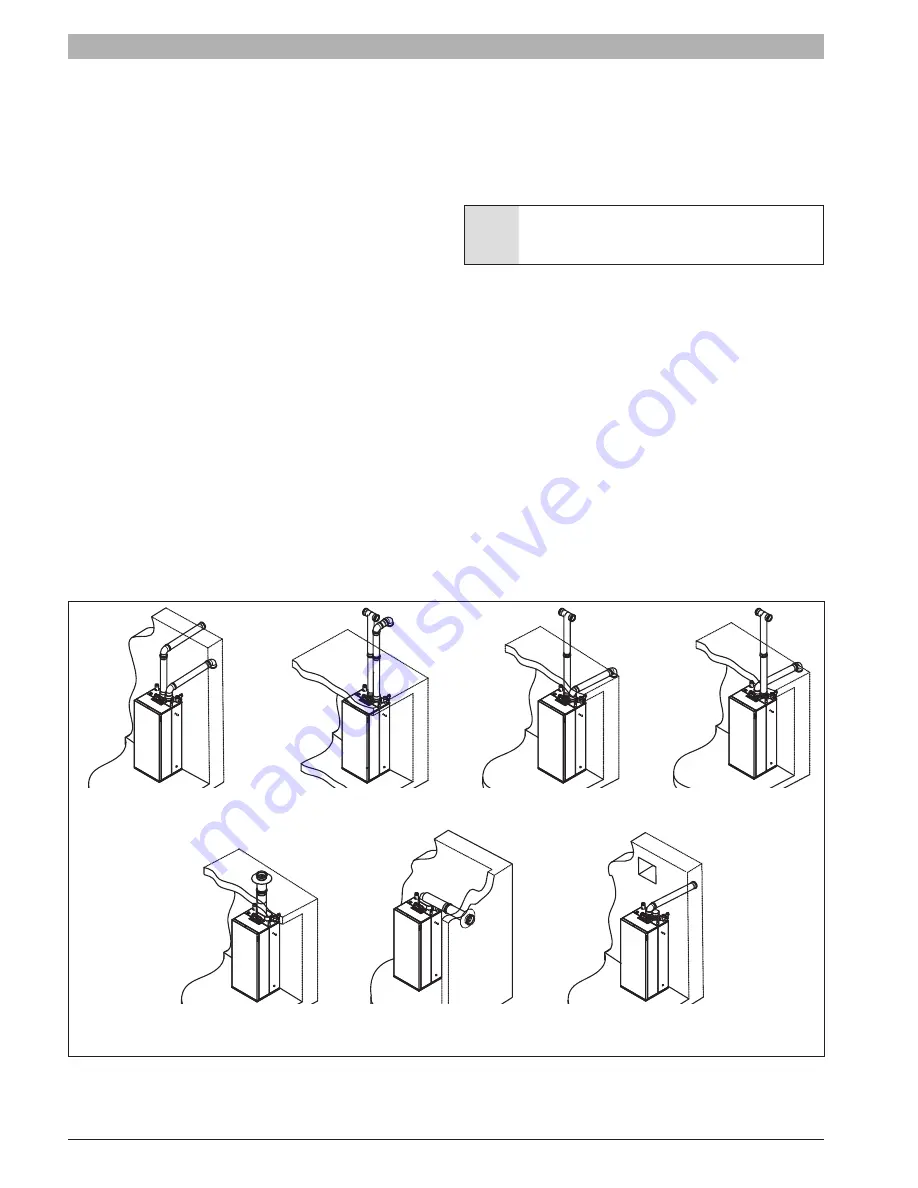
6720818454 (2016/02) US
SSB
24 | Installation
•
Remodeling areas;
•
Garages with workshops.
4 .7 .1
General venting and combustion air piping system
The SSB boilers require an approved vent system-designed for positive
pressure.
Vent connectors serving appliances vented by natural draft shall not be
connected to any portion of mechanical draft systems operating under
positive pressure.
Ensure that the flue pipes and seals are not damaged.
Use only primer and glue compounds approved for use with the vent
material used.
Never install a barometric or a thermally controlled vent damper with this boiler.
Do not route the flue system piping through or inside another duct that is
used for exhausting air or other flue gases.
The condensate trap must be primed at all times. Failure to do so may
allow combustion gases to escape into boiler room.
The unit is to be used for either direct vent installation or for installation
using room air for combustion. When room air is used, it is necessary to
provide an adequate opening for the fresh air intake.
You must use any of the vent/air piping methods shown in this manual.
Be sure to locate the unit such that the vent and combustion air piping
can be routed through the building and properly terminated.
The boiler / vent installation must be in accordance with Venting
of Appliances, of the latest edition of the National Fuel Gas Code,
ANSI Z223.1/NFPA 54 or section, Venting Systems and Air Supply
for Appliances, of the CAN/CSA B149.1, Natural Gas and Propane
Installation code or applicable provisions of the local, state and federal
building codes.
All vent pipes must be installed according to the vent manufacturer’s
instructions.
The exhaust vent and the combustion air inlet lines must be supported to
prevent sagging per the vent manufacturer’s instructions.
Do not mix components from different systems. The vent system could
fail, causing leakage of flue products into the living space. Use only
approved materials.
Use of cellular core PVC and CPVC for venting system is not allowed.
a
a
WARNING: Improper venting due to failure to comply with
the warnings above can result in excessive levels of carbon
monoxide!
The exhaust pipe must be pitched a minimum of a 1/4 inch per foot back
to the boiler (to allow drainage of condensate).
The vent system shall be installed so as to prevent the accumulation of
condensate.
Consult local and state codes pertaining to special building code and fire
department requirements. Adhere to national code requirements.
Observe the listed maximum lengths of vent system, which are boiler
model dependent
To avoid moisture and frost build-up and to maintain clearances to openings
on adjacent structures, 45 ° and 90 ° elbows or tees may be attached to
the end of the vent termination pipe to direct exhaust plumes away from
the adjacent structure. The total allowable vent length, maximum number of
elbows and distance to air intake restrictions must be adhered to.
Due to the high efficiency of the unit it may discharge what looks like
white smoke especially when the outside air temperature is cold. This
is due to the presence of water vapor, normally present in the exhaust
gases.
The following figure shows the acceptable piping installation for venting
and combustion air.
Fig. 25
Two pipes side wall
(Direct venting)
Two pipes vertical
(Direct venting)
Air intake side wall,
vent vertical
(Direct venting)
Air intake vertical,
vent side wall
(Direct venting)
Concentring
vertical pipe
(Direct venting)
Concentring side
wall pipe
(Direct venting)
One pipe venting
side wall (or vertical)
(Not direct venting)
Содержание Buderus SSB255
Страница 66: ...6720818454 2016 02 US SSB 66 Spare parts Notes ...
Страница 67: ...SSB 6720818454 2016 02 US Spare parts 67 Notes ...