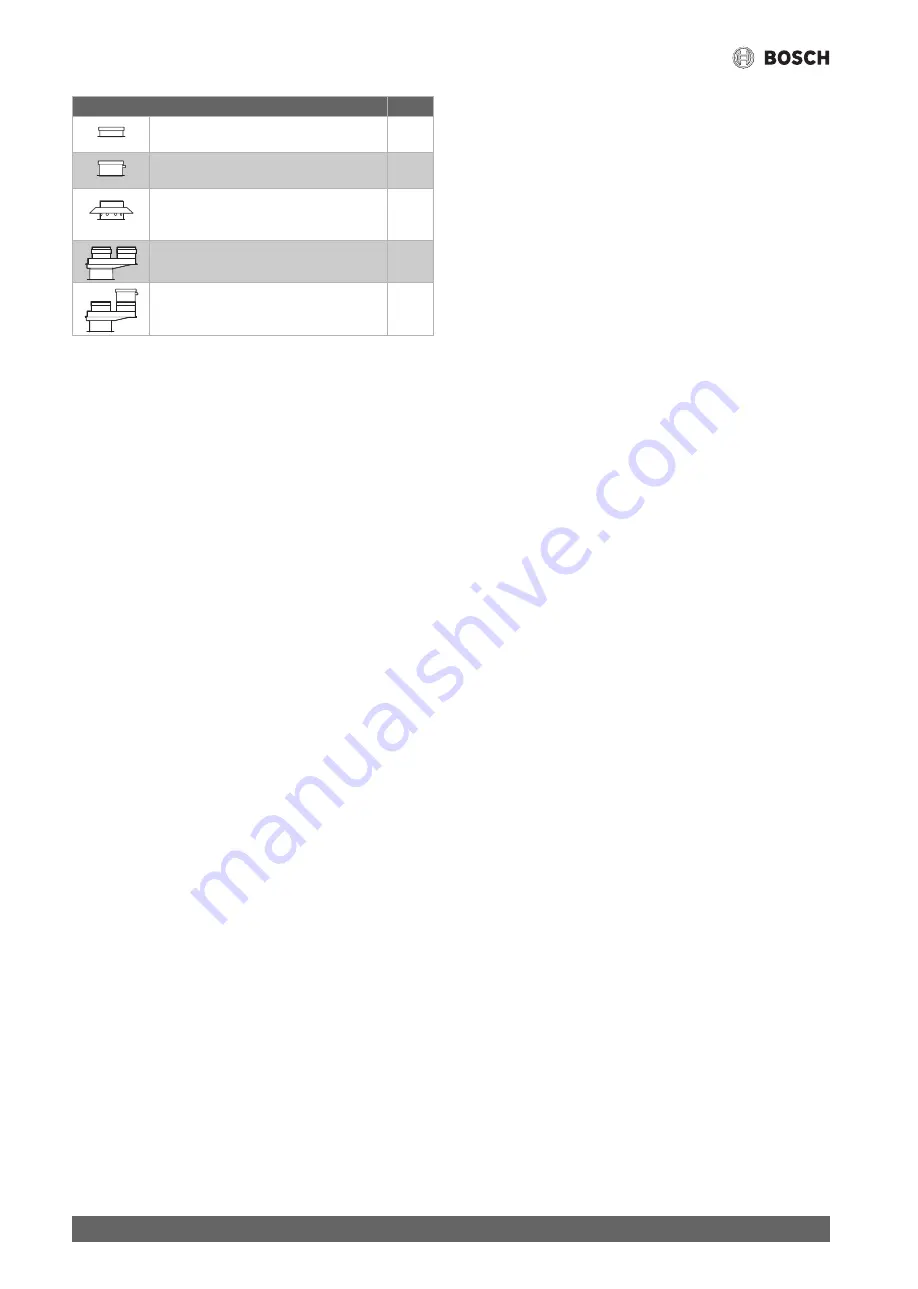
Product Information
Gaz 6000 W – 6720866247 (2019/07)
8
Table 5 Clearance B depending on the flue accessories for vertical flue
pipe
Flue gas accessories
B [mm]
Ø 60/100 mm
Connection adapter Ø 60/100 mm
≥ 170
Ø 60/100 mm
Vertical condensate drain Ø 60/100 mm
≥ 220
Ø 80 mm
Connection adapter Ø 60/100 mm with
combustion air supply
≥ 200
Ø 80/80 mm
Separate pipe connection Ø 80/80 mm
≥ 210
Ø 80/80 mm
Separate pipe connection Ø 80/80 mm,
vertical condensate drain Ø 80 mm
≥ 290
Содержание Gaz 6000 W
Страница 50: ......
Страница 51: ......
Страница 52: ...Bosch Thermotechnik GmbH Junkersstrasse 20 24 D 73249 Wernau www bosch thermotechnology com ...