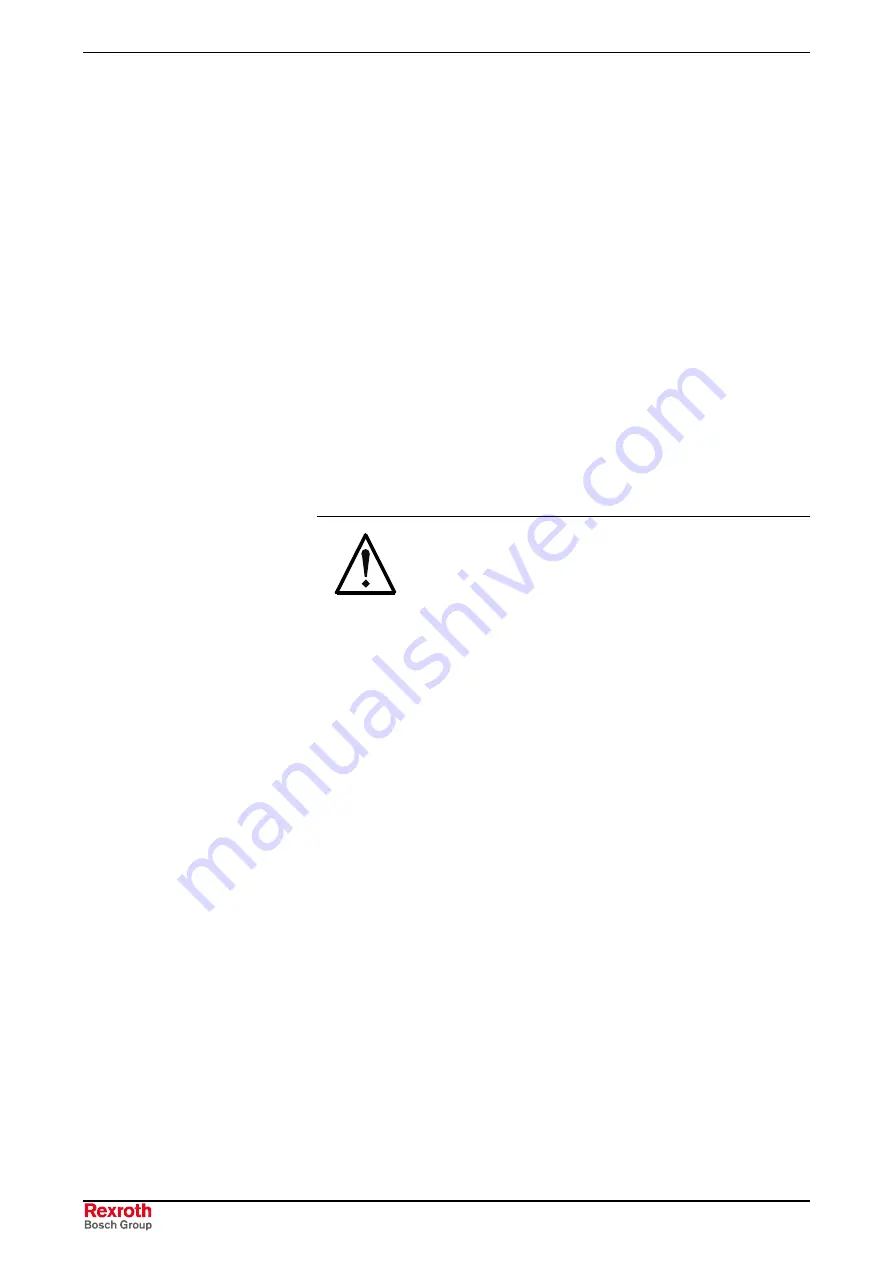
3-6
Safety Instructions for Electric Drives and Controls
VDP 16.1, VDP 40.1 and VDP 60.1
DOK-SUPPL*-VDP16/40/60-PR02-EN-P
3.7
Protection Against Dangerous Movements
Dangerous movements can be caused by faulty control of the connected
motors. Some common examples are:
•
improper or wrong wiring of cable connections
•
incorrect operation of the equipment components
•
wrong input of parameters before operation
•
malfunction of sensors, encoders and monitoring devices
•
defective
components
•
software or firmware errors
Dangerous movements can occur immediately after equipment is
switched on or even after an unspecified time of trouble-free operation.
The monitoring in the drive components will normally be sufficient to avoid
faulty operation in the connected drives. Regarding personal safety,
especially the danger of bodily injury and material damage, this alone
cannot be relied upon to ensure complete safety. Until the integrated
monitoring functions become effective, it must be assumed in any case
that faulty drive movements will occur. The extent of faulty drive
movements depends upon the type of control and the state of operation.
DANGER
Dangerous movements! Danger to life, risk of
injury, severe bodily harm or material damage!
⇒
Ensure personal safety by means of qualified and
tested higher-level monitoring devices or measures
integrated in the installation. Unintended machine
motion is possible if monitoring devices are disabled,
bypassed or not activated.
⇒
Pay attention to unintended machine motion or other
malfunction in any mode of operation.
⇒
Keep free and clear of the machine’s range of motion
and moving parts. Possible measures to prevent
people from accidentally entering the machine’s range
of motion:
- use safety fences
- use safety guards
- use protective coverings
- install light curtains or light barriers
⇒
Fences and coverings must be strong enough to
resist maximum possible momentum, especially if
there is a possibility of loose parts flying
off.
⇒
Mount the emergency stop switch in the immediate
reach of the operator. Verify that the emergency stop
works before startup. Don’t operate the machine if the
emergency stop is not working.
⇒
Isolate the drive power connection by means of an
emergency stop circuit or use a starting lockout to
prevent unintentional start.
⇒
Make sure that the drives are brought to a safe
standstill before accessing or entering the danger
zone. Safe standstill can be achieved by switching off
the power supply contactor or by safe mechanical
locking of moving parts.
Содержание Rexroth IndraControl VDP 16.1
Страница 6: ...IV Contents VDP 16 1 VDP 40 1 and VDP 60 1 DOK SUPPL VDP16 40 60 PR02 EN P ...
Страница 14: ...1 8 System Presentation VDP 16 1 VDP 40 1 and VDP 60 1 DOK SUPPL VDP16 40 60 PR02 EN P ...
Страница 30: ...4 4 Technical Data VDP 16 1 VDP 40 1 and VDP 60 1 DOK SUPPL VDP16 40 60 PR02 EN P ...
Страница 44: ...5 14 Dimensions VDP 16 1 VDP 40 1 and VDP 60 1 DOK SUPPL VDP16 40 60 PR02 EN P ...
Страница 58: ...6 14 Display and Operating Components VDP 16 1 VDP 40 1 and VDP 60 1 DOK SUPPL VDP16 40 60 PR02 EN P ...
Страница 68: ...7 10 Interfaces VDP 16 1 VDP 40 1 and VDP 60 1 DOK SUPPL VDP16 40 60 PR02 EN P ...
Страница 72: ...9 2 Touch Screen Software VDP 16 1 VDP 40 1 and VDP 60 1 DOK SUPPL VDP16 40 60 PR02 EN P ...
Страница 82: ...12 4 Index VDP 16 1 VDP 40 1 and VDP 60 1 DOK SUPPL VDP16 40 60 PR02 EN P ...
Страница 89: ......